SFM (Surface Feet per Minute) is crucial for machinists as it ensures machining accuracy and tool lifespan. It is essentially a measure of the speed of the tool relative to the workpiece. Let’s discuss it further!
What Does SFM Stand for in Machining?
SFM is the abbreviation of “Surface Feet per Minute”. It is similar to the effective speed of a tool when traveling in a straight line. It helps machinists and CNC experts determine the correct RPM (Revolutions Per Minute), feed and speed spindle speed settings, and the right tool suitable for a specific material. Therefore, it is very important to optimally set the parameters of CNC and lathe machines to improve tool performance and operational accuracy.
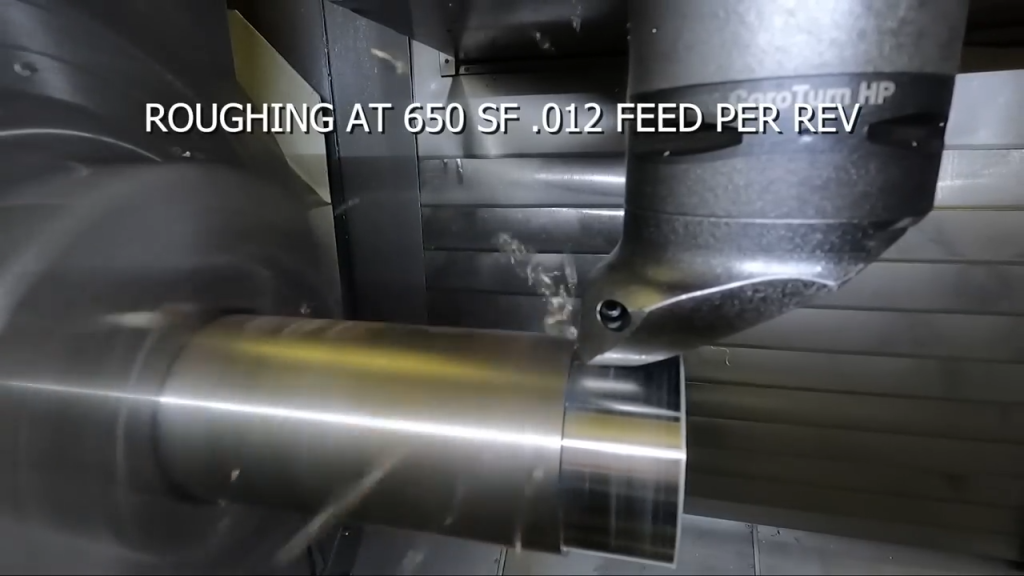
Is SFM Easy to Use?
Yes! It’s not a big project for machinists. Only a little formula is needed.
What is the Unit Used to Measure SFM?
Traditionally, SFM is an imperial unit because in the early days (1950s), machining was first adopted in the United States, and Americans used the imperial unit system with “feet” as the unit. However, later, as machining became common in other parts of the world, people became more accustomed to the SI unit system and began to use “millimeters” instead of “feet”. Therefore, it became “Surface Millimeters per Minute”.
SFM to RPM Calculation
Are SFM and RPM the Same?
As mentioned earlier, SFM uses “surface feet”, while RPM uses “revolutions per minute”. RPM mainly depends on motor specifications and thus on spindle speed. But SFM is the actual measurement of the distance covered by the tool per minute. Although the two are proportional, they cannot replace each other. There are many other factors that affect SFM, such as workpiece diameter or tool diameter. The chip load formula and IPM formula are also different from SFM and RPM, but they also depend on the feed rate.
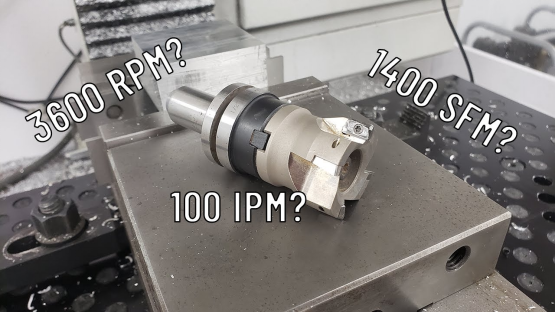
How to Calculate SFM in Machining?
The relationship between SFM, spindle speed (RPM), and tool or workpiece diameter is expressed as:
SFM = (π × D × RPM) / 12
Where:
- D: Diameter of the cutting tool (for milling) or workpiece (for turning) in inches
- RPM: Spindle speed (Revolutions Per Minute)
- 12: Conversion factor from inches per minute to feet per minute
Here is an example to better explain this:
Assume in our example, the workpiece diameter (D) is 12 inches and the RPM is 1500, then the SFM is:
SFM = (3.1416 × 12 × 1500) / 12
SFM = 4712.38 SFM
Factors Affecting SFM in Machining
Although there are many factors affecting SFM in machining, we will discuss material type, tool geometry, and machining capabilities:
1. Material Type:
Material properties such as hardness, thermal conductivity, and chip formation affect SFM in machining. For example, relatively hard materials like titanium require lower SFM compared to softer materials like plastic or aluminum due to higher cutting resistance.
Materials with better thermal conductivity, such as copper, require lower SFM compared to materials with lower thermal conductivity, such as stainless steel, because of better heat dissipation.
Materials like free-machining steel have good chip formation characteristics, so they tend to perform well at relatively higher SFM.
2. Tool Characteristics:
Tool characteristics such as geometry, rake angle, and even material properties all affect SFM. These will be discussed in detail.
3. Machining Capabilities:
The performance of the machine directly affects the achievable SFM. High RPM machines allow small tools to run at higher speeds, while limited RPM will restrict the speed of large tools. A sturdy, rigid machine can handle higher SFM without vibration, but a less rigid machine requires lower speeds to achieve accuracy. An efficient cooling system can reduce heat and enable faster cutting, while poor cooling will reduce speed. Advanced CNC controls can optimize SFM in real-time for better performance and higher Material Removal Rate (MRR).
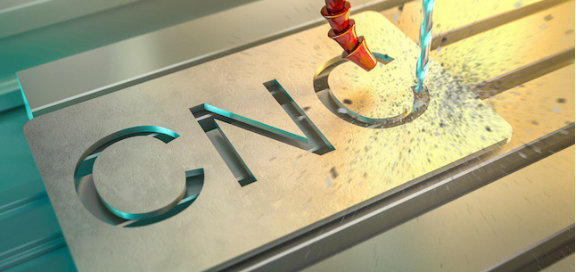
The Role of CNC Tools in SFM Calculation
Selecting the right CNC cutting tool is crucial for improving and optimizing the accuracy and cost-effectiveness of chip and material removal. Here are some parameters to consider:
1. Cutting Tool Material
- High-Speed Steel (HSS): Tools made of this material usually require lower SFM to prevent rapid wear. But it can achieve a good balance between cost and efficiency.
- Carbide Tools: These tools can withstand high temperatures and are wear-resistant. Therefore, higher SFM can be used.
- Ceramics and Cermets: These tools have higher SFM than HSS and carbide tools because they are more heat-resistant and wear-resistant. They are suitable for high-speed machining applications.
2. Tool Coatings:
Hard coatings such as TiN or TiAlN greatly enhance surface properties like friction coefficient and wear resistance, allowing for higher SFM in CNC machining applications.
3. Tool Geometry:
Larger diameter tools allow for lower SFM compared to smaller diameter tools. But in this case, the chip load in CNC machining may be larger.
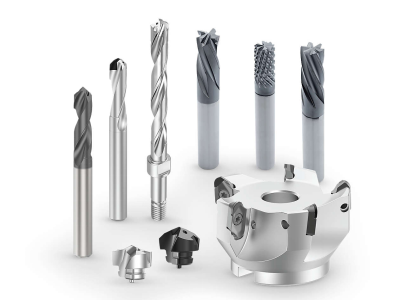
Common Mistakes and How to Avoid Incorrect SFM Settings
Optimal SFM settings are required to maintain good accuracy, good surface finish, good MRR, and long tool life. Here are the common consequences of incorrect settings:
If SFM is Too High:
- Excessive heat generated due to high friction
- Short tool life because the tool tip radius becomes dull quickly
- Material deformation due to overheating
- Dimensional errors due to thermal expansion
- Deterioration of surface finish
If SFM is Too Low:
- Low Material Removal Rate (MRR)
- Excessive tool pressure: leading to shortened tool life
- Tool chatter
How to Adjust SFM for Different Materials?
When adjusting Surface Feet per Minute (SFM) for different materials, factors such as tool type, material hardness, and cutting conditions must be considered. Here are general methods for adjusting SFM for various materials and processes:
SFM for Turning 303 Stainless Steel
For turning 303 stainless steel, several factors such as tool material and cutting type (continuous or interrupted cutting) affect SFM. Generally, carbide tools can achieve higher SFM, but if using HSS tools or performing interrupted cutting, SFM should be reduced. It is also recommended to use coolant to control heat accumulation.
SFM for Drilling 304 Stainless Steel
Drilling 304 stainless steel requires careful adjustment based on tool material and size. For larger drills or when using HSS tools, it is advisable to reduce SFM. Carbide tools and coatings can achieve higher speeds, and using peck drilling can help control heat during the process.
SFM for Milling 4140 Steel
Milling 4140 steel can benefit from higher SFM when using carbide tools for light cuts. For deeper cuts or less rigid setups, reducing SFM will help avoid tool wear and improve machining stability. Using coolant or air cooling also helps control temperature and extend tool life.
SFM for Turning 4140 Steel
Turning 4140 steel requires adjusting SFM based on the material condition. For annealed 4140, higher SFM is suitable, but for hardened material or low-rigidity setups, SFM should be reduced. Coolant is essential to prevent overheating and improve cutting efficiency.
SFM for Cutting 6061 Aluminum
6061 aluminum is relatively soft, so higher SFM is suitable, especially when using polished carbide tools. However, for larger tool diameters or to avoid tool chatter, SFM may need to be reduced. It is recommended to use coolant (either mist or flood) to reduce heat and improve surface finish.
Optimal SFM Chart for Common Machining Materials and Processes
Material and Process | Optimal SFM Range (Feet per Minute) | Adjustment Guidelines |
---|---|---|
Turning 303 Stainless Steel | 300 – 600 | Higher SFM with carbide tools; reduce SFM for HSS or interrupted cutting. Coolant is recommended. |
Drilling 304 Stainless Steel | 50 – 100 | Increase with carbide tools and coatings; reduce with larger drills or HSS. Use peck drilling for heat control. |
Milling 4140 Steel | 250 – 400 | Increase for light cuts and carbide tools; reduce for deeper cuts or less rigid setups. Use coolant or air cooling. |
Turning 4140 Steel | 300 – 500 | Higher SFM for annealed material; lower SFM for hardened 4140 or low-rigidity machines. Coolant is essential. |
Cutting 6061 Aluminum | 600 – 1,200 | Increase with polished carbide tools; reduce with larger diameter tools or if chatter occurs. Use mist or flood coolant. |
Accurate SFM Calculation Tools
Here is a list of commonly used tools for readers:
- FSWizard
- Machinist Calculator Pro (see Youtube link)
- HSMA Advisor
- G-Wizard
- G-Wizard
Frequently Asked Questions (FAQs)
How is Surface Speed Related to SFM?
SFM and surface speed are proportional. The higher the surface speed, the greater the SFM, so within the optimal range of SFM, the Material Removal Rate (MRR) is higher.
What Happens if SFM is Too High or Too Low?
Any deviation from the optimal range of SFM will lead to insufficient accuracy, surface defects, dimensional inaccuracies, increased costs, frequent tool changes, and material deformation.
How to Choose the Right SFM for My CNC Machine?
Consider parameters such as workpiece material, tool material, tool geometry, and workpiece size. The table above gives examples of SFM for common materials. To convert RPM to SFM, use the formula given above.
Does SFM Change During the Same Machining Process?
Yes, SFM also depends on the diameter (D), and if it changes, SFM will also change.
For more information, please contact us at Debaolong Seiko. You are also welcome to upload your design to Debaolong Seiko for a quote.