The automotive industry demands materials that are lightweight, fuel-efficient, and capable of enhancing vehicle performance. Aluminum and its alloys have emerged as one of the most common materials meeting all these criteria. Additionally, aluminum is durable, corrosion-resistant, versatile, safe, and reliable. Most notably, its performance evolves alongside advancements in vehicle models, ensuring automotive aluminum remains a standout choice among materials. Common applications of aluminum in automotive manufacturing include components like cylinder heads, rims, and body panels.
Is Aluminum Suitable for Automotive Parts?
Yes, aluminum is well-suited for manufacturing automotive parts. It offers lightweight properties, high corrosion resistance, excellent fracture toughness, and a superior strength-to-weight ratio. These characteristics contribute to better fuel efficiency, durability, and safety. However, due to higher maintenance costs compared to stainless steel, aluminum is typically reserved for specific metal components.
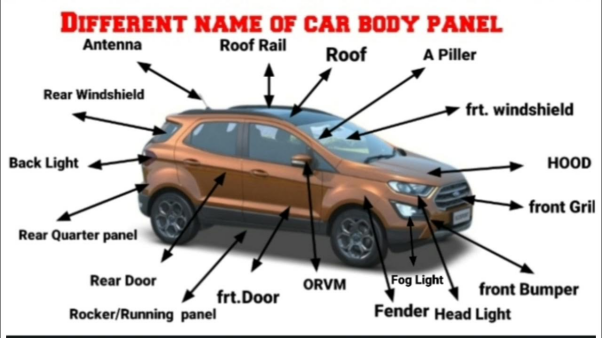
Aluminum Automotive Parts Manufacturing Processes
CNC Machined Aluminum Parts
CNC machining is an automated, computer numerical control (CNC) technology used to produce complex, precision metal automotive parts. Its advantages include high-speed production, tight tolerances, repeatability, and reduced cycle times, which boost productivity. However, this method is costly for aluminum automotive components and is often limited to specific parts.
Aluminum Die Castings
Die casting is an industrial manufacturing process where molten aluminum is poured into molds under high temperature and pressure. Once cooled, the part solidifies and can be easily removed from the mold. This method is widely used for OEM parts and components in aerospace, medical, electronics, and other industries.
Sheet Metal Aluminum Parts
Sheet metal processing involves shaping thin, flat aluminum sheets into various forms through stamping, bending, cutting (laser, water jet, plasma, or mechanical), and welding. Bending, which induces plastic deformation in aluminum alloy parts, is a common technique. Cutting processes are also integral to fabricating automotive components.
Aluminum 3D Printing in Automotive Manufacturing
3D printing constructs 3D OEM parts by layering materials, applicable to both plastic and aluminum models. Metal 3D printing, which uses lasers to melt and fuse metal powder, is employed for prototyping and producing durable, high-strength metal automotive components.
Aluminum Forging in Automotive Parts Production
Forging is a process that heats and presses aluminum to create lightweight automotive components. It is used to manufacture engine blocks, transmissions, suspension parts, and wheel hubs.
Benefits of Aluminum Automotive Components to the Automotive Industry
- Improved Fuel Efficiency and Performance
Aluminum body materials are 24% lighter than steel. Lightweight components enhance body panel performance and fuel efficiency. Aluminum’s low density and high strength enable thinner panels, better acceleration, and improved handling. - Enhanced Safety and Impact Resistance
Aluminum components offer high impact resistance and fracture toughness, with excellent energy absorption to enhance safety during accidents. They are less prone to failure and reduce braking distances, while their tendency to expand during deformation adds another safety layer. - Corrosion Resistance and Longevity
Aluminum alloys resist corrosion, performing well in harsh environments. Unlike steel, they are less susceptible to wear, ensuring longer service life and durability. - Lightweight Design and Better Handling
Aluminum’s density is one-third that of steel, making it cost-effective to transport and handle while enabling a lighter, more compact overall structure. Its lightweight nature also improves aerodynamics, making it ideal for automotive and aerospace applications. - Eco-Friendliness and Recyclability
Aluminum’s recyclability makes it an environmentally friendly and cost-effective choice. Recycling aluminum incurs no material loss and reduces carbon emissions, minimizing environmental impact.
Challenges of Using Aluminum in Automotive Parts
- Low Melting Point
Aluminum melts at 660°C and is difficult to weld due to oxidation (burning) before melting. Its mechanical strength declines at 200–250°C, limiting its use in high-temperature applications. - Susceptibility to Galvanic Corrosion
While aluminum resists corrosion under normal conditions, it is prone to electrochemical (galvanic) corrosion when in contact with other metals in the presence of an electrolyte. To mitigate this, metals with similar electrochemical potential to aluminum should be paired. - Higher Cost Compared to Some Metals
Extracting pure aluminum from bauxite and other compounds is energy-intensive and time-consuming, making aluminum more expensive than some alternatives.
Why Aluminum Is a Top Choice for Automotive Parts
Compared to steel and other materials, aluminum stands out for:
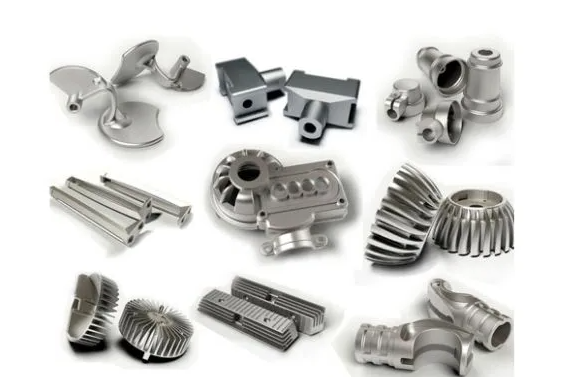
- High Strength and Durability
Aluminum is durable, versatile, and offers a high strength-to-weight ratio, matching steel’s strength at a fraction of the weight. - Lightweight and Flexibility
Aluminum is one-third the weight of steel, improving fuel efficiency, acceleration, and handling. Its high ductility allows easy formation into complex shapes. - Corrosion Resistance and Longevity
Aluminum resists corrosion in harsh environments, wears less than steel, and has a longer service life. - Thermal and Electrical Conductivity
Aluminum is an excellent conductor of heat and electricity, enhancing its mechanical performance and heat absorption capabilities. - Ductility and Formability
Aluminum’s softness and ductility allow it to be shaped into complex forms without expensive preprocessing, reducing production costs.
Common Aluminum Alloys for Automotive Components
5000 Series Aluminum (Marine Grade)
5052 aluminum alloy, known for high durability and ductility, is ideal for lightweight body panels and fuel tanks.
6000 Series Aluminum (Structural Applications)
6061 alloy, part of the 6000 series, offers high mechanical strength and corrosion resistance, making it suitable for structural parts and body panels.
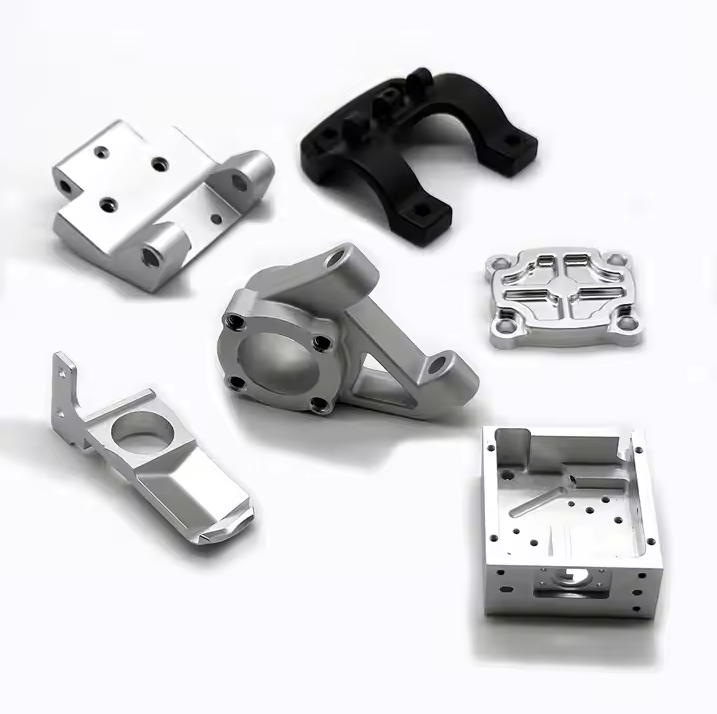
7000 Series Aluminum (High-Strength Applications)
7075 aluminum alloy boasts an exceptional strength-to-weight ratio, perfect for high-performance, lightweight components.
Selecting the Right Aluminum Alloy for Specific Parts
Alloy selection depends on performance, maintenance, and cost. 6061 aluminum (alloyed with silicon and magnesium) is widely used for its high strength, heat treatability, anodizability, and excellent surface quality. For specialized applications, 3000, 4000, and 5000 series alloys are also employed.
Examples of Aluminum Automotive Parts
- Body Panels and Frames
Frames, hoods, fenders, bumpers, spoilers, roof racks, grilles, trunk liners, windows, and doors. - Wheels
Rims and hubcaps, chosen for lightweight properties and performance. - Radiators and Heat Exchangers
Crankcases, pistons, intake manifolds, radiators, cylinder blocks, and cylinder heads. - Chassis and Suspension Components
Suspension parts, frames, struts, windshield frames, and brake systems. - Interior and Miscellaneous Parts
Door handles, consoles, trim pieces, transmission cases, gearboxes, and drive shafts.
Aluminum in Motorsports
Aluminum is widely used in racing due to its high strength and corrosion resistance; aluminum alloys often outperform low-carbon steel.
- High-Performance Components
Aluminum alloys with strengths exceeding 1,000MPa offer twice the impact resistance of steel with equivalent strength, absorbing and dispersing impact energy evenly to enhance safety. - Applications in Formula 1 and Racing Cars
Aluminum is used in engine components (cylinder heads, valve covers, intake/exhaust manifolds, blocks), spring plates, locknuts, and low-stress transmission parts.
Aluminum vs. Steel Automotive Parts: Performance Comparison
Performance Factor | Aluminum Parts | Steel Parts |
---|---|---|
Strength | High strength-to-weight ratio | Higher absolute strength but heavier |
Weight | 40% lighter than steel | Heavier and thicker |
Cost | More expensive | Cost-effective |
Corrosion Resistance | Good | Higher (with proper treatment) |
Durability | Good | Better resistance to bending/cracking |
Maintenance | Lower requirements | Moderate requirements |
The Role of Aluminum in Future Electric Vehicles (EVs)
Aluminum will reduce EV weight and improve efficiency, enhancing braking distance and overall handling. Its use in battery enclosures, conductors, trays, cooling systems, motor housings, cabin heaters, and body structures will further boost performance.
How to Polish Aluminum Automotive Parts
- Thoroughly clean the surface with a degreaser.
- Use fine sandpaper to remove minor scratches.
- Apply polish and buff in circular motions with a soft cloth.
- Shine with a microfiber cloth for a glossy finish.
- Apply a sealant to prevent oxidation.
How to Clean Cast Aluminum Parts
- Use mild detergent or water for basic cleaning.
- For heavy grime or oxidation, use vinegar solution or commercial aluminum cleaners.
- Wipe with a soft cloth to avoid scratches; polish afterward to restore shine.
How to Paint Aluminum Automotive Parts
- Clean the surface to remove dirt and grease.
- Sand lightly with fine sandpaper.
- Apply self-etching primer.
- Use high-quality acrylic or epoxy paint for durability and chemical resistance.
- Finish with gloss or matte topcoat and a sealant to protect the paint.
For more information, contact Debaolong Seiko. You are also welcome to upload your designs to Debaolong Seiko for a quote.