What Is Aluminum Bronze?
Aluminum bronze is an alloy composed primarily of copper and aluminum, with small additions of other elements. Valued for its durability, it excels in harsh environments like seawater, making it a staple in aerospace and marine industries.
Is Aluminum Bronze Easy to Machine?
No, it presents significant challenges due to:
- High strength
- Excellent wear resistance
- High thermal conductivity
- Copper content (causing adhesion)
- Poor chip formation
Cost of Machining Aluminum Bronze
Due to its high thermal conductivity, problematic chip formation, and copper content, machining costs average around $3.00 per minute.
Key Properties of Aluminum Bronze Alloys
- High wear resistance
- Strong and durable
- High thermal conductivity
- High copper content
- Poor chip formation
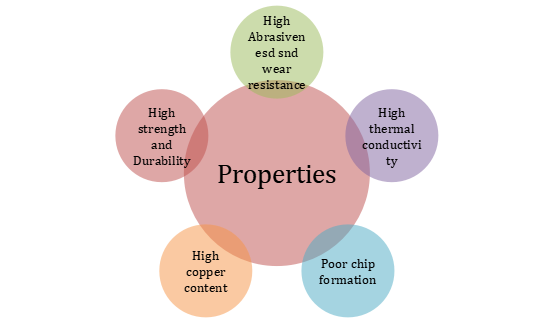
Aluminum Bronze Grades and Their Machinability
C63000 Nickel Aluminum Bronze
More manageable with modern CNC equipment, but requires effective lubrication to achieve tight tolerances.
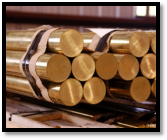
C95400 Aluminum Bronze
Offers moderate machinability. Optimal results require carbide tooling and coolants to combat overheating.

954 Aluminum Bronze
Identical to C95400, with similar machining characteristics.
CA104 Aluminum Bronze
Boasts good mechanical properties and machinability, but demands precise cutting speeds and parameters for optimal performance.
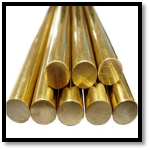
Def Stan 02-833 and NES 833 Alloys
Rated only 20% as machinable as brass. Processing these alloys requires specialized tooling, coolants, and skilled operators.
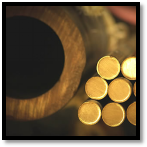
Applications in Defense and Specialty Industries
Aluminum bronze’s seawater corrosion resistance makes it ideal for marine use, while its high strength-to-weight ratio benefits aerospace applications.
Challenges in Aluminum Bronze Machining
Tool Wear and Abrasiveness
The alloy’s hardness and abrasiveness accelerate tool wear, reducing tool life and increasing production costs.
Heat Dissipation and Thermal Management
High thermal conductivity causes rapid heat buildup, risking tool damage and dimensional inaccuracies without proper cooling.
Maintaining Dimensional Accuracy and Surface Finish
Copper content leads to adhesion issues, resulting in poor surface quality. Achieving tight tolerances requires careful parameter control.
Poor Chip Formation and Evacuation
Chips tend to be stringy and difficult to clear, leading to clogging and potential damage to tools or workpieces.
Typical Components and Industries
Aluminum bronze is widely used in:
- Marine equipment
- Aerospace components
- Industrial machinery
- Automotive parts
- Oil and gas sector
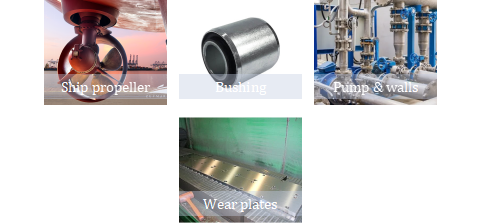
Performance Benefits in Marine, Aerospace, and Industrial Applications
- Mechanical strength
- Durability under high pressure
- Spark-resistant properties
- Thermal stability
- High strength-to-weight ratio
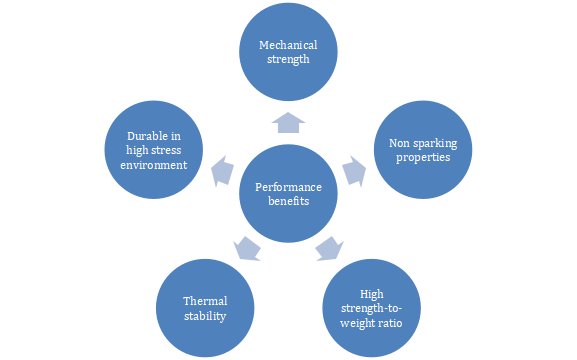
Best Practices for Machining Aluminum Bronze
Selecting the Right Cutting Tools
Use carbide or coated carbide tools, known for durability and wear resistance, to combat heat and abrasion.
Recommended Cutting Speeds and Feeds
- Cutting speed: 60–120 mpm
- Feed rate: 0.1–0.5 mm/rev
Adjustments may be needed to avoid overheating.
Lubrication and Cooling Techniques
Synthetic coolants are critical for reducing tool damage by managing heat and minimizing friction.
Strategies to Reduce Tool Wear
- Regular tool maintenance
- Precise adjustment of machining parameters
- Avoiding work hardening in the alloy
Heat Treatment and Its Impact on Hardness
For enhanced hardness and strength (critical for high-stress or harsh-environment applications), aluminum bronze undergoes:
- Solution heat treatment
- Aging for a specific duration
This process maximizes hardness, ensuring performance in demanding conditions.
Surface Finish Options for Aluminum Bronze Parts
Polishing and Coating
- Mechanical or electrolytic polishing: Improves surface smoothness and longevity.
- Specialized coatings: Applied via tribology labs to enhance wear resistance.
Corrosion-Resistant Treatments
- Anodizing
- Thermal spraying
- Diffusion treatments (e.g., nitriding)
These processes extend part life in corrosive environments.
Quality Control and Standards
To ensure quality:
- Conduct initial visual inspections.
- Adhere to international standards.
- Perform destructive and non-destructive testing as needed.
For more information or to upload your design for a quote, contact Debaolong Seiko.