At this year’s TCT Shenzhen 3D Printing Exhibition, held from September 10 to 12, some exhibitors will showcase additive manufacturing application cases related to low-altitude aircraft – ranging from lightweight design of key structural components to localized printing for maintenance, repair, and operations (MRO). These solutions are attempting to break through the “forming ceiling” of traditional 3D printing, which is caused by equipment volume limitations.
Although robotic arm-based printing has expanded to provide a larger build volume through increased spatial freedom, the dual constraints of fixed platforms and operational radius have always left the manufacturing of large components facing a “heart willing but strength insufficient” dilemma.
Traditional 3D printing is limited by the structural design of printing equipment, often having a “ceiling” in terms of maximum forming volume. While robotic arm-based printing has expanded spatial freedom and movement range to a certain extent, offering a larger build volume, overall, such technologies are still restricted by fixed platforms and operational radius.
Aerial Additive Manufacturing (Aerial AM)
In the field of additive manufacturing, to break through this limitation, a joint research team consisting of University College London (UCL), École Polytechnique Fédérale de Lausanne (EPFL), Swiss Federal Laboratories for Materials Science and Technology (EMPA), and Imperial College London released a cutting-edge study in May this year. It systematically explored the feasibility of drone 3D printing for the first time and proposed an emerging concept: Aerial Additive Manufacturing (Aerial AM for short).
Compared with traditional printing equipment, drones have inherent spatial mobility, enabling long-distance printing in both horizontal and vertical directions, thus breaking through the physical volume limitations of fixed equipment. Based on this advantage, Aerial AM is regarded as a potential technical path to cope with large-scale construction, repair in remote environments, and even future aerial manufacturing tasks. However, the research also points out that Aerial AM is still in the early exploration stage, with three key technical bottlenecks to be broken through:
- Material durability: It is necessary to develop printing materials that are suitable for aerial printing conditions and have high stability;
- Outdoor environment positioning system: To achieve high-precision autonomous positioning of drones in complex environments;
- Multi-machine collaborative control: To build a stable and intelligent task allocation and collaboration mechanism, and improve the efficiency of group operations.
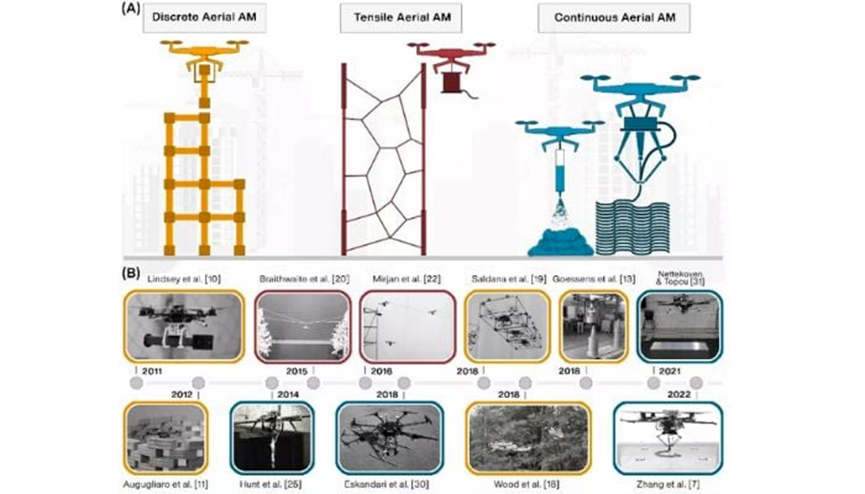
The team proposed three initial implementation methods of aerial additive manufacturing in the research
The team proposed three initial implementation methods of aerial additive manufacturing in the research: first, using drones to transport and accurately position individual prefabricated components; second, using flexible media such as ropes to weave or set up structural units; third, using FDM (Fused Deposition Modeling) for continuous extrusion printing. The project aims to address the pressure on housing and infrastructure brought by urbanization and explore greener and more flexible construction methods. The research team believes that aerial additive manufacturing will show great potential in scenarios such as “unmanned construction” and “low-carbon construction”.
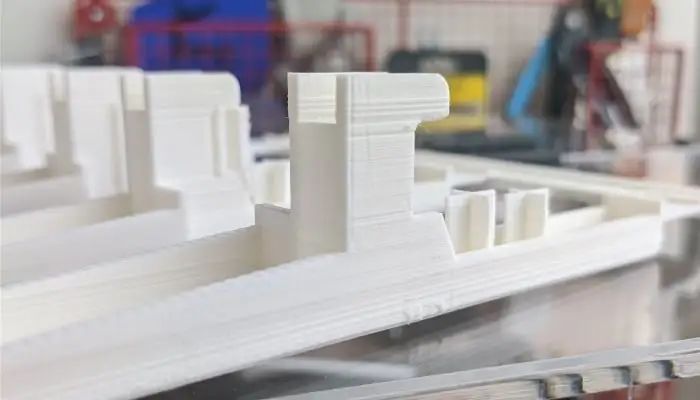
Some printed layer lines are clearly visible
To promote technical verification, the team established a “DroneHub” test center, which can simulate various weather and terrain environments. Preliminary tests show that drones can already achieve rapid structural repair. The team is also developing modular assembly solutions to lay the foundation for the practical application of Aerial AM.
As technologies such as eVTOL (Electric Vertical Take-Off and Landing), electric vertical take-off and landing aircraft, and drones are accelerating towards commercialization, the “low-altitude economy” is rapidly emerging as an important outlet in the new round of scientific and technological revolution and industrial transformation. In this trend, additive manufacturing, with its advantages of lightweight design, rapid iteration, and high customization, is gradually integrating into the core manufacturing and application links of low-altitude aircraft, becoming an important engine for promoting industrial upgrading.
At this year’s TCT Shenzhen Exhibition from September 10 to 12, some exhibitors will also bring additive manufacturing application cases related to low-altitude aircraft, including lightweight design of key structural components, rapid manufacturing of functional parts, and localized printing solutions in the maintenance, repair, and operations (MRO) link.
AVIC Metal Powder: Four-Rotor UAV
AVIC Metal Powder, relying on the advantages of one-stop comprehensive services for metal 3D printing equipment, materials, and processes, is actively exploring metal 3D printing solutions for the low-altitude industry.
AVIC Metal Powder uses self-developed MT-Ti6Al4V titanium alloy powder and MT650 equipment, and through unique bionic design inspiration, drawing on the structure of bird bones and insect wings, optimizes the topology of parts, successfully overcoming the limitations of traditional manufacturing technology in the manufacturing of complex structures. This highly free integrated forming technology effectively solves the problems of traditional drones, such as heavy weight, short battery life, and poor design flexibility. Practice has proved that the drones manufactured using AVIC Metal Powder’s 3D printing technology have a 40% weight reduction, significantly improved flight flexibility, significantly reduced energy consumption, and a 26% increase in battery life, enabling the drones to carry more diverse equipment and perform more complex tasks, releasing value for drones in more application scenarios such as aerial photography and mapping, logistics and distribution, and agricultural and forestry plant protection.
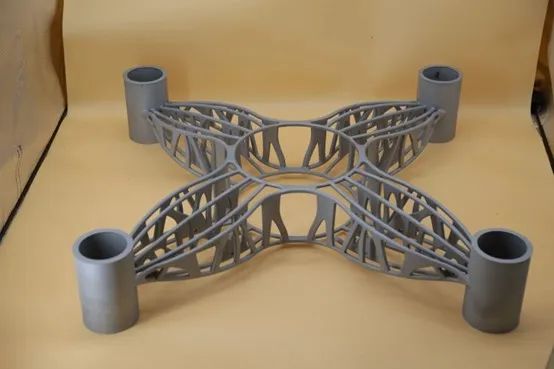
The company was included in the first batch of the 2025 Low-Altitude Economy Industry – 3D Printing Excellent Suppliers list in March 2025.
HP: Smart Drone ATHERA Components
VECROS, India’s first space AI drone startup, is accelerating the product development and engineering implementation of its smart drone ATHERA with the help of HP Multi Jet Fusion 3D printing technology. As an AI-driven drone with automatic navigation and obstacle avoidance capabilities, ATHERA puts forward higher requirements for structural complexity and performance for inspection and monitoring scenarios in multiple industries such as mining, construction, telecommunications, oil, and gas.
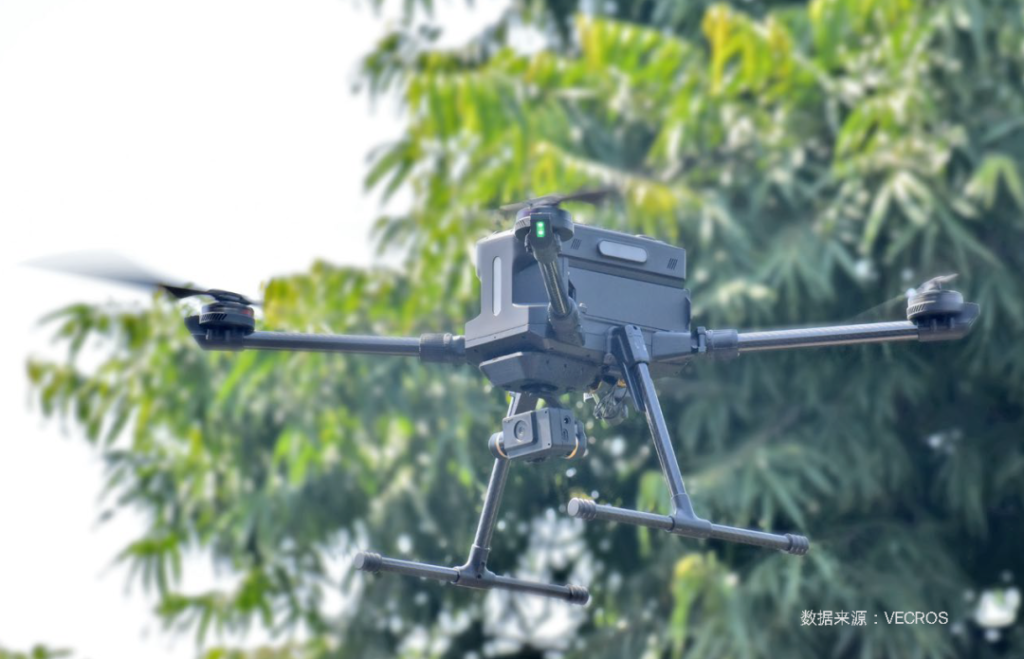
The VECROS team tried various additive manufacturing processes in the prototype design stage and finally chose HP MJF technology to meet the comprehensive requirements for surface finish, strength, structural integration, and design flexibility. By using the HP Jet Fusion 5210 printing platform and PA 12 material, VECROS not only significantly improved component performance but also accelerated the iteration speed and reduced the cost of mold manufacturing and small-batch production. VECROS stated that with the help of HP 3D printing technology, they have achieved the rapid transformation of products from conception to actual testing, and the current version of ATHERA is close to the initial ideal state in terms of design and function integration, and will continue to explore deeper optimization possibilities in subsequent versions.
Formlabs: Lightweight Drone Frame
ION Mobility has actively introduced additive manufacturing technology in drone research and development to meet the actual needs of complex structures, small-batch customization, and rapid iteration. In the past, relying on traditional machining, not only the manufacturing cycle was long, but once the design was changed, the iteration cost soared. To solve these bottlenecks, the company introduced Formlabs’ Fuse 1+ 30W Selective Laser Sintering (SLS) 3D printer to realize the internal rapid manufacturing of key components. With this system, the R&D team can complete high-density printing tasks within hours, independently produce end parts with complex geometric structures, and take into account both strength and surface quality.
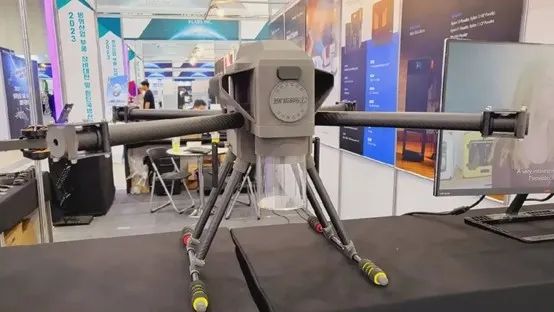
By using Formlabs’ Nylon 12 GF (glass fiber reinforced nylon) powder, ION Mobility has successfully created lightweight fuselages, high-temperature resistant motor brackets, and mission equipment enclosures with 达标 precision. Key components remain stable in extreme environments. This complete set of additive manufacturing solutions not only meets the strict requirements of drones for structural strength, weight control, and thermal stability but also significantly improves product development efficiency – the company’s overall R&D cost has been reduced by about 60%, and the design iteration speed has increased by 70%. The application of SLS technology has significantly accelerated the entire process from prototype design to small-batch production, providing strong support for product performance optimization and market response.
Chuangrui Laser: Lattice Sandwich Wing
It has broken through key technologies such as plasma beam additive manufacturing online monitoring, digital twin intelligent control technology, and in-situ preparation composition precision control, realizing the efficient and low-cost manufacturing of high-quality 600mm-level titanium alloy/refractory high-entropy alloy gradient grid rudders and 3m-level titanium alloy lattice sandwich wings. The grid rudder samples have passed the ground static test verification, and the UAV lattice wing samples have passed the test flight verification, promoting the application of plasma beam additive manufacturing technology in the aerospace field.
A+PLUS: Hydrogen Energy UAV
A leading hydrogen fuel cell technology enterprise in China, based on A+PLUS’s Blast X agile manufacturing platform, has begun to deploy hydrogen fuel cell systems in various special UAV models in batches.
Due to the complex application scenarios of special UAVs, high requirements are put forward for structural functional components, which must have excellent mechanical strength and environmental adaptability, while also challenging customization and delivery timeliness. The Blast X platform, relying on its high-precision linear motor system and industrial-grade dual-nozzle architecture, combined with BlastMate PAHT-CF / PET-CF and other engineering-grade carbon fiber composite materials, has realized the full-process one-stop in-house manufacturing capability of structural components from modeling to batch delivery.
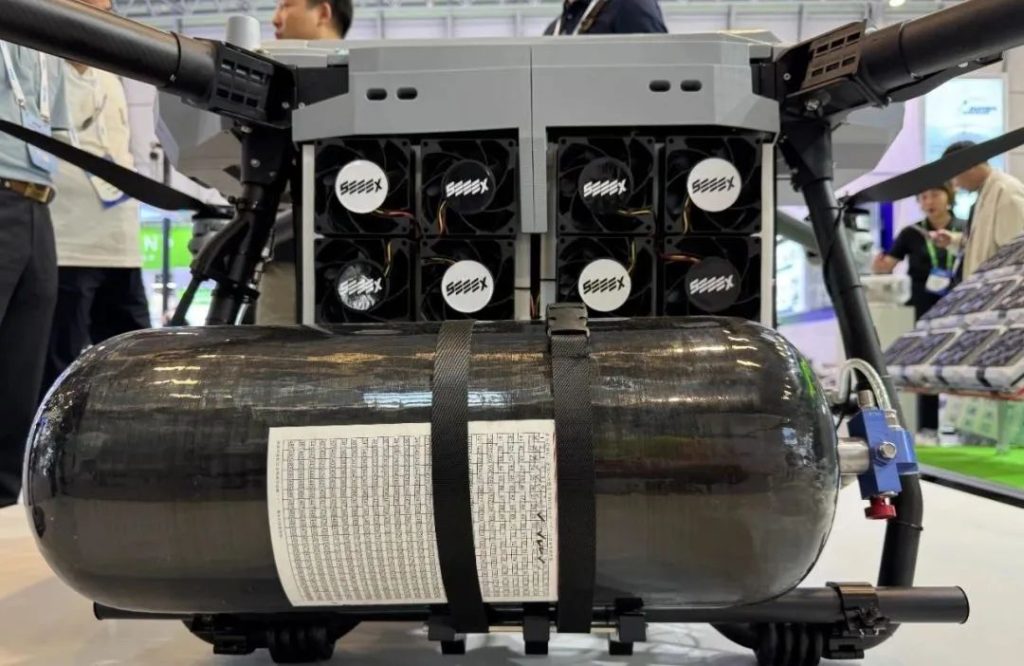
It not only demonstrates the manufacturing potential of the Blast series in the integration of new energy and unmanned systems but also re-verifies its leading advantages in high-performance composite material printing, flexible customization, and rapid response, providing strong manufacturing support for the large-scale implementation of hydrogen energy UAVs.
There will also be the TCT Shenzhen Summit – Low-Altitude Economy and Additive Integration Industry Forum on site, which will focus on the industrial integration of “low-altitude economy” and “additive manufacturing”. Around topics such as cutting-edge technologies, application scenarios, industrial chain collaboration, and commercialization paths, representatives from main engine factories, supply chain enterprises, scientific research institutions, and policy support units will be invited to discuss the future, promote technology implementation and industrial development, and bring an exchange feast with both forward-looking vision and technical insights.
As 3D printing technology continues to break through, additive manufacturing is profoundly changing the future of manufacturing. Whether in aerospace, automotive, medical, architecture, or consumer electronics, innovative applications are emerging one after another, bringing unprecedented opportunities and challenges.
For more information, please contact us at Debaolong Seiko. You are also welcome to upload your designs to Debaolong Seiko for a quotation.