After the Fourth Industrial Revolution, manufacturing processes have advanced significantly, and CNC machining is one of them. It is a precision manufacturing process executed by computer software with core programming. There is much more to CNC manufacturing, and here we will discuss all the important aspects of CNC machining.
Introduction to CNC Machining
What is CNC Machining?
CNC stands for Computer Numerical Control. Computer control enables machines to perform tasks such as material removal, resulting in custom-designed components.
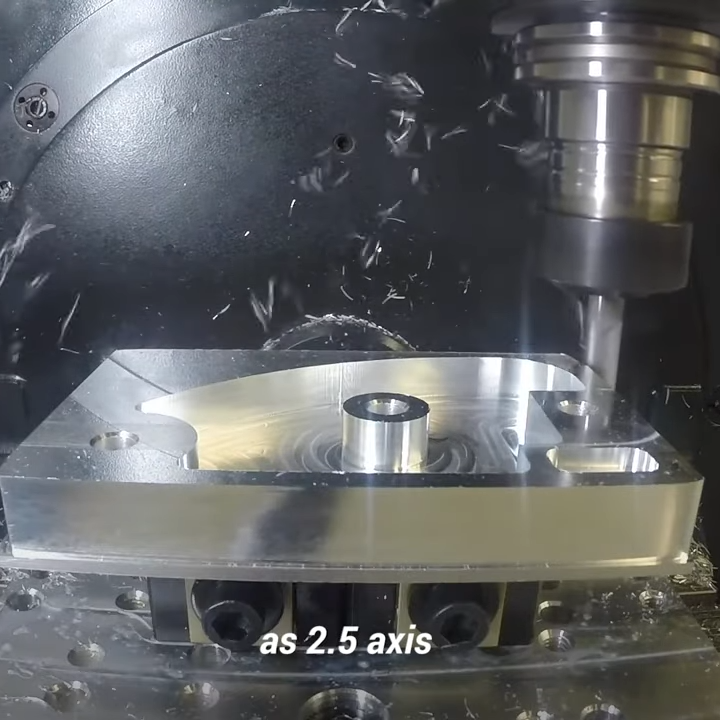
How Does CNC Machining Work?
In CNC production, materials rotate and move across different planes of the machine. 3D Computer-Aided Design (CAD) models guide computer programs that command a series of tasks, such as drilling, grinding, or lathe operations. These programs control tool movements and automatically execute tasks on the workpiece.
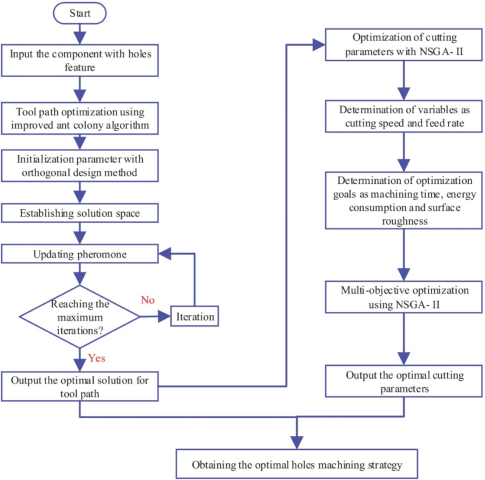
15 Advantages of CNC Machining
CNC manufacturing is globally renowned for numerous reasons. It offers manufacturers significant benefits in terms of error reduction and has replaced manual machining. The advantages of CNC machining are discussed below:
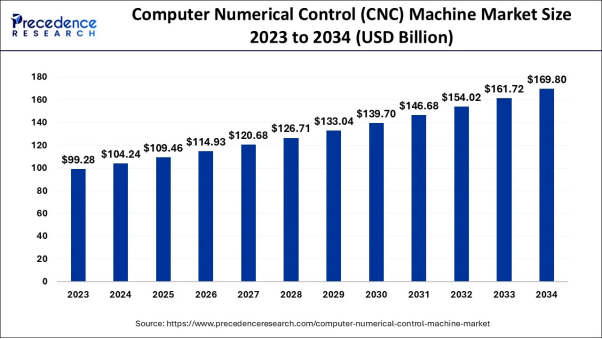
- Precision and Accuracy in Manufacturing
The primary advantage of CNC production is its precision and accuracy. Manufactured parts meet exact specifications without requiring constant oversight from experts or operators. Due to computer control, the risk of human error is negligible. However, some areas still require human attention for accurate results, such as operating environment, tool calibration, and tool wear. CNC production can achieve tolerances of at least 0.004 mm.Industries like defense and aerospace demand this high level of machining. Precision CNC machining produces intricate parts that enhance the overall efficiency of aircraft. - Improved Production Efficiency
CNC production begins when operators program the machine according to desired design specifications. Once the process starts, no CNC experts are needed, and parts are manufactured quickly. Mass production becomes convenient and easily scalable. CNC machines can be programmed to create prototypes or mass-produce parts. In summary, CNC projects have no limits, allowing manufacturers to expand their business efficiently with better workflows and minimal downtime. - Reduced Material Waste and Costs
CNC machining is highly efficient, with high precision minimizing material waste. The computer-controlled design ensures no accidental cuts, resulting in fewer damaged parts (e.g., scrap or discarded items). Machines cut with precise efficiency, reducing overall production costs for CNC projects. - Repeatability and Consistency in Production
CNC production controls exact speeds and positions. Precision CNC machining can manufacture thousands of identical parts with the same accuracy and precision in minimal time—a feat nearly impossible with traditional machining. Machines are designed to repeat cuts without compromising part quality. - Enhanced Manufacturing Flexibility
CNC machining offers exceptional flexibility, capable of producing parts with any complex design. Some machines feature advanced functions like automatic tool changers or one-click processes, enabling the production of versatile parts with intricate designs. - Improved Workplace Safety
CNC production is fully automated, eliminating the need for CNC professionals to be near cutting tools. This reduces safety incidents significantly, enhancing overall workplace safety. - Lower Labor Costs Through Automation
While CNC projects require higher initial capital investment, operational costs are extremely low. Minimal error rates, low production costs, reduced labor expenses, and minimal training make it a cost-effective method overall. Operators can learn machining operations virtually, reducing training and workshop costs. - Scalability for Mass Production
CNC machines have no limits on production volume. They can create prototypes or mass-produce parts with the same precision and design specifications in a short time. This allows manufacturers to scale their business and achieve mass production. CNC machines can be easily programmed to optimize mass production, helping businesses utilize resources and budgets effectively. - Support for Multiple Materials and Processes
CNC machining works with various materials, including metals, alloys, composites, and plastics. However, material selection depends on factors like stress resistance, high-temperature tolerance, design tolerances, and hardness. Processes such as milling, turning, drilling, or grinding can be performed on any material. - Improved Quality Control
Precision CNC machining ensures high design consistency, making it ideal for mass production with minimal errors. Optimal cutting parameters and high speeds enhance efficiency. CNC machines can operate 24/7 with full quality control, no CNC experts required. Once calibrated and adjusted, they perform tasks autonomously with superior quality control. - Faster Prototyping and Time-to-Market
Beyond high precision and design consistency, CNC machines reduce time-to-production for mass manufacturing. Faster prototyping and rapid mass production help scale businesses through CNC projects. Overall, CNC machining is the fastest, most cost-effective, and efficient manufacturing process. - Reduced Environmental Impact
CNC production is highly sustainable, with no carbon emissions. It consumes less energy—approximately 1/7 of the energy used by traditional methods. CNC machines operate at high speeds with minimal per-minute power consumption. - Seamless Integration with Computer-Aided Design (CAD)
CNC machines integrate easily with CAD and digital prototyping simulations. A single CAD drawing initiates fully automated production with high precision, quality control, and efficiency. - Longevity and Durability of CNC Machines
CNC machines have low operational costs, partly due to their durability and long lifespan. Maintenance costs are low, and no specialized personnel are needed for tool maintenance or machine calibration. - High Customization and Design Flexibility
CNC machines are versatile, highly customizable via design software, and capable of producing any complex shape. They outperform human engineers—with the right software, they can manufacture parts of any shape or size, even those designed virtually.
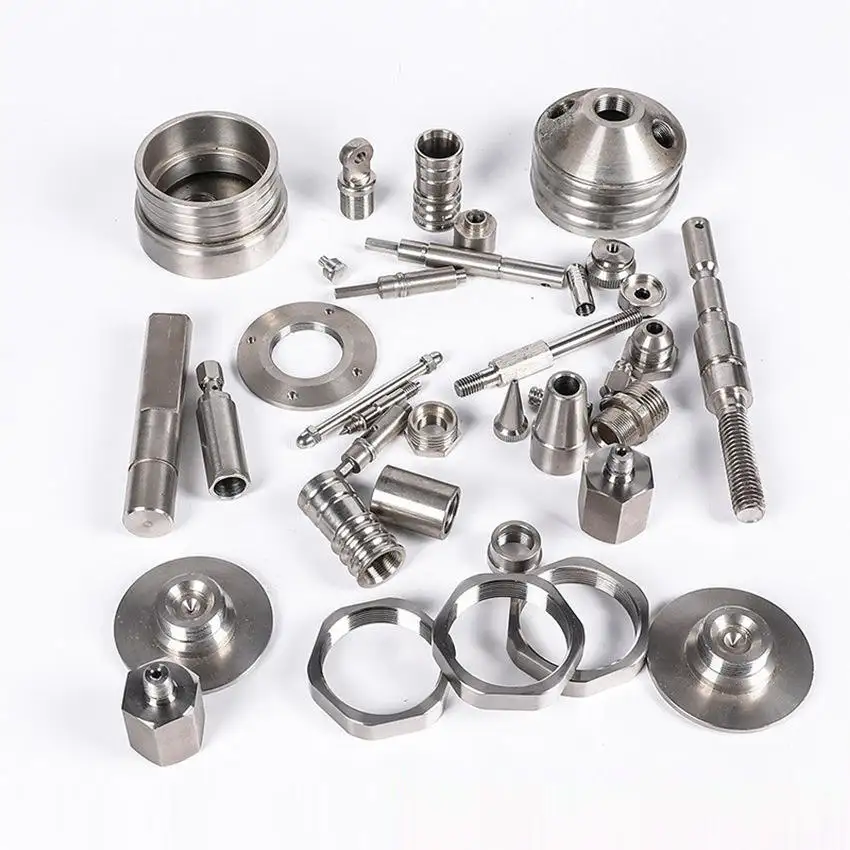
Debaolong Seiko Helps You Customize CNC Machined Parts
Debaolong Seiko is one of China’s top precision CNC machining manufacturers. We provide comprehensive one-stop solutions for CNC metal parts. Our CNC experts and skilled staff have years of experience in CNC manufacturing service design, CAD drafting, material selection, production processing and assembly, and quality inspection of CNC parts.