What is Trochoidal Milling?
Trochoidal milling is a CNC dynamic machining method that uses a spiral tool path to create overlapping circular cuts. Ideal for high-speed machining, heavy material removal, and difficult-to-machine materials, this technique relies on principles of intermittent tool engagement, high axial depth of cut, and low cutting forces.
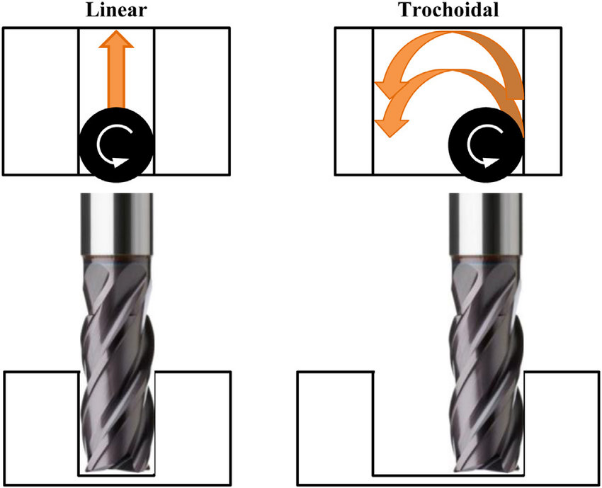
Trochoidal Milling vs. Conventional Milling
Definitions and Core Concepts
Derived from the Greek “trochos” (meaning “wheel”), trochoidal milling refers to a wheel-like circular path where a tool follows a curve formed by a rolling circle. The core principle is using a large axial depth of cut (ADOC) with a small radial depth of cut (RDOC) to maximize material removal while minimizing tool wear and heat generation.
Key Differences
Trochoidal Milling | Conventional Milling |
---|---|
Uses spiral tool paths (not linear) to remove material. | Relies on straight or traditional linear paths. |
Dynamic motion ensures lower heat and cutting forces. | Generates higher heat and forces during continuous engagement. |
Small RDOC limits tool-workpiece contact, with high ADOC for high material removal. | Typically uses larger RDOC, increasing tool stress and wear. |
Reduces tool wear, extending tool life. | Prone to faster tool degradation. |
How Trochoidal Tool Paths Work
Programming Trochoidal Paths in CAM
CAM software defines parameters like feed rate, tool entry/exit zones, and cutting depth, adjusted based on material, surface finish requirements, and machine capabilities.
Circular Entry and Continuous Arc Motion
- Circular Entry/Exit: Minimizes tool load, especially for sharp corners.
- Continuous Arc Motion: The tool maintains a circular path, steadily 切入 the workpiece. Trochoidal paths enable efficient chip evacuation and prevent chip buildup.
Constant Chip Thickness Cutting
By controlling RDOC and feed rate, trochoidal milling maintains uniform chip thickness, reducing cutting forces. The small engagement arc enhances process stability.
Heat Dissipation and Chip Evacuation
The spiral tool path facilitates efficient heat dissipation from the cutting zone. Small RDOC and uniform chip thickness promote better chip formation and evacuation, ensuring clean cuts.
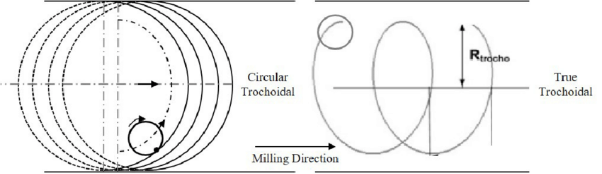
Advantages and Disadvantages of Trochoidal Milling
Advantages
- Higher Material Removal Rate: Faster cutting with deeper axial depth compared to conventional milling.
- Longer Tool Life: Reduced heat and stress on the tool due to intermittent engagement.
- Cost-Effective: Less downtime for tool replacement.
- Efficient Chip Evacuation: Prevents re-cutting and chip-related issues.
- Better Surface Finish: Reduced heat and intermittent cutting minimize workpiece damage.
Disadvantages
- Specialized Skills Required: Needs CAM software and programming expertise for complex tool paths.
- Machine Limitations: Not all CNC machines support trochoidal or dynamic milling.
- Component Wear: Constant radial motion may accelerate wear on CNC machine ball screws and guides.
When Trochoidal Milling Is Not Ideal
- Ineffective for large open-face milling, soft materials, or shallow cavity machining, where its advantages (low tool wear, high material removal) are underutilized. Conventional milling is preferable here.
Key Parameters for Trochoidal Cutting (Example: Inconel 718)
Optimal Stepover (ae)
For Inconel 718, a stepover of 10% of the tool diameter is recommended to control cutting forces and ensure good surface finish.
Feed per Tooth and RPM Range
- Feed per Tooth: 0.1 mm is a starting point for Inconel 718, adjustable based on tool and machine performance.
- RPM Range: 1000–6000 RPM for Inconel 718, varying by tool and material specifics.
Engagement Angle Calculation
- Engagement Angle = (2 × Contact Arc) / Tool Diameter.
- The contact arc is the distance the tool travels along the part’s circumference in one cycle.
Quick Formula for Slot Width ≤ ½ × Tool Diameter
Calculate the maximum tool diameter based on slot width and required stepover.
Free Online Feed/Speed Tool
Use the Hoffman Group machining calculator for cutting parameter calculations.
Tool and Machine Requirements
Recommended End Mill Geometry
- Solid carbide end mills with high-performance coatings, at least 5 flutes, and vibration-dampening features.
- Machines must support dynamic motion and have dedicated CAM software.
Tool Holders and Vibration Control
- Hydraulic chucks and shrink-fit systems are preferred.
- Combine with vibration-dampening holders to reduce vibrations and optimize cutting parameters.
Machine Essentials
- High-Speed Pre-reading: Predicts the next cut to optimize efficiency and tool life.
- High-Pressure Coolant: Ensures safe tool operation, heat dissipation, and chip evacuation.
Best Application Scenarios
- Deep Slots and Pockets in Steel/Inconel: Enables large ADOC with small RDOC, reducing tool wear in tough materials like Inconel or titanium.
- Micro-Machining Thin Walls: Uses small-diameter tools with minimal heat generation, lowering tool breakage risks.
- Roughing Hard or Heat-Treated Materials: Maintains small engagement angles to minimize tool wear in hard-to-machine materials.
- Trochoidal Turning for Lathe Grooving: A variant for lathe grooving, offering low cutting forces and suitability for difficult materials.
Troubleshooting and Quick Fixes
- Excessive Tool Wear: Reduce engagement angle, adjust cutting speed, or use wear-resistant coatings.
- Poor Chip Evacuation: Use air blasts or mist cooling; choose tools with chip-breaker features or large helix angles.
- Vibration Marks: Use variable helix tools to disperse cutting forces, or reduce feed rate.
Conclusion
Trochoidal milling is a CNC machining technique using spiral tool paths with overlapping circular cuts, ideal for high-speed machining, deep slots, and hard materials. By using small RDOC and large ADOC, it reduces cutting forces, heat, and tool wear, making it suitable for difficult materials, 3D cavities, non-ferrous metals, deep slots, and vibration-sensitive applications.
For more information or to upload your design for a quote, contact Debaolong Seiko.