5minlab, a software development studio, has released an independent simulator that models the fused deposition modeling (FDM) 3D printing workflow within a detailed, interactive environment. Titled 3D Printer Simulator, the software is now available on Itch.io, allowing users to navigate the entire process from slicing digital models to observing layer-by-layer deposition—all without consuming physical materials.
Interactive Simulation of Real-World Printing Dynamics
Users interact with a virtual printer emulating the mechanical structure of a real Ender 3 system. The simulation reproduces nozzle movement, retraction, filament flow rate, Bowden pressure lag, and other variables. Users can load pre-sliced G-code or generate slices directly within the app. A freely movable camera and adjustable lighting aid in visualizing individual print layers, while a nozzle transparency toggle offers clearer views. The environment is set in a realistic warehouse-style workspace to mimic an authentic workshop scenario.

Real-time rendering of the popular 3D Benchy test model in the virtual simulator
Advanced Parameters and Compatibility
Settings allow modifying print speed, time-lapse acceleration, and reproducing physical phenomena like layer lines and stringing. The tool also simulates geometry-specific behaviors, including visible seam accumulation and retraction effects. While supporting G-code from common slicers (e.g., Ultimaker Cura and OrcaSlicer), the developers have addressed compatibility issues with Klipper-specific macros and relative extrusion commands in recent patches.
Future Development Roadmap
Upcoming updates aim to expand supported printer types, including CoreXY, Delta, and inverted configurations, with plans to enable dual extrusion and multi-color printing. The team also intends to simulate advanced variables like pressure advance, input shaping, resonance, and the impact of hardware geometry on print quality. Long-term goals include exploring non-planar slicing visualization and “spaghetti print” failure simulation.
System Requirements
- Processor: 9th Gen Intel Core i5 or AMD Ryzen 5 3000 series
- Memory: 8 GB RAM
- Graphics: Discrete GPU with ray tracing support (e.g., NVIDIA RTX 2060+/AMD RX 6000+)
Built with Unreal Engine and enabling real-time ray tracing, the simulator currently relies on hardware-accelerated ray tracing due to unoptimized lighting and rendering resources. Distributed as a ZIP file, it requires manual extraction and execution. Features include time-lapse capture and exporting builds as GLTF for further visualization or animation.
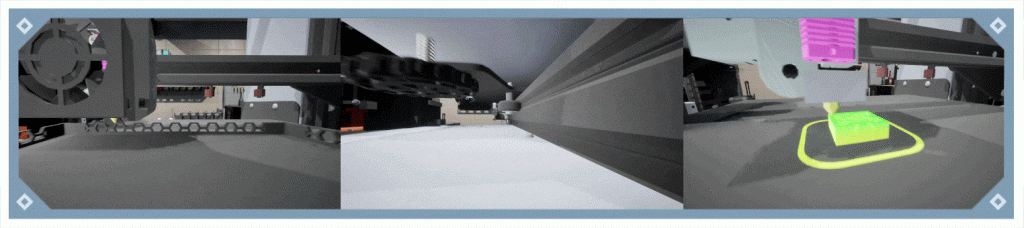
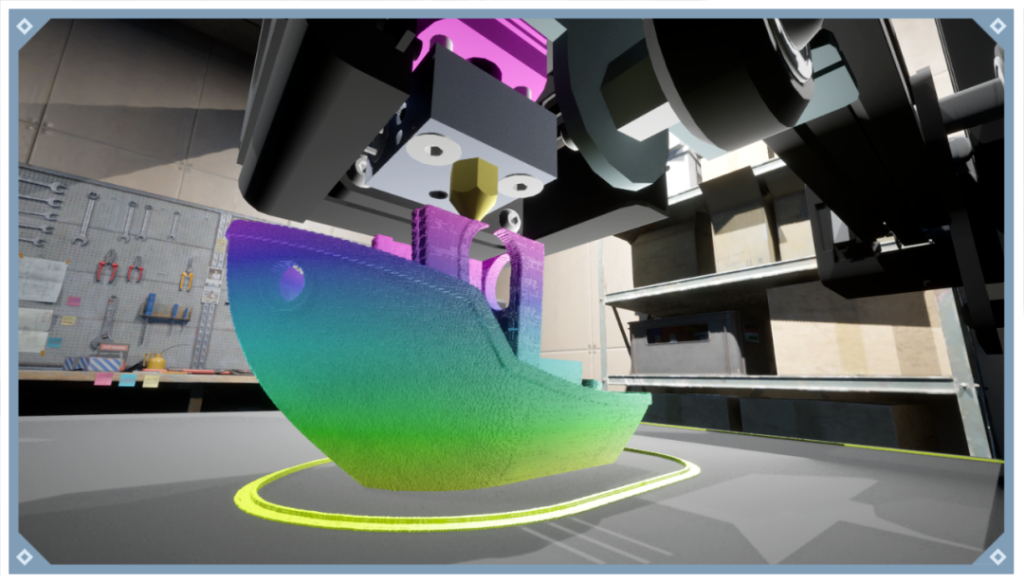
The simulator provides dynamic views of nozzle motion, print geometry, and extrusion behavior
Accelerating Virtualization in 3D Content Creation
Tencent’s recent release of Hunyuan3D 2.0 reflects the shift toward end-to-end digital asset generation. The platform separates geometry and texture processing pipelines via Hunyuan3D-DiT and Hunyuan3D-Paint to produce 3D models with stronger input-output consistency. With Hunyuan3D-Studio supporting low-poly stylization and rigging, the toolset aims to simplify animation, prototyping, and potential applications in additive manufacturing. While not designed for 3D printing, its open framework and export capabilities may adapt to desktop or industrial printing workflows.
Roblox has taken a similar approach with Cube 3D, a generative model converting natural language prompts into structured, engine-ready 3D meshes. Trained on native assets within the Roblox ecosystem, it uses an autoregressive transformer architecture to predict object geometry token-by-token. While focused on in-game content, Cube 3D’s open-source nature and “mesh-first” generation method hint at new potentials beyond entertainment—such as AI-assisted design tools. Future updates may support scene-level generation and multimodal prompting.
For more information, contact Debaolong Seiko. You are welcome to upload your designs to Debaolong Seiko for a quotation.