Have you ever wondered how medical tools, aerospace components, or automotive parts achieve such high-precision surfaces? The answer is honing. As a critical process in metalworking, honing plays a pivotal role in industries like aerospace, automotive, and beyond, enabling strict tolerances and smooth surfaces. This article delves into honing, its processes, and tools.
Definition of Honing
Honing is used in manufacturing to enhance the geometric accuracy of cylindrical holes and internal surfaces. It helps achieve the required tolerances and improve surface finish.
What is Honing?
It is a process of fine-tuning surfaces. A rotating abrasive stone or honing stone is used to remove an extremely small amount of material, typically 0.005 millimeters.
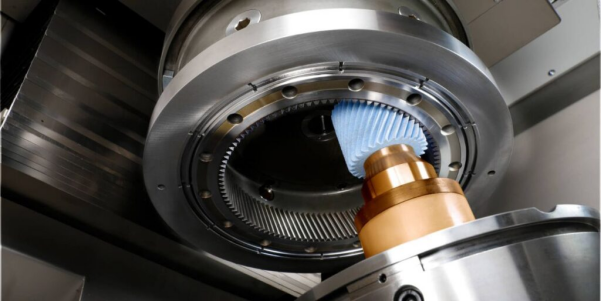
How Does Honing Work?
In a honing operation, the abrasive stone or honing head rotates over the workpiece surface with controlled movement. By applying controlled pressure, the honing head expands against the workpiece, removing material.
Benefits of Honing for Precision Parts
Honing offers numerous advantages for machining precision components. Below are some key benefits and their applications:
- Improved Accuracy
It allows precise control of hole diameter, enabling tolerances as low as ±0.002 millimeters and a surface finish of Ra 0.2 microns.
- Applications in Honing: Commonly used for automotive parts like cylinders, fuel rails, engine blocks, and other components requiring strict tolerances and smooth surfaces.
- Correction of Roundness and Straightness
Honing can help correct geometric errors in holes, such as roundness and straightness. This process is vital for components like aerospace actuator holes.
- Applications in Honing: Used for aerospace parts, including actuator holes, hydraulic cylinders, and other critical components where precision and reliability are essential.
- Extended Life of Tools and Seals
Honing achieves a smooth and consistent surface finish, optimizing clearances between components. It also reduces friction and wear, ultimately extending the lifespan of tools and seals.
- Applications in Honing: Hydraulic and pneumatic cylinders, pistons, and other components in hydraulic systems require honing to ensure leak-free seals and prolong part life.
- Efficient Production
Honing is a relatively fast process, and its automation further enhances production efficiency while reducing labor costs.
- Applications in Honing: High productivity makes honing suitable for mass manufacturing of applications requiring precise dimensions, smooth surfaces, and reliable seals.
Common Types of Honing Operations
Honing operations can be categorized based on their automation level and production capacity, such as manual or automated, low-cost or small-batch finishing to high-volume processing.
- Manual Honing Operations
Manual honing is typically lower in cost and suitable for single-piece or small-batch production. It is often used for finishing pre-machined surfaces or precision machining of individual parts, requiring the use of handheld honing tools to rub against the workpiece. - Reciprocating Machine Honing
This process is suitable for medium-capacity parts that require precise hole dimensions and surface finish. It uses a machine to move the honing tool back and forth (reciprocating motion) while rotating it, creating a cross-hatch pattern on the workpiece.
- Vertical vs. Horizontal Honing: Vertical machines are ideal for machining long holes, while horizontal machines suit larger or heavier parts.
- Single-Pass Diamond Honing
This process features short cycle times and is suitable for hardened steel. It uses diamond abrasives to remove a small amount of material in one pass. Due to its speed and high material removal rate, precise hole pre-positioning is required. It is recommended for mass production of parts with tight tolerances and high surface finish. - CNC Adaptive Honing
CNC honing is a highly automated process with servo-controlled pressure and online metrology. CNC honing machines automatically adjust honing pressure and dwell time based on feedback from the metrology system. It is strongly recommended for high-precision, high-volume production of complex geometries with strict tolerances.
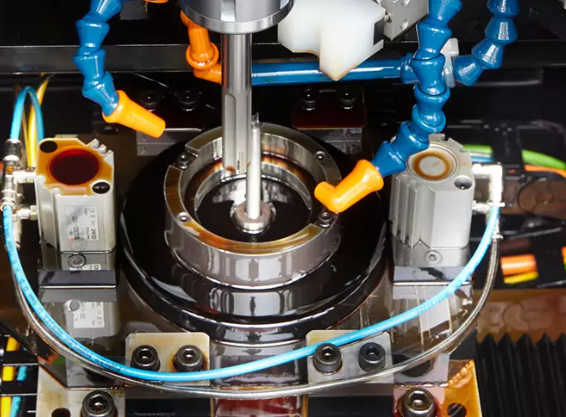
Honing Equipment: Vertical, Horizontal, CNC Systems
Honing machines come in vertical, horizontal, and CNC configurations to achieve high precision and surface finish on internal cylindrical surfaces.
- Vertical Honing Centers: These CNC honing machines are designed for high precision and accuracy, especially suitable for machining long holes or components with strict tolerances. Long tubes and shafts can be easily loaded vertically into automatic honing systems for efficient material handling. Coolant is injected from the top into the hole, flushing chips and debris downward.
- Horizontal Honing Machines: These CNC honing machines offer shorter cycle times for machining shorter parts, ideal for batch production. With horizontal placement, workpiece loading and unloading are convenient. Coolant is introduced from one end, circulates through the workpiece, and exits from the other end.
- Multi-Spindle or Rotary Indexing Systems: These CNC honing machines use multiple honing spindles or a rotary indexing table to machine multiple parts simultaneously, leveraging parallel processing to minimize idle time between honing cycles. The rotary indexing table has multiple stations, moving parts from one station to the next for honing stages like roughing, semi-finishing, and finishing.
Guide to Precision Surface Finishing Processes
A typical precision surface finishing process using honing involves multiple steps:
- Secure and mount the workpiece on a CNC honing machine. Select the appropriate honing tool (abrasive stone or wheel) based on the workpiece material and required surface finish.
- Remove a small amount of material to achieve initial surface finish and geometry.
- Regularly measure surface finish and dimensions using a profilometer or other measuring instruments to ensure compliance with specifications.
- Complete the process with finer abrasive tools to achieve the final surface finish and geometric accuracy.
- Thoroughly clean the workpiece to remove abrasive particles and contaminants.
- Conduct a final inspection of the finished surface to verify dimensions, surface finish, and honing quality.
Honing Surface Finish Table (by Material)
Below are the honing surface finishes (Ra) for some common materials:
Material | Surface Finish (Ra) |
---|---|
Cast Iron | 0.2–0.8 μm |
Alloy Steel | 0.1–0.4 μm |
Aluminum Plate | 0.2–0.6 μm |
Ceramic | 0.1–0.4 μm |
Tips to Improve Honing Quality
- For taper and out-of-roundness, adjust honing pressure, feed rate, and honing time.
- For irregular surface finishes, adjust abrasive grit size and honing parameters.
- For chatter marks, reduce pressure, optimize honing motion, and check machine stability.
- When loading stones, use a dressing tool to clean and sharpen them.
- If material removal is insufficient, increase cutting pressure and use coarser abrasives.
Honing vs. Grinding, Lapping, Reaming
These are all machining processes used to improve surface finish and dimensional accuracy, but they have distinct characteristics and applications:
- Honing vs. Sharpening: Sharpening has a higher material removal rate and is faster, while honing is more cost-effective with longer tool life. It also provides a better surface finish and finer edge 打磨 compared to sharpening. CNC honing machines require simpler tools and are easier to learn than sharpening setups.
- Honing vs. Lapping: Honing has a higher material removal rate and speed than lapping. It is more cost-effective for achieving high-precision hole diameters, though honing oil management may increase overall costs. Honing can achieve precision tolerances as low as 0.005 millimeters, while lapping is better for creating extremely flat surfaces.
- Honing vs. Grinding: Grinding has a higher material removal rate than honing, while honing is better for fine finishing. Grinding is generally a cost-effective process, but honing is more cost-effective for achieving strict final tolerances and surface finishes.
- Honing vs. Reaming: Reaming has a higher material removal rate than honing. Honing is better suited for achieving high-precision internal diameters and surface finishes. Reaming is generally more cost-effective than honing and requires simpler, fewer tools. However, honing tools have the inherent ability to self-center in the hole, which is superior to reaming. Reaming is the best choice when the hole is not perfectly aligned with the machine axis.
Conclusion
Honing is a precision machining process that uses abrasive stones to improve the surface finish and geometry of internal cylindrical surfaces by removing minimal material. As a critical link between rough machining and a part’s final performance, honing enhances part accuracy, surface quality, and optimal functionality.
If you need to enhance part performance through precision honing, consider contacting Debaolong Seiko for a quote tailored to your specific needs.