Powder coating is a surface treatment process that enhances the properties of metal surfaces by applying a protective layer. However, powder coating materials may need to be removed to repair and restore the original surface. This article will explain how to remove powder coating from metal and plastic, as well as the advantages and disadvantages of each method.
What Is Powder Coating?
It is a dry surface treatment process that uses static electricity to spray powder onto a surface. The powder coating is cured to form a durable protective layer. This is a high-quality surface treatment that improves the material’s corrosion resistance and anti-corrosion properties.
Metal Powder Coating
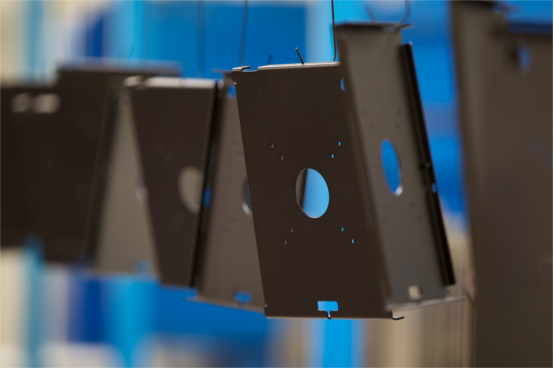
Metals such as aluminum, titanium, copper, brass, bronze, steel, and stainless steel are widely powder-coated to enhance their rust resistance, scratch resistance, and impact resistance. The coating forms a strong, durable barrier to protect the metal. It also provides a decorative finish for the final product, with customizable colors and styles.
Plastic Powder Coating
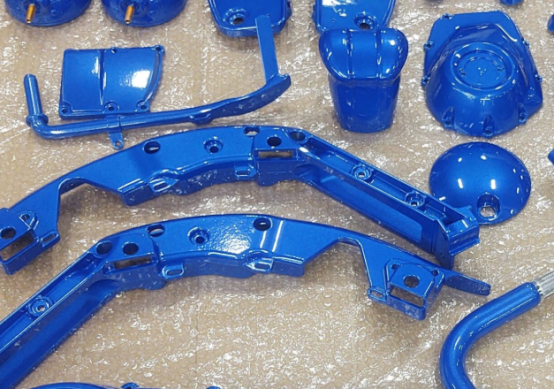
Plastics such as polysulfone, fiberglass and carbon fiber, ABS, PVC, and polycarbonate are powder-coated to improve their durability, impact resistance, and scratch resistance, and to prevent UV degradation and damage from extreme weather and temperature conditions.
Why and When Is Powder Coating Removal Needed?
Powder coating needs to be removed for several reasons, explained as follows:
Common Reasons for Powder Coating Removal
One of the common reasons for removing powder coating is to repair and restore the original surface, as well as to address adhesion and curing issues.
Repair and Repainting
Re-painting the original surface, such as applying a new coating or welding, requires removing the powder coating. If you want to customize the product by repainting it with a different color, style, or texture, the existing coating must be removed.
Repairing Damaged Surfaces
Damage such as cracks or chips requires removing the powder coating to repair the original surface. In some cases, if the coating has poor adhesion, leading to peeling or bubbling, the coating also needs to be removed to repair the surface.
Consequences of Improper Powder Coating Removal
If powder coating is not removed properly, it may damage the metal substrate, cause subsequent coatings to fail to adhere, result in peeling or chipping, and reduce the quality of the new coating.
New Coating Adhesion Issues
Poor surface preparation or application techniques can cause new coatings to peel, bubble, or chip, leading to adhesion problems.
Surface Damage and Reduced Durability
Using improper methods (such as abrasive tools or harsh chemicals) to remove powder coating can scratch and weaken the underlying substrate.
The Easiest Way to Remove Powder Coating: Chemical Stripping
Chemical stripping is considered a simple and commonly used method for removing powder coating. Details are as follows:
What Is Chemical Stripping? How Does It Work?
It involves using chemical solutions to dissolve, soften, or swell the powder coating, allowing it to be peeled or washed off the metal surface.
Types of Chemical Strippers
Solvent-based strippers contain methylene chloride, which can dissolve powder coatings—examples include Benco-B17, acetylene, or ethanol, used as industrial or automotive paint strippers. Alkaline strippers use alkaline substances such as sodium hydroxide to break down organic matter. Other chemicals, such as biochemical and acidic strippers, are also used.
How to Safely Use Chemical Strippers
Personal protective equipment (PPE) must be worn, ventilation must be ensured, and the manufacturer’s instructions for use and handling must be followed. Apply the stripper using brushing or dripping, leave it for a period of time, then scrape off the powder coating.
Pros and Cons of Chemical Stripping
Each method has its advantages and limitations. The pros and cons of chemical stripping are as follows:
Advantages
- It effectively dissolves and removes powder coating with minimal or no damage to the original substrate.
- This method mostly provides consistent powder coating removal results.
- Overall, it is a cost-effective method requiring less capital and manual labor.
Risks and Hazards
- Solvent-based strippers produce toxic fumes, posing potential health risks.
- The use of solvents causes environmental pollution.
- This method takes more time than other methods such as heat removal or blasting.
Best Chemicals for Removing Powder Coating
Benco B-17 is highly recommended as it can remove coatings in 20 minutes. Klean Strip or regular acetone can also be used for DIY powder coating removal.
Acetone vs. Other Solvents
Acetone, like methylene chloride, is one of the most effective chemicals, though acetone is relatively less potent. However, for safety reasons, methylene chloride has been replaced by benzyl alcohol.
Choosing the Right Chemicals for Different Materials
For metals, Benco B17 and trisodium phosphate can be used. For composites and polymers, specialized strippers or other methods such as heating and sandblasting are used.
Heat Stripping: Using Heat to Remove Powder Coating
Heat stripping is another common method for removing powder coating. Details of the process are as follows:
How Does Heat Stripping Work? The Burning Process
This process uses high temperatures to decompose the coating, converting it into ash that can be easily removed. This process is also called burning off.
Equipment Required for Heat Stripping
It is performed in industrial ovens with temperatures up to 600-1200°F, or on fluidized bed systems for heating large components, while heat guns are used for smaller parts.
Safety Precautions When Using Heat Sources
Safety kits such as personal protective equipment (PPE) and proper ventilation systems are required to avoid potential hazards such as toxic fumes and high-temperature surfaces.
Pros and Cons of Heat Stripping
The pros and cons of this method are as follows:
Advantages
- It is a relatively fast process for large batches.
- Ash can be removed by rinsing with water, eliminating the need for chemical treatment.
Disadvantages
- It requires specialized equipment, such as expensive high-temperature furnaces.
- It is not suitable for all types of materials, such as soft metals and heat-sensitive materials.
What Temperature Is Needed to Remove Powder Coating?
The minimum temperature required to burn off powder coating is 650°F, with a maximum of 1200°F. However, for heat-sensitive materials such as polymers or aluminum alloys, the temperature must not exceed 200°F.
Sandblasting to Remove Powder Coating
This is also an effective method for removing powder coating.
How Does Sandblasting Work for Powder Coatings?
Pressurized air or water is used to propel abrasive particles toward the surface. This breaks down and removes the coating from the metal.
Wet Blasting vs. Dry Blasting
Wet blasting is more popular than dry blasting. It cools the surface to prevent warping, produces a smoother surface, and offers better process control. Dry blasting is also effective for powder coating removal but may cause issues with thin metals and heat-sensitive materials due to high temperatures.
Media Selection for Effective Blasting
Different abrasive media are used, such as glass beads, aluminum oxide, or garnet. These media have good removal power and can create a textured surface, which helps with the adhesion of new coatings.
Pros and Cons of Sandblasting
The pros and cons of this method are as follows:
Advantages
- It is cheaper than other methods and effective for large batches.
- It creates a surface profile, providing better adhesion for new coatings.
- It is a versatile process suitable for different applications, completing the job in one step.
Risks
- It requires manual control and is a time-consuming and labor-intensive process.
- It may corrode soft metals if operated improperly.
Which Surfaces Can Be Safely Sandblasted?
It is considered safe for metals such as steel, aluminum, and other alloys, but is sometimes unsuitable for plastics and composites due to their softness.
Laser Removal of Powder Coating: A High-Tech Solution
This is a precise and environmentally friendly coating removal process.
How Does Laser Powder Coating Removal Work?
A laser beam is used to vaporize the powder coating, leaving the metal surface clean and intact. It is particularly suitable for localized areas and offers many advantages over traditional methods such as chemical stripping and sandblasting.
Types of Lasers Used for Powder Coating Removal
Laser types used include single-mode and multi-mode lasers. Single-mode lasers have better beam quality, can etch the surface, and provide stronger adhesion after cleaning. Multi-mode lasers clean faster.
Pros and Cons of Laser Removal
The pros and cons of laser removal are as follows:
Advantages
- It is a precise and controllable process that does not damage the substrate.
- It is an environmentally friendly method requiring no additional cleaning.
- It is an easily automatable process and highly effective for large-scale production.
Disadvantages
- It is not suitable for large areas, only for localized regions.
- Heat treatment during removal may damage the coating or material.
- Overall, it is an expensive process compared to other methods.
When Should Laser Powder Coating Removal Be Chosen?
It is the preferred option when precise and efficient removal of localized areas or fragile materials is needed. It causes minimal damage to the underlying material.
How to Remove Powder Coating from Different Materials
Each material behaves differently during powder coating removal due to differences in heat sensitivity, strength, and durability.
How to Remove Powder Coating from Aluminum?
Considering aluminum’s melting temperature and strength, thermal, chemical, and abrasive removal methods can be used.
Step-by-Step Guide:
- Prepare the surface to remove any dirt.
- Apply the chemical stripper to the area using brushing, spraying, or dipping.
- Soak for up to 10-20 minutes.
- Scrape off the softened powder with a scraper, brush, or wire.
- Rinse with water and clean the final surface or remove grease.
How to Remove Powder Coating from Steel?
Removing powder coating from steel can be challenging due to its strong adhesion to the substrate. However, all methods can remove the coating.
Step-by-Step Guide:
Chemical stripping involves:
- Cleaning the surface.
- Using Benco B-17 or Prematex/Miles paint stripper.
- Soaking for 15-20 minutes.
- Removing the softened powder with a brush or scraper.
How to Remove Powder Coating from Titanium?
Like steel, titanium can be treated with chemical stripping, sandblasting, or heat removal.
Step-by-Step Guide:
- Chemical solutions dissolve the powder coating, which can be cleaned with a scraper or brush.
- Heat the titanium with a heat gun to burn off the coating, then the ash can be easily removed.
- Abrasive media such as sand or glass beads strip the coating from the surface.
Powder Coating Removal from Plastic vs. Metal
For metals, chemical stripping, sandblasting, or heat stripping can be used; for plastics, plastic media blasting is usually used to avoid damaging the material.
Conclusion
Powder coating is a surface treatment process that protects surfaces from corrosion and damage. But sometimes it needs to be removed for repair or restoration of the original surface. Powder coating can be applied to both metal and plastic, but removing it from plastic is more critical than from metal, as plastic substrates use specially formulated powders to improve durability. For metals, chemical strippers—mostly solvent-based and alkaline—are commonly used. After removal, the surface needs to be cleaned and pre-treated to effectively bond with the new coating, ensuring good adhesion.
However, choosing the right surface treatment method can save a lot of effort. If you are still troubled by your processing project—such as choosing powder coating for CNC precision custom parts—you can contact a professional team: Debaolong Seiko Online Machining to assist you in selecting the most suitable one-stop solution! With years of experience in this field, we cover everything from design to CNC machining to surface treatment.