Cavity milling is a CNC process that creates precision hollow parts in materials ranging from aluminum to titanium. While 60% of mold manufacturers rely on it, tool deflection and chip issues can undercut your efficiency. Want to slash machining cycles by 40%, triple tool life, and achieve Ra 0.4 µm surface finish? We’ll show you how with smart tool selection, CAM tricks, and 5-axis solutions.
What is Cavity Milling?
Cavity milling creates precise hollow spaces in molds, aerospace components, and medical implants. Unlike surface milling (which processes only the surface), cavity machining requires intelligent depth control, long-reach tools, and chip management to machine tight internal geometries.
How Cavity Milling Works
- Tool Engagement:
- A rotating end mill cuts into the material axially (plunging) or laterally (radial cutting) to carve out material layer by layer.
- Depth of cut (e.g., 0.5–2 mm per pass) depends on material hardness and tool rigidity.
- Material Removal:
- Roughing uses high feed rates and deep cuts to remove bulk material.
- Finishing employs light stepovers (5–10% of tool diameter) for smooth walls.
- Chip Evacuation:
- Compressed air or through-tool coolant clears chips from deep cavities to prevent re-cutting and tool wear.
Key features: Adaptability to complex designs, precision, and efficiency.
Cavity Milling vs. Pocket Milling
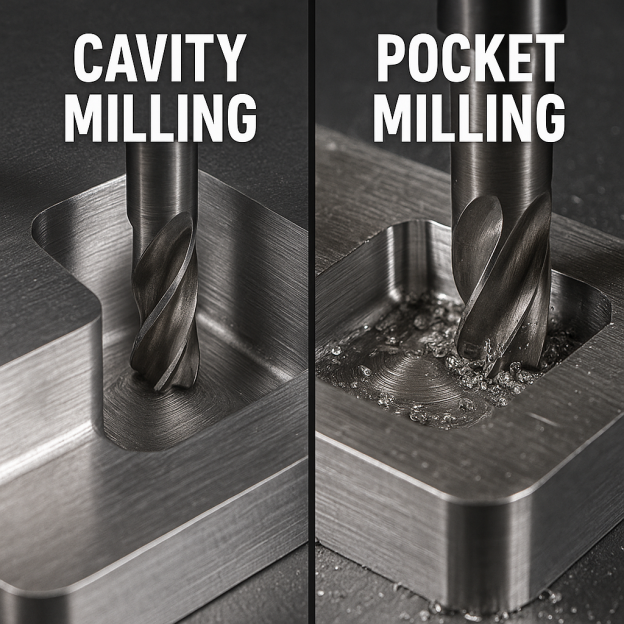
Aspect | Cavity Milling | Pocket Milling |
---|---|---|
Geometry | Deep internal spaces | Shallow recesses |
Tool Reach | Requires long-reach tools (10xD or more) | Uses standard tools (3–5xD) due to shallow depth |
Chip Evacuation | Challenging—chips trap in deep cavities; needs air flow or through-tool coolant | Easier—open design allows natural chip ejection |
Typical Industries and Part Examples
Cavity milling shines in precision industries. Three key cases demonstrate its impact on efficiency, tool life, and surface quality:
- Aluminum Mold Core
- Achievement: 40% shorter cycle time
- Method: Optimized toolpaths and efficient roughing
- Inconel Aerospace Housing
- Achievement: 3x longer tool life
- Method: High-speed machining (HSM) strategies
- Medical Implant Cavity
- Achievement: Ra 0.4 µm surface finish
- Method: Precision finishing paths with micro-grain tools
Common Challenges in Deep Cavity Machining
Deep cavity machining faces unique challenges affecting precision and efficiency: tool reach, stability, and chip management, which impact surface finish and tool life. Recognizing these issues helps select successful strategies.
- Limited Tool Access
- Standard tools often can’t reach deep cavity bottoms, leaving unfinished surfaces. A mold maker solved this by using extended-reach end mills for 150 mm aluminum cavities, ensuring full coverage.
- Overhang Rigidity
- Excessive tool overhang causes vibration and poor surface quality. A turbine blade manufacturer improved surface quality by 35% using tapered tool holders for nickel alloy parts. Minimizing overhang maintains precision.
- Tool Deflection
- Bending tools create tapered walls with size inaccuracies. An aerospace plant reduced taper errors by 50% using carbide tools with lower cutting forces. Stiffer tools prevent deformation.
- Poor Chip Evacuation
- Trapped chips re-cut the surface and damage tools. A medical implant manufacturer eliminated defects in titanium workpieces using 800 psi through-tool coolant. Proper chip clearance is critical.
- Vibration/Chatter
- Long cuts generate visible vibration waves and audible chatter. An automotive supplier reduced vibration by 60% using variable helix end mills for steel cavities. Dynamic toolpaths also help.
- Residual Material in Corners
- Remaining material in side corners requires extra passes. A mold maker achieved 90° sharp corners using smaller tools for rest machining. Proper planning avoids this issue.
Tool Selection for Reliable Cavity Cutting
Right tool selection is key to cavity machining success. Tools must maintain rigidity in deep cuts and withstand cutting forces, affecting tool life, surface finish, and efficiency.
- Cavity Cutting End Mills
- Choose end mills based on material and depth: Carbide for deep steel cavities, HSS for shallow aluminum, and PCD for composites. A turbine blade manufacturer tripled tool life using carbide for Inconel cavities.
- Necked-Down Milling Tools
- Necked-down mills provide depth reach without sacrificing rigidity, effectively machining deep features. An automotive mold maker achieved ±12 mm straightness in 0.02xD aluminum molds with necked-down mills.
- Tool Holders and Adapters
- Holders determine stability in deep cuts: Hydraulic holders enable extended reach, while shrink-fit holders offer max rigidity. A medical implant manufacturer reduced chatter by 40% using hydraulic holders with coolant for titanium.
Choosing Better CAM Toolpaths (Minimize Risks)
Optimal toolpaths help overcome deep cavity challenges and boost efficiency. Optimized strategies shorten cycles, extend tool life, and ensure precision in complex geometries.
- Cavity Milling vs. 3D Adaptive Roughing
- 3D adaptive roughing is a newer strategy: a high-speed toolpath that saves time by maintaining constant tool engagement. It cut a mold core in 3.2 hours (vs. 8.5 hours traditionally) while reducing tool wear.
- High-Speed Trochoidal Patterns
- Trochoidal milling maintains stable chip load, preventing tool overload. A jet engine manufacturer reduced breakage by 40% using this method for titanium cavities.
- Z-Level and Rest Machining Finishing
- These strategies clean up residual material in corners. A medical tool manufacturer achieved Ra 0.4 µm by combining Z-level and rest machining.
5-Axis Strategies for Complex Cavities
5-axis machining revolutionizes cavity milling by positioning tools at multiple angles. Unlike 3-axis machines limited to vertical approaches, 5-axis systems tilt and rotate tools to maintain optimal cutting conditions for complex geometries.
- 5-Axis Z-Level Finishing
- 3-axis machines struggle with deep cavities, causing tapered walls from tool deflection. 5-axis Z-level finishing keeps tools vertically engaged for straight walls and superior finishes. A turbine blade manufacturer eliminated 0.1° taper errors in Inconel fuel cavities with this method.
- Index and Cut Undercuts (3+2 Axis)
- This hybrid approach locks two rotary axes while using three linear axes for cutting, enabling undercuts without complex 5-axis machining. A mold maker reduced setup time by 3% using “3+2” machining for aluminum cores with side features.
- Smooth 5-Axis Surface Paths
- Equidistant toolpaths maintain consistent stepover on contoured surfaces, while free-form path milling follows organic shapes. An aerospace supplier achieved mirror finishes (Ra 0.2 µm) on titanium housings with dynamic 5-axis surface strategies.
How to Maintain Tool Stability in Deep Cavities
Stable tools are essential for precision deep cavities. Proper techniques prevent vibration and deformation, ensuring tool life and quality.
- Optimize Stepdown & Stepover
- Balance stepdown (10–15% of diameter) and stepover (30–50%) for stability. A mold maker reduced tool breakage by 40% using these values for steel cavities.
- Rough First, Mill Corners Later
- Remove bulk material first, then gently clean corners. This two-step method reduced excessive stress for an aerospace plant, improving titanium surface finish by 60%.
- Mid-Process Wall Probing
- Probing after roughing detects errors early. A medical device manufacturer avoided scrap by verifying dimensions before finishing critical implants.
- CAM Software Programming
- Use NX, Fusion, or Mastercam to optimize toolpaths. A supplier halved programming time and extended tool life with adaptive programming.
Conclusion
Mastering cavity milling lets you cut faster, last longer, and finish better. With the right tools, strategies, and CAM technology, you’ll tackle deep cavities with confidence and precision. Apply these methods today to witness real improvements in your machining results.
For more information, contact Debaolong Seiko. You’re welcome to upload your designs to Debaolong Seiko for a quote.