CNC machining is a versatile technology capable of producing various espresso machine components, such as filter baskets, nozzles, handles, and other structural parts, with high precision and repeatability. This article details the list of CNC-machined espresso machine parts, processes, and surface treatments.
Why Choose CNC Machining for Espresso Machine Parts?
CNC machining is selected for manufacturing coffee equipment parts due to its high precision, superior quality, speed, excellent repeatability, ability to produce complex shapes and geometries, and low production costs.
Precision and Accuracy of CNC Machining
CNC machining offers high precision and accuracy, which is required for complex espresso machine components. It achieves extremely tight tolerances of ±0.0025 mm (a quarter of a human hair), compared to standard tolerances of ±0.1 mm.
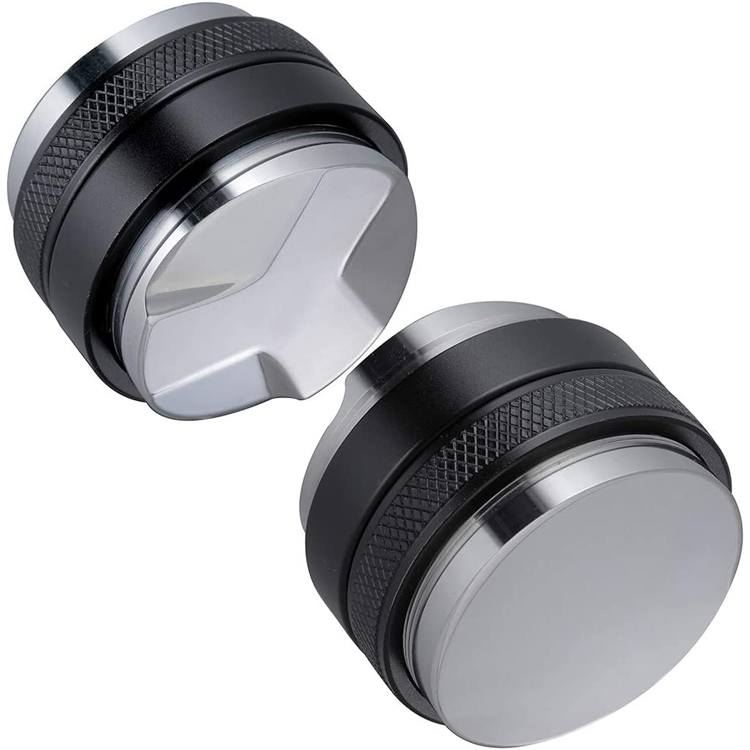
Cost-Effectiveness in Mass Production
Thanks to economies of scale, CNC machines are highly cost-effective for mass production. They also reduce labor costs through automation and efficiently utilize materials, lowering the cost per part.
Complex Geometries and Customization
CNC machines excel at manufacturing complex geometries and custom parts through multi-axis capabilities, advanced software integration, and precision tools. They can produce intricate shapes and features that are difficult to achieve with traditional machining.
List of CNC-Machined Espresso Machine Parts: Precision Components
CNC machining can create precise, complex parts with high quality and functionality. The list of espresso machine parts is explained as follows:
Group Head
The brew head body and gasket are components for extracting coffee. They secure the portafilter and regulate water flow through pressure.
Portafilter
This component includes a handle, basket, and spout, used to hold coffee grounds before brewing espresso. It is also known as the filter handle.
Steam Wand
The steam wand uses steam to heat and froth milk inside the wand, creating foamed milk for cappuccinos and lattes.
Boiler
The boiler is responsible for heating and maintaining pressurized water, which is essential for espresso extraction.
Drip Tray
The drip tray and dreg box collect effluent produced during brewing. This helps keep the espresso machine clean.
Dispensing Head
This distribution nozzle is a key component for texturing milk and creating microfoam. The distribution switch is located on top of the component it operates.
Custom Parts
CNC machining allows customization of parts such as adjustment rings or knobs around the bean hopper, or pressure gauges for boiler pressure and pump operation.
CNC Machining Process for Espresso Machine Parts: Step-by-Step Explanation
Espresso machine part machining involves several steps, discussed separately below:
Step 1: Material Selection
Material selection for CNC-machined espresso parts is based on factors such as durability, functionality, and machinability. Common materials include stainless steel, brass, and aluminum.
Step 2: Design and CAD Modeling
Espresso machine designs are created using 3D modeling in Computer-Aided Design (CAD), which defines all dimensions, geometries, and features.
Step 3: CNC Programming
The CAD model is converted into a series of commands (G-code) that the CNC machine can understand. Machine parameters are then set accordingly.
Step 4: Machining Process
Guided by G-code, the machining process begins, performing operations such as milling (using rotating tools to remove material), drilling (creating holes), and turning (rotating cylindrical workpieces to cut shapes).
Step 5: Final Inspection and Quality Control
After machining, parts require additional finishing to achieve the desired surface effect, such as deburring, polishing, and coating. They are then inspected to ensure they meet the required tolerances and specifications.
Surface Treatment Technologies for Espresso Machine Parts
Several surface treatment technologies are available for espresso machine parts, including:
Polishing
It creates a smooth, reflective surface, enhancing the appearance of metal components in espresso machines. For complex parts, this is time-consuming and labor-intensive.
Anodizing
This is an electrochemical process that forms a protective oxide layer on the surface of aluminum components in espresso machines. It improves corrosion resistance and can be done in various colors.
Electroplating
It uses an electric current to form a thin metal layer on the base material. It is used to decorate or protect machined espresso machine components.
Sandblasting
This surface treatment uses a stream of abrasive glass beads to clean and roughen the surface of CNC-machined espresso machine parts, preparing them for painting and coating.
Shot Peening
This involves bombarding the metal surface with tiny round particles (shots) to create a cold-worked layer with compressive residual stress on machine components of espresso machines.
Sandblasting (Repeat Note: As mentioned, this uses sand as abrasive particles to roughen the surface of espresso machine parts.)
Impact of Surface Finish on Espresso Machine Part Performance
Surface finish is crucial for the aesthetics and performance of espresso machine components. Its importance is explained as follows:
Improved Durability and Corrosion Resistance
A smooth surface finish reduces friction between parts, increasing durability and minimizing wear. It also protects part surfaces exposed to water and steam from corrosion.
Aesthetic Enhancement
It contributes to the overall functionality and appearance of machine parts, thereby influencing the user experience. Finished surfaces also facilitate smooth assembly and compatibility between components.
Enhanced Functional Performance
Better overall functional performance is achieved due to reduced friction, smooth surfaces, and less heat generation, thus improving service life, efficiency, and performance.
Conclusion
CNC machining can produce various espresso machine components, such as steam wands, group heads, dispensing heads, nozzles, and portafilters, with strong functionality, excellent performance, and high precision. Additional surface treatment processes like electroplating, anodizing, shot peening, and sandblasting can improve the corrosion resistance, wear resistance, aesthetics, and functionality of espresso machine components.
For more information, please contact Debaolong Seiko. You are also welcome to upload your designs to Debaolong Seiko for a quotation.