CNC thin-wall machining is critical in the aerospace industry, where precision, weight reduction, and structural integrity are paramount. However, machining thin-wall parts presents challenges such as deformation, poor rigidity, and difficulty maintaining surface quality. This guide outlines best practices and techniques to overcome these hurdles, ensuring high-quality, cost-effective production.
Key Challenges in Thin-Wall Part Machining
Machining thin-wall components requires careful planning and execution. Below are the primary challenges and their solutions:
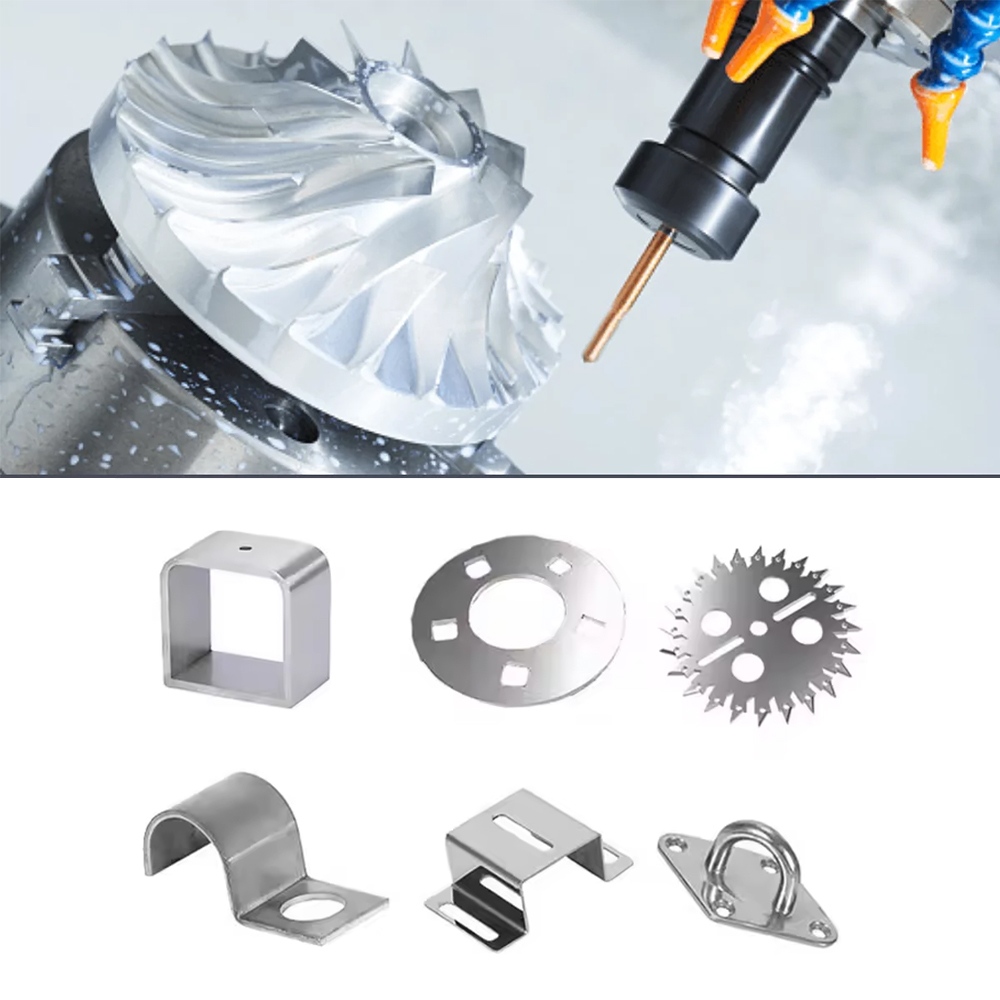
How Thin Can Metals Be Machined?
The minimum achievable thickness in CNC machining depends on material properties, machine capabilities, and tooling. General guidelines:
Material | Minimum Machinable Thickness | Typical Applications |
---|---|---|
Aluminum | 0.5 mm (0.02 in) | Aerospace panels, housings |
Titanium | 1.0 mm (0.04 in) | Engine components |
Stainless Steel | 0.8 mm (0.03 in) | Structural parts |
Magnesium | 0.6 mm (0.024 in) | Lightweight frames |
Precision CNC machining ensures these thin materials can be shaped without compromising structural integrity, though achieving such limits demands advanced tools and strict process control.
Poor Rigidity and Structural Fragility
Thin-wall parts inherently lack rigidity, leading to:
- Vibration: Degrades surface finish and dimensional accuracy.
- Deflection: Parts bend under cutting forces, causing inaccuracies.
Solutions:
- Toolpath Optimization: Use adaptive toolpaths to distribute cutting loads evenly.
- Clamping: Apply uniformly distributed clamping force to minimize deflection.
- Cutting Strategy: Prefer climb milling over conventional milling to reduce tool pressure (details below).
Part Deformation in Thin-Wall Structures
Deformation is a major issue due to low rigidity and high cutting forces.
Techniques to Reduce Deformation:
- Progressive Machining: Gradually reduce cutting depth to minimize stress.
- Low Cutting Forces: Use smaller cutting depths and feed rates.
- Pre-Stressing: Apply external force during machining to counter internal stress.
Common Causes of Deformation:
Cause | Description |
---|---|
High Cutting Forces | Excessive force bends or twists thin walls. |
Heat Accumulation | Localized heat distorts the metal structure. |
Clamping Pressure | Uneven or excessive clamping deforms fragile walls. |
Workholding Solutions for Thin-Wall Parts
Choosing the right workholding technique is critical to precision and part integrity.
Workholding Techniques:
Method | Advantages | Disadvantages |
---|---|---|
Vacuum Clamping | Uniform pressure distribution; ideal for precision parts | Limited clamping force; unsuitable for heavy machining |
Mechanical Clamping | Higher force; secure grip | May deform fragile parts |
Vacuum clamping suits lightweight or precision thin-wall components, while mechanical clamping is better for sturdier parts.
Fixture Design for Complex Geometries
For irregular or complex thin-wall parts, custom fixtures are often necessary:
- 3D-Printed Fixtures: Custom, lightweight, and precisely shaped to support thin sections.
- Modular Clamping Systems: Adjustable fixtures for versatile geometries.
Custom fixtures improve stability and reduce deformation risk.
Tool Selection for CNC Thin-Wall Machining
Tool choice is vital for maintaining precision and minimizing defects.
Choosing the Right Tools:
Tool Type | Advantages | Recommended Applications |
---|---|---|
Carbide Tools | High wear resistance; maintains sharp edges | Hard materials like titanium |
Necked-Down Mills | Reach deep into thin-wall structures | Aluminum, magnesium, and steel components |
Diamond-Coated Tools | Extreme hardness; reduces wear | Precision aluminum and high-strength alloys |
Proper tool geometry and material reduce cutting forces and improve surface finish.
Special Considerations for Aluminum Thin-Walls
Aluminum, widely used in aerospace for its strength-to-weight ratio, is prone to chatter during machining.
Tips for Aluminum Machining:
- Sharp Cutting Tools: Prevent excessive material deformation.
- Large Helix Angle Tools: Improve chip evacuation and reduce vibration.
- Coolant: Control heat and minimize thermal expansion.
Optimizing Cutting Speeds and Feed Rates
Balancing speed and precision is critical for thin-wall parts.
Balancing Speed and Accuracy
High speeds cause heat buildup (leading to warping), while low speeds extend cycle times. Optimization methods:
- Reduced Cutting Depth: Minimize heat and cutting forces.
- Adjust Feed Rates: Slow for precision; faster for roughing.
- Coolant: Prevent overheating, vital for thin materials.
Benefits of High-Speed Machining (HSM)
HSM is advantageous for thin-wall parts:
- Shorter Cycle Times: Higher spindle speeds accelerate production.
- Better Surface Finish: Reduced heat exposure minimizes deformation.
- Longer Tool Life: Lower tool pressure reduces wear.
Parameter | Traditional Machining | High-Speed Machining (HSM) |
---|---|---|
Feed Rate | Low | High |
Spindle Speed | Medium | High |
Cutting Depth | Medium-High | Low |
Cycle Time | Long | Short |
Toolpath Optimization for Thin-Wall Machining
Optimized toolpaths control forces exerted on thin-wall parts.
Advanced Toolpath Strategies
Adaptive toolpaths (e.g., High-Efficiency Machining, HEM) distribute cutting forces evenly, reducing pressure on parts and maintaining dimensional accuracy.
Advantages of Adaptive Toolpaths:
- Lower Cutting Forces: Reduce deformation risk.
- Longer Tool Life: Less stress on cutting edges.
- Consistent Material Removal: Better surface finish.
Climb Milling vs. Conventional Milling
Milling Type | Performance | Best Use Cases |
---|---|---|
Climb Milling | Lower cutting forces, less heat, smoother surfaces | Thin-wall parts |
Conventional Milling | Better for hard materials; lower rigidity requirements | Bulk material removal |
Climb milling is preferred for thin walls, as it produces smoother surfaces and reduces cutting forces, minimizing deformation.
Deformation Control
Deformation in thin-wall parts stems from multiple factors; understanding them aids process planning.
Factors Causing Deformation:
Factor | Impact |
---|---|
Cutting Forces | Bending or twisting of components |
Heat | Expansion and distortion |
Clamping Pressure | Deformation from uneven/excessive force |
Material Stress | Residual stress from raw material processing |
Process Optimization:
- Optimize Toolpaths: Use adaptive strategies to reduce cutting loads.
- Control Temperature: Employ coolant systems and minimize dwell times.
- Select Appropriate Materials: Use materials with low residual stress.
Auxiliary Support Technologies
Auxiliary technologies significantly enhance thin-wall machining precision.
CNC Compensation Techniques
Advanced CNC machines offer real-time compensation, adjusting toolpaths based on sensor feedback to ensure accuracy even with minor deformation.
Vibration Damping and Structural Support
- Damping Technologies: Tuned mass dampers or active damping systems reduce vibration, improving precision and surface finish.
- Temporary Supports: Structural braces stabilize thin walls during machining.
Surface Finish Considerations
Achieving proper surface finish is challenging for thin-wall parts.
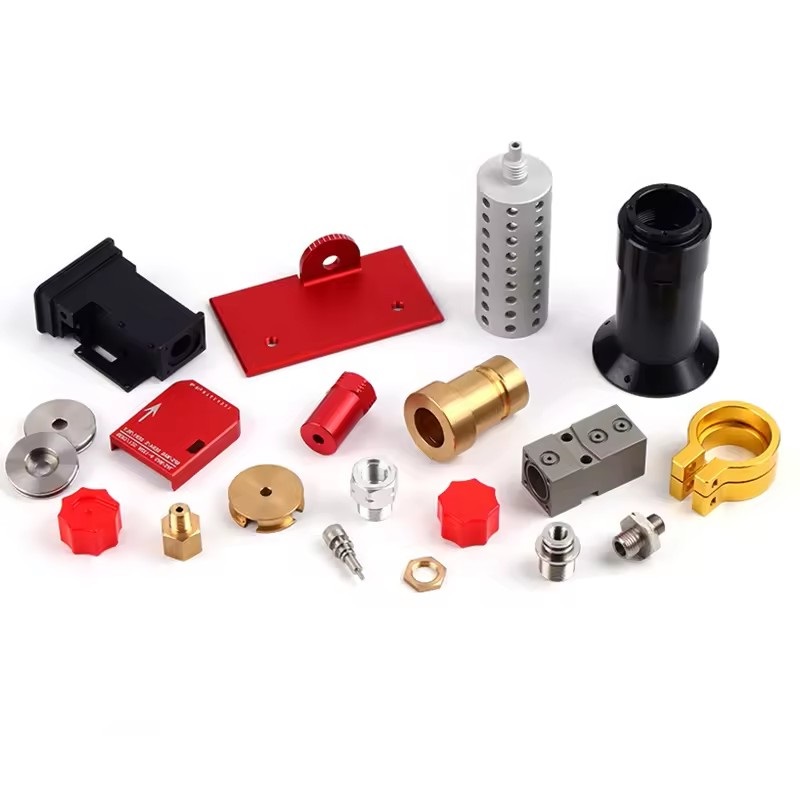
Achieving High-Quality Surface Finish:
- Sharp Tools: Reduce tool pressure and improve surface quality.
- Finishing Paths: Light finishing passes minimize surface defects.
- Controlled Speeds/Feeds: Balanced parameters prevent over-machining.
Advanced Metrology for Thin-Wall Parts
Accurate measurement ensures thin-wall parts meet tight tolerances.
Precision Measurement Techniques:
Technique | Advantages |
---|---|
CMM (Coordinate Measuring Machine) | High precision; suitable for complex geometries |
Laser Scanning | Fast, accurate; ideal for thin-wall components |
Both techniques enable precise measurement, detecting deformation and ensuring compliance with tolerances.
Leveraging High-Speed Cutting and Thermal Management
High-speed cutting poses challenges in tool wear and heat management.
Managing Tool Wear and Heat in HSM:
- Coolant: Prevent overheating.
- Optimize Cutting Speeds: Balance speed and feed to minimize heat.
- Tool Materials: Carbide and diamond-coated tools resist wear at high speeds.
Digital Twins and AI for Process Optimization
Digital technologies are transforming CNC machining with precise simulations and intelligent toolpaths.
Simulating Thin-Wall Machining with Digital Twins
Digital twins allow pre-production simulation, predicting issues like deformation or tool wear for proactive adjustments.
AI-Enhanced Machining
AI analyzes real-time data to optimize toolpaths, reduce errors, and adjust parameters automatically, ensuring consistent quality.
Post-Machining Stress Relief and Heat Treatment
Thin-wall parts may retain internal stress, causing deformation over time.
Stress-Relief Techniques:
- Heat Treatment: Apply controlled heat to relieve internal stress.
- Vibratory Stress Relief: Use vibration to redistribute stress without heating.
For more information, contact Debaolong Seiko. You are also welcome to upload your designs to Debaolong Seiko for a quote.