Zinc machining is vital for numerous sectors due to its unique properties, enabling straightforward innovation. Zinc alloys are favored in various applications for their cost-effectiveness, versatility, and high precision. Moreover, the distinct characteristics of zinc metal and its ease of alloying with other metals make it an ideal choice for manufacturing high-quality precision parts. This article further explores different types of zinc alloys and their suitability for CNC machining.
What is Zinc Alloy?
A zinc alloy is a combination of zinc with other metals such as tin, aluminum, copper, or cadmium. These materials offer superior properties compared to pure metals, including high corrosion resistance, ductility, and strength. Common applications of zinc alloys include thermal spraying, die casting, and the manufacture of construction, household, and automotive components.
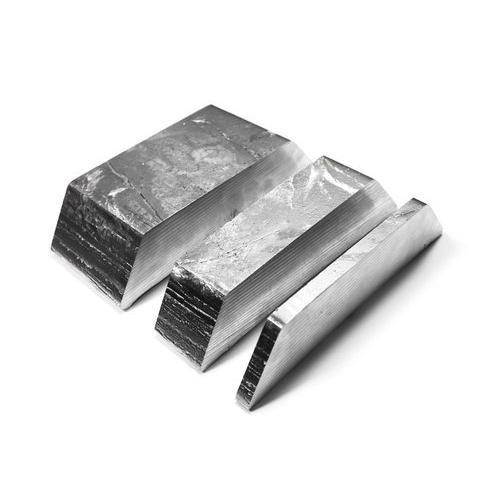
Why is Zinc Suitable for Precision Machining?
Zinc is a preferred material for precision machining due to its excellent machinability, ability to achieve tight tolerances, and cost-effectiveness. With a low melting point and high thermal conductivity, zinc is well-suited for machining applications. Additionally, it provides stable chip formation, further enhancing the precision and efficiency of machining operations.
A Brief History of Zinc Alloys
Zinc alloys have a history spanning thousands of years. They were first used as brass in ancient times, as zinc as a pure metal was not recognized until the late 1400s. Early zinc production and refining originated in China and India, while Europe began in the 18th century.
Year | Country | Description |
---|---|---|
Ancient (<1000 BC) | Palestine | Zinc ores were used to manufacture brass. |
13th century | India | Metal zinc was produced for the first time. |
1400 | India | Zinc was recognized as a pure, distinct metal. |
1500 | China | Large-scale zinc refining production. |
1740s | Europe | Andreas Marggraf of Germany rediscovered pure metallic zinc. |
10 Zinc Alloys Suitable for Machining
Zinc alloys used in machining include Zamak 2, Zamak 3, Zamak 5, Zamak 7, ZA-8, and more. Below are detailed descriptions of ten zinc alloys most commonly used in machining:
- Zamak 3
Zamak 3 is a common zinc-based die-casting alloy, known for its high castability, high strength-to-weight ratio, and corrosion resistance. It is renowned for its die-casting and finishing properties, suitable for various applications.
- Composition:
- Zinc: 96%
- Aluminum: 3.5–4.3%
- Magnesium: 0.02–0.05%
- Copper: 0.025%
- Properties:
- High fluidity, easy for die casting
- Good ductility for bending and forming
- High dimensional accuracy and stability
- Excellent corrosion resistance
- Cost-effective
- Limitations:
- Lower tensile strength than some other alloys
- Prone to creep
- Applications:
- Automotive parts (door handles, decorative elements)
- Electronic housings, connectors, and components
- Hinges, locks, and other hardware
- Furniture, appliances, and home products
- Medical devices and instruments
- Zamak 5
Zamak 5 is primarily composed of zinc and aluminum with other alloying elements, known for its corrosion resistance, strength, and high-pressure casting properties.
- Composition:
- Zinc: 96%
- Aluminum: 3.8–4.2%
- Magnesium: 0.035–0.06%
- Copper: 0.7–1.1%
- Properties:
- High strength and hardness
- Good corrosion resistance
- Excellent die-casting performance
- Cost-effective
- Limitations:
- Lower ductility
- Low thermal strength at high temperatures
- Heavier weight, unsuitable for weight-sensitive applications
- Applications:
- Automotive parts (brackets, gearboxes, motor components)
- Consumer products (decorative elements, furniture locks, handles)
- Industrial equipment and machinery components
- Construction hardware
- Sanitary fittings
- Zamak 7
Zamak 7 is known for its good ductility, excellent castability, and relatively high strength, primarily containing zinc with small amounts of aluminum and other elements.
- Composition:
- Zinc: 96%
- Aluminum: 4%
- Trace amounts of magnesium and copper
- Properties:
- Excellent castability
- High ductility
- Good strength
- Dimensional stability
- Corrosion resistance
- Low melting point
- Limitations:
- Susceptible to hydrogen embrittlement
- Lower strength compared to some alloys
- Unsuitable for high-temperature applications
- May require surface treatment
- Applications:
- Automotive parts (engine mounts, steering components)
- Electrical and electronic components (housings, connectors)
- Industrial parts (pumps, valves)
- Household appliance handles, etc.
- Zamak 2
Primarily used for die casting, Zamak 2 is known for its high strength, hardness, and creep resistance, composed mainly of zinc, copper, and other elements.
- Composition:
- Zinc: 96%
- Aluminum: 3.7–4.3%
- Magnesium: 0.02–0.06%
- Copper: 2.6–3.3%
- Properties:
- High tensile strength and hardness
- Excellent creep resistance
- Good corrosion resistance
- Easy to cast and machine
- High dimensional accuracy
- Vibration and damping capabilities
- Limitations:
- Increased brittleness
- High shrinkage
- Unsuitable for high-stress or high-temperature applications
- Higher cost
- Applications:
- Metal forming dies
- Plastic injection tools
- Industrial fittings and gears
- Automotive parts
- Household appliances
- ZA-8
ZA-8 is a zinc-based alloy with significant aluminum and copper content, known for its higher strength, hardness, and wear resistance compared to traditional zinc alloys.
- Composition:
- Zinc: 90%
- Aluminum: 8%
- Trace magnesium
- Copper: 1%
- Properties:
- Enhanced mechanical properties
- Creep resistance
- High fluidity for die casting
- Good plating and surface treatment compatibility
- Improved corrosion resistance
- Non-sparking
- Limitations:
- Prone to plastic deformation under pressure at high temperatures
- Dimensional changes after aging
- Brittleness
- Applications:
- Decorative products
- Bearings requiring minimal wear inserts and bushings
- Durable components where strength is critical
- Thin-walled parts
- Applications with aesthetic surface requirements
- ZA-12
ZA-12 is renowned for its high strength, hardness, and wear resistance, along with excellent castability and cost-effectiveness.
- Composition:
- Zinc: 88%
- Aluminum: 11%
- Trace magnesium
- Copper: 1%
- Properties:
- High strength
- Excellent wear resistance
- Good castability
- Dimensional stability
- Machinability and platability
- Limitations:
- Unsuitable for high-temperature applications
- Susceptible to hydrogen porosity (in some cases)
- Applications:
- Die casting
- Permanent mold casting
- Gravity casting
- Bearing components
- Engine parts
- Construction hardware
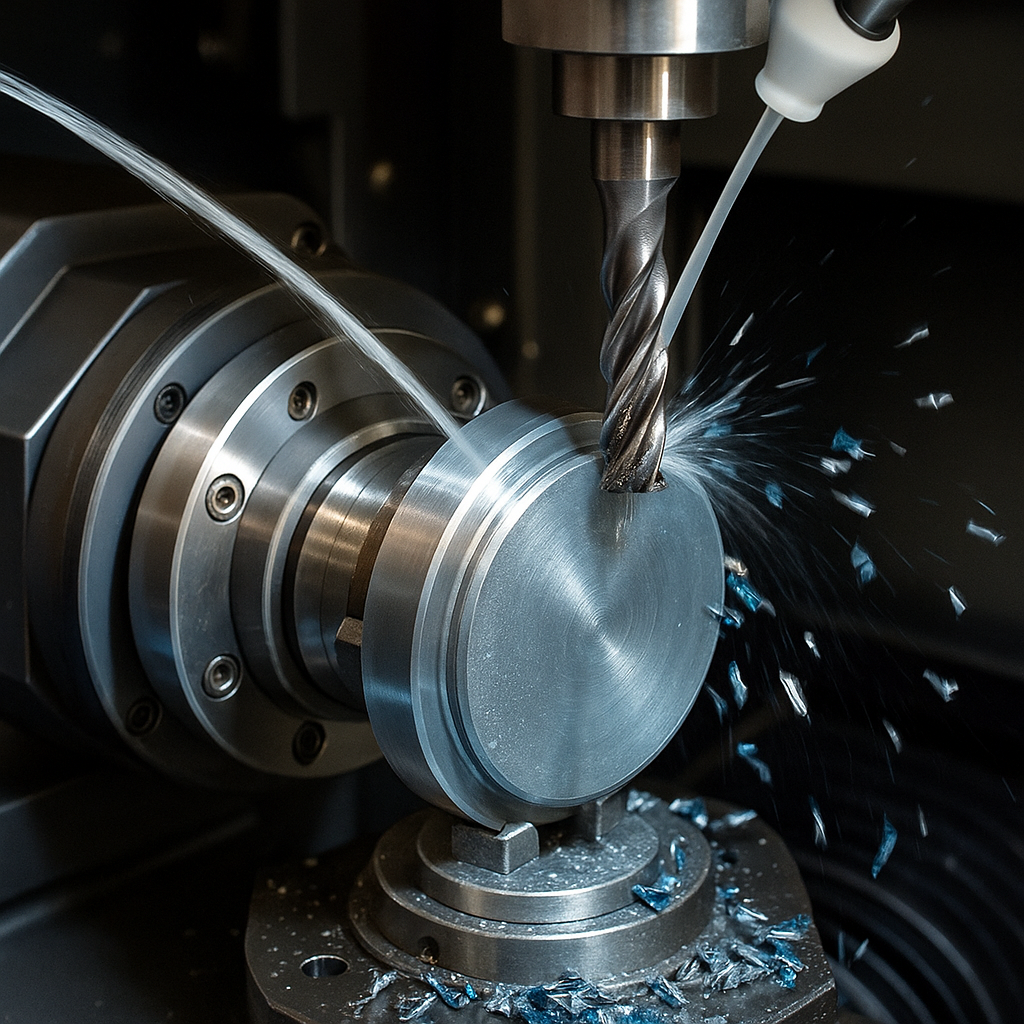
- ZA-27
ZA-27 is known for its high strength and light weight, primarily composed of zinc with significant aluminum and copper content.
- Composition:
- Zinc: 70%
- Aluminum: 28%
- Copper: 2%
- Properties:
- High strength
- Lightweight
- Good wear resistance
- Non-sparking property
- Limitations:
- Requires cold chamber die casting
- Shrinkage issues
- Reduced performance at high temperatures
- Unsuitable for electroplating
- Dimensional instability
- Applications:
- Bearing applications
- Automotive parts
- Machinery and tools
- Marine structural materials
- EZAC (Engineering Zinc Alloy Composition)
EZAC is mainly composed of zinc, aluminum, and other elements, offering higher creep resistance and strength than traditional zinc alloys.
- Composition:
- Zinc: Balance
- Aluminum: 4–8%
- Copper: 3–9%
- Properties:
- High creep resistance
- Enhanced strength and hardness
- Hot chamber processability
- Improved fluidity
- Good plating and finishing characteristics
- Limitations:
- Potential brittleness
- Corrosion sensitivity
- Limited high-temperature applications
- Applications:
- Automotive parts
- Electrical components
- Industrial equipment
- Consumer products
- Medical devices
- ACuZinc
Primarily composed of zinc, copper, and aluminum, with varying copper and aluminum contents depending on the application.
- Composition:
- Zinc: Balance
- Aluminum: 3–8%
- Copper: 5–10%
- Properties:
- Enhanced mechanical properties
- High wear resistance
- Cost-effective
- Limitations:
- Tool wear
- Limited working temperature range
- Applications:
- Automotive industry
- Bearing applications
- Electronic/electrical systems
- Tombak
Tombak is a copper-based alloy containing zinc as an alloying agent, along with other elements like tin, lead, or arsenic.
- Composition:
- Zinc: 28%
- Copper: 72%
- Properties:
- High luster
- Resistance to rust and corrosion
- Easy to work with
- Cost-effective
- Limitations:
- Lower strength
- Reduced machinability
- Unsuitable for high-strength applications
- Applications:
- Decorative items (art castings, historical artifacts)
- Coin plating
- Metal leaf
Optimized CNC Processes for Zinc Components
Machining processes for zinc milling can be optimized based on factors such as tool selection, cutting parameters, and material properties.
- High-Speed Milling Technology for Zinc
Machining zinc alloys (e.g., Zamak 3 and ZA-27) requires 5-axis CNC milling. This technology uses smaller tools and higher spindle speeds to minimize tool wear and improve productivity. CNC processes for zinc alloy milling are optimized with positive rake angle insert geometries, sharp edges, and potential dry cutting strategies. - Precision Thread Turning on Zinc
This method offers high precision and flexibility for machining threads on zinc alloys, ensuring consistent thread size and position with a better surface finish. It is suitable for medical and aerospace applications where precision is critical. - Micro-Drilling and Tapping on Zinc
Specialized tools are used to create small holes and threads in zinc materials, essential for complex designs, miniature components, and precision fastening applications. - EDM for Complex Zinc Cavities
Electrical Discharge Machining (EDM) is ideal for machining complex cavities in zinc, excelling in shaping intricate geometries and processing harder materials. The process uses an electrode with the cavity shape, immersing the workpiece in a dielectric fluid to apply discharges that erode the material.
Surface Treatments and Protective Coatings
Surface treatments and protective coatings form a barrier on the material surface, enhancing performance and service life, as well as improving aesthetics, durability, corrosion resistance, and functionality.
Zinc, Brass, and Stainless Steel in CNC Machining
Aspect | Zinc Alloys | Brass | Stainless Steel |
---|---|---|---|
Machinability | |||
Cutting Difficulty | Easier than stainless steel and brass | Easiest to cut | Hardest to cut due to high hardness |
Cooling Requirements | Requires coolant | Minimal coolant needed | Requires coolant |
Machining Speed | Moderate | Highest | Slowest |
Material Properties | |||
Tensile Strength | Lower | Moderate | Highest |
Thermal Conductivity | Moderate | Highest | Lowest |
Challenges and Solutions in Zinc Manufacturing Processes
- Control of Sticky Chip Formation
Zinc chips can become sticky due to low melting point and poor ductility, leading to poor surface finish and tool wear. Solutions include optimizing cutting parameters, using soft/lubricious coatings and coolant lubrication, and employing chip breakers to break long, sticky chips. - Thermal Management for Low-Melting Alloys
Zinc’s low melting point causes overheating, deformation, and surface defects during machining. Mitigation strategies include high-speed machining, high feed rates, optimized coolant/lubricant use, and appropriate tool geometry. - Burr Minimization and Edge Quality
Zinc alloys are prone to burrs and edge defects due to their ductility and deformability. Solutions include using sharp tools, reducing cutting speed, employing vibration-assisted machining for zinc alloys, and post-processing deburring methods. - Tool Coating and Wear Reduction
Zinc’s ductility causes adhesion to tools, leading to wear. Solutions include using specialized cutting tools with coatings (TiN, AlTiN, PVD), lubricious coatings, suitable tool geometry, and regular tool maintenance.
Design for Manufacturability (DFM) Guidelines for Zinc Alloys
DFM guidelines for zinc alloys simplify production and assembly, ensuring affordability and high quality:
- Set Minimum Wall and Rib Thicknesses: Ensure sufficient thickness to prevent cracking and withstand high stress in applications. Ribs with adequate thickness and spacing provide structural support without adding complexity.
- Incorporate Larger Fillet Radii and Draft Angles: Fillet radii at internal corners prevent stress concentration and improve material flow. Draft angles on vertical surfaces allow easy ejection from molds or dies.
- Plan Thread Inserts and Reinforced Bosses: Use thread inserts strategically for mounting/fastening, as direct threading in zinc is prone to strength loss. Reinforced bosses provide structural support and withstand pressure without failure.
- Control Tolerance Stack-up and Fit: Strict tolerance control ensures proper part fit and function. Design components with sufficient clearance for easy assembly and to prevent jamming.
Conclusion
Zinc offers excellent machinability, fast CNC processing, and minimal tool wear. Its low melting point can cause heat accumulation, but strategies like flood cooling minimize heat and softening. Zinc alloys are categorized into Zamak and ZA types: Zamak alloys are most common, known for superior die-casting performance and strength, while ZA alloys have higher aluminum content and enhanced strength.
For more information, contact Debaolong Seiko. You are also welcome to upload your designs to Debaolong Seiko for a quote.