Carbon fiber stands as one of the most advanced materials of our era, thanks to its unparalleled properties. Today, it’s integral to aircraft, spacecraft, Formula 1 cars, and more—objects that demand both speed and minimal fuel consumption. The world is undergoing a transformative shift: aircraft components are transitioning from aluminum and steel to carbon fiber. This article explores carbon fiber’s many applications and why it’s reshaping industries. Let’s start with the basics.
What is Carbon Fiber and Why is it Popular in Machining?
“Fiber” refers to extremely fine filaments, and carbon fiber is a composite material made from ultra-thin carbon strands bonded with epoxy resin. Rarely used alone, it forms carbon composites when combined with an epoxy matrix. Due to high demand, it’s typically machined into carbon fiber plates or tubes.
Understanding Carbon Fiber Properties
Before diving into properties, knowing its composition is key.
What is Carbon Fiber Made Of?
Surprisingly, carbon fiber originates from organic polymers, primarily polyacrylonitrile (PAN). It consists of 90% carbon atoms arranged in a crystalline structure.
What Makes Carbon Fiber Special?
The magic lies in its 90% carbon atoms arranged in a crystalline pattern, granting exceptional properties: it’s stronger than steel while being remarkably lightweight.
- Lightweight and Strong
The most celebrated trait is its high strength-to-weight ratio, making it invaluable in aerospace, automotive, and sports equipment. - High Modulus and Fatigue Resistance
Carbon fiber boasts a modulus of 200–800 GPa (far exceeding steel) and can withstand millions of cyclic stresses before failure, a key advantage for aircraft wings.
Advantages of Carbon Fiber in Manufacturing
Carbon fiber enhances durability and performance while reducing fuel consumption (and costs). It also resists high temperatures effectively.
Common Applications of Machined Carbon Fiber Parts
Its high strength and low weight make carbon fiber ideal for structural components across industries:
Aerospace Industry
The strength-to-weight ratio drives its use in critical parts like fuselages and rotor blades, saving fuel and increasing speed.
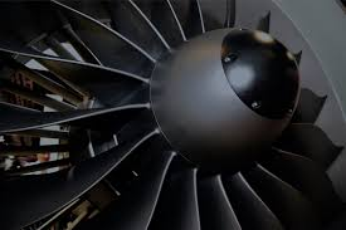
Automotive Industry
Lightweight high-performance vehicles, such as components like the hood, chassis, and spoiler of Formula One cars, can enhance speed and control
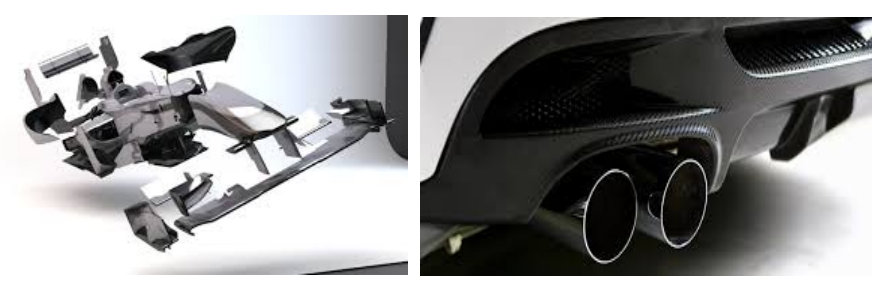
Sports Equipment and Consumer Goods
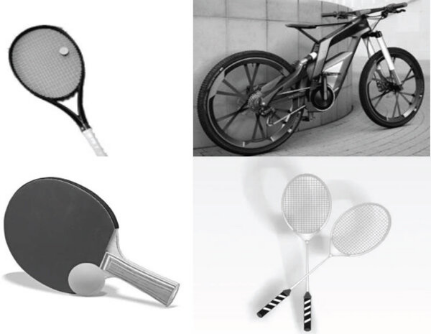
Bicycles: Lighter, stronger frames.
Golf Clubs: Improved speed and accuracy.
Tennis Rackets: Greater power and control.
Carbon Fiber CNC Machining: Techniques and Tools
Carbon fiber’s unique properties make machining challenging, requiring precision tools and careful handling.
- CNC Milling for Carbon Fiber Parts
CNC milling creates objects by cutting material from flat or rectangular samples, offering:- Automatic tool changing reduces downtime, boosting productivity by 10–15% with advanced CAM software.
- Tight tolerances (±0.025 mm) and surface finishes (Ra <0.8 µm).
- CNC Turning and Lathe Techniques
Ideal for cylindrical/tubular parts (connectors, bushings, shafts), where the workpiece rotates while a fixed tool removes material:- 30% faster than milling for symmetrical designs.
- Maintains 0.05 mm runout for balanced rotating parts.
- 25% more cost-effective than milling due to lower material waste.
- Drilling and Cutting Carbon Fiber Plates
- Drilling Key Techniques:
- Carbide drills at 3,000–5,000 RPM with 118° angles prevent tearing.
- Peck drilling (retracting every 2–3 mm) clears dust and keeps temperatures below 200°C.
- Core drills minimize inner wall chipping.
- Edge Cutting:
- Spiral bits at 18,000 RPM with 0.5–1.5 mm/min feed rates prevent delamination.
- Spray cooling or air 吹扫 (blowing) keeps temperatures below resin melting points.
- Drilling Key Techniques:
Challenges and Solutions in Carbon Fiber Machining
As a carbon fiber-reinforced polymer (CFRP) composite, it presents unique machining hurdles:
- Abrasive Nature and Rapid Tool Wear
Carbon fiber is 5–10 times more abrasive than glass fiber, quickly damaging traditional tools and causing surface roughness (leading to fatigue failure).- Solution: Use diamond-coated or carbide tools, far harder than HSS alternatives.
- Toxic Dust and Fumes
Carbon dust particles (<5 microns) are potential carcinogens and can short-circuit CNC electronics.- Solution: HEPA vacuum systems (capturing 99.66% of dust) or wet cutting (reducing particles by 90%).
- High Scrap Costs
CFRP is expensive, so suboptimal cutting parameters can raise scrap rates by 15–25%.- Solution: Optimize settings:
- Spindle speed: 18,000–24,000 RPM (prevents resin melting)
- Feed rate: 0.05–0.1 mm/tooth (reduces fiber pull-out)
- Cut depth: ≤0.5 mm (minimizes delamination)
- Solution: Optimize settings:
- Delamination and Surface Damage
Layer separation during drilling/trimming reduces strength by 50–60%.- Solution: High-precision CNC machines with automatic tool changing, stable workholding, and advanced cutting strategies (e.g., carbon fiber CNC services).
Cutting Carbon Fiber: Methods and Equipment
CFRP’s anisotropic nature (property variation with direction) and heat-sensitive resin make cutting complex:
- Waterjet Cutting
High-pressure water (60,000–90,000 psi) mixed with abrasive particles cuts carbon fiber without:- Thermal damage zones
- Mechanical stress to adjacent parts
- Ensures high-precision cuts
- Laser Cutting: Pros and Cons
- Pros: 10x faster than waterjet, suitable for high-volume production, higher precision.
- Cons: Creates thermal damage zones, emits toxic gases, optimal for thicknesses <3 mm.
- Abrasive Cutting Techniques
Method | Best For | Key Advantages | Limitations |
---|---|---|---|
Diamond Band Saw | Thick CFRP (>25 mm) | No heat generation, portable | 0.5–1.0 mm kerf waste |
Diamond GrindingWheel | Edge finishing | 0.05 mm precision bevels | Requires flood coolant |
Ultrasonic Cutting | Delicate laminates | 60% less delamination | Equipment cost >$75k |
Essential Tools for Machining Carbon Fiber Parts
- Diamond-Coated Cutting Tools
Ideal for reducing wear and improving surface finish on this abrasive material. - High-Speed, High-Rigidity CNC Machines
- 25,000–60,000 RPM controls fiber pull-out.
- Harmonic control minimizes vibration at composite interfaces.
- Achieves Ra 0.1 µm surface finishes.
- CFRP-Specific Composite Cutters
Innovations include diamond-like carbon (DLC) coatings, through-tool coolant, and ultrasonic assistance.
Safety Measures for Carbon Fiber Machining
- Personal Protective Equipment (PPE)
Use goggles, respirators, and suits to prevent lung irritation and skin rashes from toxic fumes and particles. - Ventilation and Air Filtration
Filter Type | Efficiency |
---|---|
HEPA (H13) | 99.95% @ 0.3 µm |
ULPA (U15) | 99.9995% @ 0.1 µm |
- Waste Management
Recycle scraps and comply with local hazardous waste regulations to minimize environmental impact.
Conclusion
Carbon fiber is a transformative material for aerospace, automotive, and beyond. Its machining challenges drive advancements in CNC technology, with Industry 4.0 shaping the future through automation and AI optimization. Staying ahead requires embracing smart innovations.
For more insights, contact Debaolong Seiko. Upload your designs to Debaolong Seiko for a customized quote.