What is a Turbocharger Impeller?
A turbocharger impeller is a crucial rotating component within the turbocharger, designed to compress the air entering the engine. This compression enhances the engine’s oxygen supply, improving fuel combustion efficiency and boosting torque and power. Impellers are aerodynamically designed to withstand high pressure and temperatures.
Turbo Impeller and Compressor Impeller
The turbocharger impeller consists of two main parts: the turbine wheel and the compressor wheel, connected by a shaft. The turbine wheel is driven by engine exhaust gases, rotating the shaft which powers the compressor wheel. The compressor wheel inhales and compresses air, delivering it to the engine to improve combustion and power output.
Difference: Impeller vs. Other Turbocharger Components
The impeller is the rotating wheel in the turbocharger that compresses the intake air. Other components, such as the turbine housing, compressor housing, or turbine, serve different roles: the turbine drives the compressor impeller using exhaust energy, while the housings guide the airflow.
How Does a Turbocharger Impeller Work?
As the core component of the turbocharger, the impeller is located on the intake side. It inhales and compresses air, which then flows through the engine to facilitate fuel combustion and generate higher power. In short, the impeller is vital for enhancing engine performance.
How Turbocharger Impellers Improve Engine Efficiency
Also known as compressor impellers, they improve engine efficiency by forcefully compressing air into the engine. This allows the engine to produce the same power with a smaller displacement, ultimately enhancing fuel economy and reducing emissions.
How Impeller Speed and Flow Affect Power
Impeller speed (RPM) and flow rate directly correlate with the pump’s power demand. Higher speeds and larger-diameter impellers lead to higher flow rates and increased power consumption, though this relationship is not always linear.
Why Impeller Size Is Crucial for Turbo Performance
Impeller size directly impacts turbocharger performance by influencing airflow, boost pressure, and engine power output. An optimally sized impeller ensures efficient airflow, higher boost, and avoids performance limitations like engine overload or turbo lag.
Turbocharger Impeller Design: Key Considerations
Factors Influencing Impeller Shape and Size
Impeller design is significantly affected by blade shape and angle, diameter, width, curvature, and flow velocity, which in turn impact overall energy consumption, pressure, and efficiency.
Blade Profile and Geometry
Blade profiles and geometry affect the performance of centrifugal pumps, directly influencing factors like head, power output, or efficiency. The shape, angle, curvature, and number of blades impact flow patterns and energy transfer within the pump. Optimizing these factors enhances efficiency.
Importance of Blade Angles
Blade angles influence impeller performance, flow characteristics, and efficiency. The inlet angle affects how fluid enters the impeller, with optimized angles minimizing turbulence and improving flow efficiency. The outlet angle determines how fluid exits, impacting the pressure and head generated.
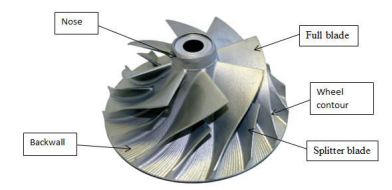
Impeller Blade Details: Radial vs. Axial Design
Radial and axial impellers differ in airflow direction, efficiency, and pressure generation, making them suitable for different applications:
- Axial impellers direct fluid parallel to the shaft, ideal for high-flow, low-pressure uses like ventilation.
- Radial impellers push fluid outward from the center, suitable for high-pressure applications or airflow through pipes.
Types of Turbocharger Impellers
Based on airflow direction, turbocharger impellers can be categorized into:
Axial Flow Impellers
In these impellers, fluid flows parallel to the shaft (vertically), known for creating strong vertical currents. They are ideal for mixing liquids and suspending solids.
- Advantages:
- Designed for high-volume fluid movement.
- Suitable for low-pressure, large-capacity applications.
- Strong vertical flow suspends solids to prevent sedimentation.
- Works with stratified liquids in tanks.
- Achieves high RPM with low energy consumption.
- Disadvantages:
- Unsuitable for high-viscosity fluids.
- Improper baffle installation can cause vortexes and poor mixing.
- Expensive due to large propeller blade size.
- Applications:
- Mixing and blending fluids requiring solid suspension.
- Low-head water pumping for irrigation and flood control.
- Circulating water in power plant cooling systems.
- Liquid circulation in chemical processes like evaporation and crystallization.
- Wastewater treatment and sewage digestion.
Radial Flow Impellers
These impellers have blades perpendicular to the shaft, pushing fluid outward to generate high pressure and low flow.
- Advantages:
- Produce high pressure, suitable for high-altitude or high-resistance pumping.
- Ideal for applications like mixing pigment pastes, offering high shear force.
- Versatile, handling fluids with varying temperatures and viscosities.
- Efficiently convert mechanical energy to fluid flow.
- Suitable for gas dispersion.
- Disadvantages:
- Sensitive to viscosity changes, which affect performance.
- Lower flow rates compared to other impellers.
- Prone to vortexes, not suitable for all applications.
- Applications:
- High-pressure water supply and irrigation.
- Firefighting systems due to high-pressure capability.
- Industrial and commercial uses (circulation pumps, machine tools, boiler feed pumps).
- Mixing and dispersing to form uniform mixtures.
- Achieving high discharge pressure in multi-stage pumps.
Mixed Flow Impellers
Combining features of radial and axial pumps, mixed flow impellers have neither purely radial nor axial flow patterns. They are versatile for water supply and cooling systems.
- Advantages:
- Handle fluids with varying densities and viscosities.
- Effective for medium-pressure head applications.
- Pump turbid liquids or those with suspended solids.
- Combine radial and axial flows for diverse patterns.
- Disadvantages:
- More complex than radial/axial impellers, increasing manufacturing costs.
- Unsuitable for extremely low or high head applications.
- Limited speed range between radial and axial configurations.
- Applications:
- Water supply, intake, and distribution systems.
- Large-scale irrigation projects.
- Cooling systems requiring mixed flow patterns.
- Handling contaminated or turbid liquids (e.g., paper pulp in paper mills).
- Dewatering applications and marine jet propulsion systems.
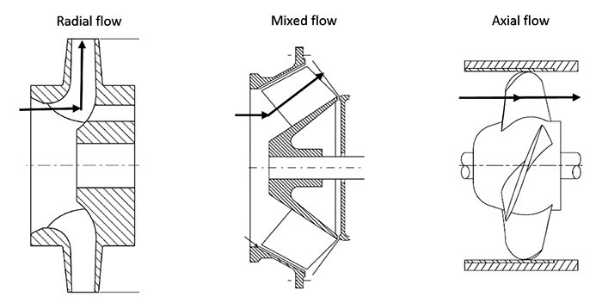
Common Materials for Turbocharger Impellers
Turbocharger impellers typically use stainless steel and titanium alloys. For high-temperature and lightweight needs, materials like nickel-based alloys or composites are employed.
- Stainless Steel Alloys: Offer good strength and corrosion resistance, ideal for high-temperature/high-pressure applications (e.g., AISI 4063 steel). Low-carbon C1045ss (carbon steel) is less commonly used directly in impellers.
- Nickel-Based Alloys & Aluminum Alloys: Nickel alloys (e.g., Inconel 718) are preferred for turbine wheels due to high temperature and strength resistance. Aluminum alloys, with low density, are used for compressor wheels to reduce inertia and improve engine response.
- Titanium Alloys in Impellers: Titanium alloys combine strength, corrosion resistance, and light weight, widely used in high-temperature/high-speed applications. Both compressor and turbine impellers favor titanium for its strength-to-weight ratio.
- Composites in Lightweight Impellers: Composites like carbon fiber-reinforced polymers (CFRP) and fiberglass create lightweight impellers, reducing weight significantly while maintaining strength and durability. They are less common than stainless steel and used in specific applications to avoid failures.
Turbocharger Impeller Coatings
Coatings enhance impeller performance and durability. Common materials include PVD (Physical Vapor Deposition) and PACVD (Plasma-Enhanced Chemical Vapor Deposition), preventing scratches, wear, and friction oxidation. Carbon-based coatings are also used for their low friction coefficient in low-lubrication conditions.
How to Manufacture Precision Impellers?
Due to complex geometries, impeller manufacturing relies on 5-axis CNC machining, though challenges include high initial costs and the need for specialized training.
- 5-Axis CNC Machining for Impellers: This process uses 5-axis CNC machines to produce complex, precision components like impellers. The machines control multiple axes (e.g., A, B, X, Y) simultaneously, enabling shapes impossible with 3-axis machining.
- Advantages: High precision, control over tool movement, multi-directional tool paths for complex blade features, higher efficiency, reduced setup time, minimal human intervention, and excellent surface finish (critical for aerodynamics).
- Disadvantages: Higher initial costs than 3-axis machines, requires specialized training, and thin-walled parts may deform during machining.
- Main Machining Processes for Impellers:
- Create a 3D model of the impeller via CAD.
- Select materials (titanium, aluminum, stainless steel) based on requirements.
- Choose cutting tools (ball end mills, end mills) for desired properties.
- Generate CNC programming code from the CAD model.
- Clamp the workpiece and set up the machine.
- Machine the impeller through roughing and finishing operations.
- Thoroughly inspect the finished impeller.
How to Choose the Right Turbocharger Impeller for Your Engine
Selecting an impeller requires considering key factors: engine type, suitable impeller type, and material compatibility.
- Choose Impeller by Engine Type: Engine size and type determine airflow and boost pressure needs. Smaller impellers offer faster boost response, while larger ones deliver higher peak power. Also, consider vehicle usage and fuel type.
- Match Impeller Type to Performance Goals: Factors like impeller type (compressor/turbine), size, shape, blade count/angle, and compatibility with the turbo housing impact performance.
- Material Considerations for Impeller Durability: Common materials (stainless steel, aluminum, titanium) offer different strength, corrosion resistance, and weight properties. Impeller materials must withstand high speeds and temperatures.
Conclusion
Turbocharger impellers are key to enhancing engine power and efficiency, designed to compress intake air for better combustion and torque. Their manufacturing involves precise design, material selection, and 5-axis CNC machining.
For more information or to upload your design for a quote, contact Debaolong Seiko.