In the consumer AM market, sports remain one of the primary domains where 3D printing is making significant impacts. Several factors drive the eager adoption of 3D printing in sports goods, such as the unending mission to design more comfortable, safe, and high-performance products, as well as the demand to provide more customized options for professional and amateur athletes. In this article, we aim to highlight four areas within the broader sports industry where 3D printing is indeed helping to raise the standards.
1. Football Helmets
Player safety has become an increasingly critical part of professional football, a sport where athletes face significant risks of concussions and brain injuries. In recent years, 3D printing innovations have helped enhance helmet performance, with brands like Riddell, VICIS, and Xenith incorporating the technology into some of their professional-grade products.
Launched in April 2024, Riddell’s Axiom 3D helmet—designed for elite players including quarterbacks and offensive/defensive linemen—combines Axiom helmet technology with 3D-printed lattice liner technology. Players undergo head scans to ensure a perfect fit, after which the liners are 3D printed using Carbon’s Digital Light Synthesis (DLS) technology based on the scan data.
Riddell states that their partially 3D-printed helmets “create a personalized combination of energy-managing internal padding with unique thickness, shape, and contours to deliver comfort and protection.” Today, an increasing number of NFL professional football players opt for helmets with 3D-printed padding, with an estimated 240+ players wearing such helmets.
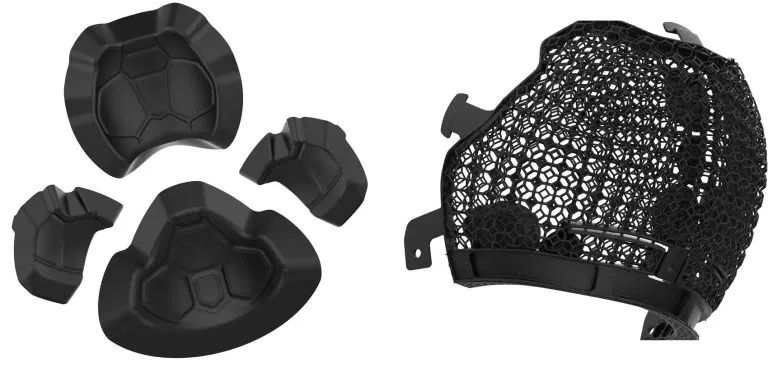
2. Golf Clubs
The growing popularity of metal additive manufacturing has helped the golf equipment industry develop new lightweight clubs that enhance player performance. One of the most significant promotions of 3D printing in golf product manufacturing comes from COBRA, which, after the successful launch of a limited-edition series of 3D-printed irons, now sells 3D-printed irons as part of its standard range.
COBRA’s 3D-printed Tour irons, based on the LIMIT3D and KING Tour irons, are produced using LPBF (Laser Powder Bed Fusion). This innovative club integrates a complex additive lattice structure that reduces weight by 33%, while its internal design lowers the mass of the clubhead to a lower position. This results in a lower center of gravity and a higher Moment of Inertia (MOI).
Another company using 3D printing to manufacture high-end golf clubs is Avoda Golf. Bryson DeChambeau used their custom 3D-printed clubs when winning the 2024 U.S. Open.
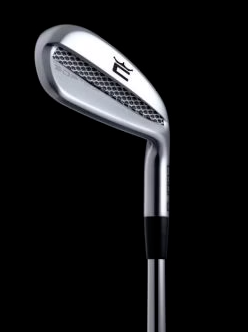
3. Bike Saddles
3D printing technology is no stranger to competitive cycling, and a key area of application in recent years has been the development of lightweight, rider-optimized saddles. Saddle design requires balancing rider comfort, weight, and performance, and data-driven lattice designs combined with 3D printing can help achieve this.
A leading brand in this field is Italian company Fizik, which partnered with Carbon in 2019 to bring its standard Adaptive 3D-printed saddle to market. Since then, Fizik has launched a fully rider-specific custom product—the One-to-One saddle—which uses technology from Germany’s GebioMized (a company specializing in cycling accessories and pressure mapping data) to generate custom lattices based on rider pressure map data. These designs are then realized using Carbon’s Digital Light Synthesis (DLS) technology.
Other performance cycling brands like Hanglun Technology, 22 Bicycles, and TITAN SUPER BOND specialize in using 3D printing to produce optimized lightweight bicycle frames from materials like titanium and aluminum.
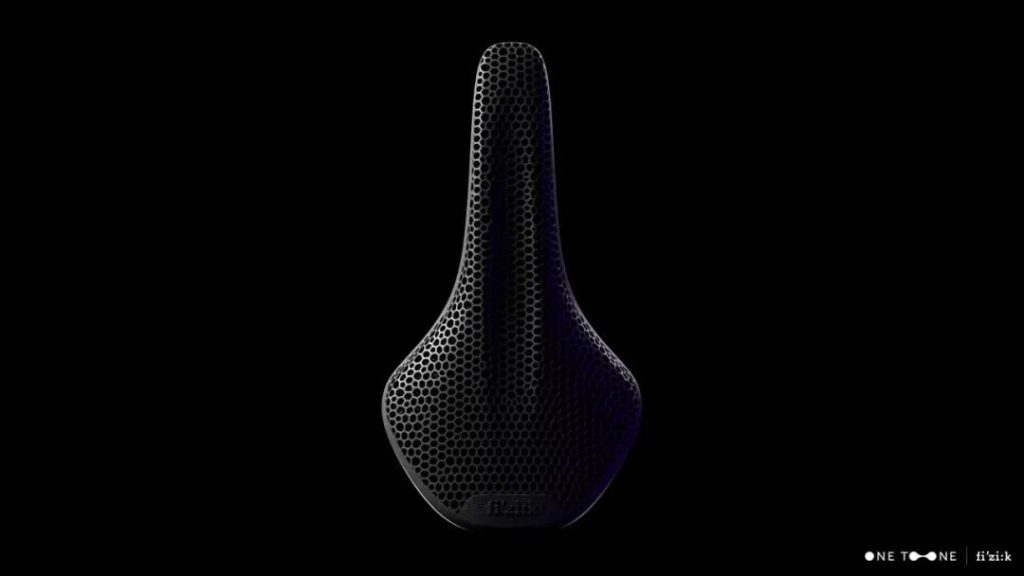
4. Paraglider Parts
Since November 2024, paraglider design and manufacturing company Ozone has been using 3D printing to produce adjustable riser control handles, maximizing pilot control. These critical components, known as elevator handles in the paragliding world, can now be fully customized to fit the pilot’s hand size. The result is better stability management during straight flight and higher precision during turns.
The 3D printing initiative is the result of a collaboration with French 3D printing bureau Sculpteo, whose on-demand 3D printing services enable Ozone to sell these custom parts in short lead times. The rapid process also allows for faster testing and validation of prototypes.
“We can now provide standardized components to customers in record time.”Ozone’s Marketing Manager and paraglider pilot Nicolas Cochet says. “Our pilots benefit from high-performance, fully customized equipment, leading to a safer flight experience.”
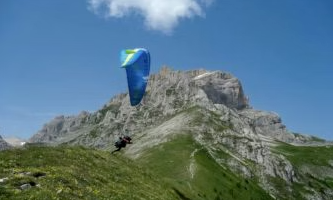
For more information, please contact Debaolong Seiko. You are also welcome to upload your designs to Debaolong Seiko for a quotation.