Why Are Nickel Alloys Difficult to Machine?
Nickel alloys pose significant machining challenges due to their abrasive nature, rapid work hardening, and heat accumulation. These factors lead to accelerated tool wear, dimensional errors, and potential warping from high temperatures.
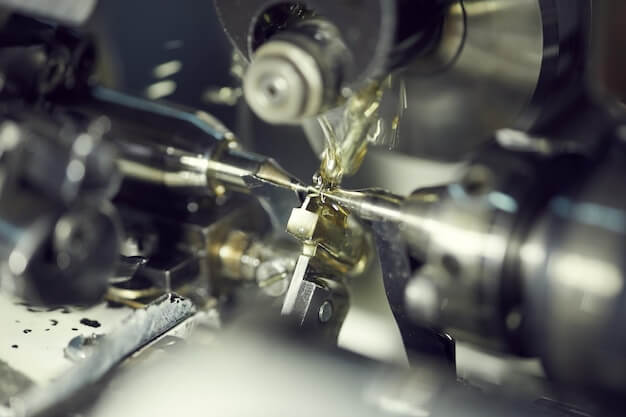
Material Properties of Nickel and Nickel-Based Alloys
Nickel and its alloys are renowned for corrosion resistance, high strength, and heat tolerance. Alloying with other elements creates unique properties, while nickel plating enhances performance for various metals.
- High Tensile Strength & Elasticity: Nickel alloys exhibit tensile strengths up to 1,000 MPa and Young’s modulus of 210 GPa, far exceeding pure nickel, due to enhanced mechanical properties from alloying.
- Low Thermal Conductivity & Heat Concentration: Alloying agents disrupt nickel’s atomic lattice, reducing thermal conductivity (e.g., pure nickel: 106 W/mK; alloys: lower).
- Chemical Reactivity with Cutting Tools: High machining heat and abrasive carbides in alloys cause adhesive and diffusive wear on tools.
Nickel Alloy Groups and Relative Machinability
High nickel content (25–65%) boosts corrosion resistance but complicates machining due to high work hardening and shear strength.
Pure Nickel Grades (Nickel 200/201):
UNS N02200/N02201 are extremely difficult to machine due to sticky, stringy chips that tangle on tools. Nickel 201 generates excessive heat, causing rapid tool wear. Solutions: sharp tools, adequate feed rates, and cutting depth to avoid work hardening.
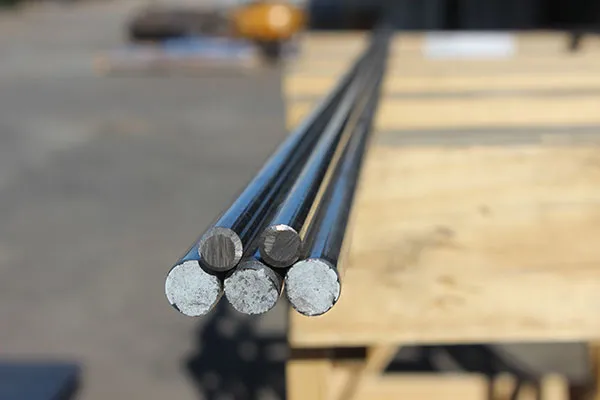
Ni-Cr Austenitic Alloys (Alloys 600, 625):
Face-centered cubic structure offers excellent corrosion resistance, non-magnetic properties, and machinability in annealed states. Use carbide or HSS tools for CNC machining.
Superalloys (Inconel 718, 725):
Critical for aerospace and oil & gas, these alloys feature low thermal conductivity and rapid work hardening, leading to poor surface finish, fast tool wear, and high cutting forces.
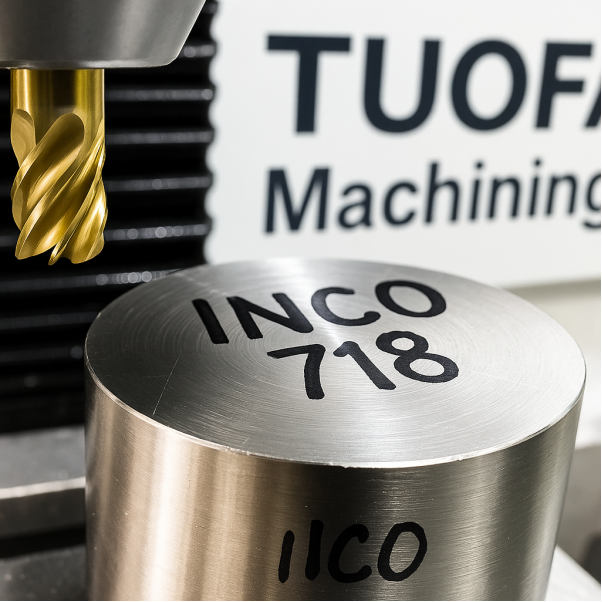
Cast vs. Wrought Nickel Materials
- Cast Nickel 201: Formed by pouring molten metal into molds, prone to porosity and microstructure inconsistency, making machining difficult.
- Wrought Nickel: Shaped via forging/rolling, with uniform microstructure and higher ductility, enabling easier machining.
5 Core Machining Operations: Challenges & Solutions
- Turning Nickel Alloys
- Challenge: Work hardening, heat generation, tool wear.
- Solution: Carbide/ceramic tools with positive rake angles, high cutting speeds, and steady coolant flow.
- Milling Nickel Alloys
- Challenge: Work hardening, chip buildup, vibration.
- Solution: Positive rake angle tools, high-power machines, avoid low feed rates.
- Drilling & Reaming
- Challenge: High temperatures, tool wear, work hardening.
- Solution: Cobalt drills, consistent speeds, and coolant for deep holes.
- Tapping & Thread Milling
- Challenge: Work hardening, tool wear.
- Solution: High-quality taps, proper coolant, and controlled threading speeds.
- Grinding & Honing
- Challenge: Wheel wear, poor surface finish from high hardness.
- Solution: Tough, ductile grinding wheels, optimized parameters, and coolant.
Heat & Chip Management Techniques
- Liquid Nitrogen Cryogenic Machining: Ideal for Inconel 718, reduces cutting forces and extends tool life by rapidly cooling the cutting zone.
- Indexable Inserts with Optimized Coolant Ports: Enhance heat dissipation, lubrication, and chip evacuation for better surface finish.
- Tool Path Strategies: Minimize dwell and re-cutting with strategies like stock removal, smooth tool paths, and optimized parameters.
Safety in Nickel Alloy Machining
- Key Risks: Nickel dust/fumes can cause respiratory issues; fine chips pose fire hazards.
- Safety Tips:
- Control dust with high-pressure coolant and proper ventilation.
- Store fine chips in dry, cool environments.
- Use PPE and follow coolant disposal protocols.
Cutting Data & Coolant Guidelines
- Parameters: Use lower cutting speeds/feed rates; prioritize tool quality.
- Coolants: Water-soluble coolants are critical for heat dissipation, lubrication, and chip evacuation.
- Intermittent Cutting: Controls heat and tool wear in precision turning.
Real-World Applications & Case Studies
- Aero Turbine Disks from Inconel 718:
GEAE tested three forged Alloy 718 variants: standard, high-strength, and direct-aging treatments, with the latter optimizing disk performance via high forging reduction and aging. - Oil & Gas Valves from Alloys 625/825:
Both resist high pressure, temperature, and H₂S; Alloy 625 offers superior performance at higher cost, while 825 balances cost and efficiency. - Medical Nitinol Components:
Nickel-titanium alloys excel in wires and stents due to superelasticity and shape memory, processed via laser cutting, EDM, and wire forming.
Conclusion
Nickel-based alloys’ strength and hardness demand high cutting forces, accelerating tool wear and heat accumulation. Their chemical reactivity and tendency to chip under shear stress further complicate machining. CNC operations often find nickel harder to machine than titanium, requiring specialized parameters and processes. For professional solutions, contact Debaolong Seiko for expertise in nickel alloy machining from CAD to production.
For more information, please contact us at Debaolong Seiko. You are also welcome to upload your designs to Debaolong Seiko to get a quotation.