In precision design, every aspect of the design deserves attention. Details such as the selection of screws and bolts can be critical. The right thread type will better suit the screw’s purpose. Let’s explore the topic of coarse threads versus fine threads.
Design Features of Coarse and Fine Threads
Coarse and fine threads play different roles based on properties like tensile strength, shear strength, holding power, clamping strength, and base materials. For designers and engineers, this choice is vital in applications involving human health and safety. For example, in automotive applications, bolts must never fail during operation. Therefore, caution should be exercised when selecting the correct type of screw or bolt.
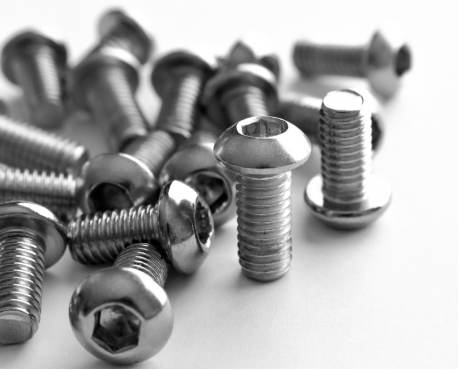
Coarse Thread Design Features
- Pitch: Coarse threads have a larger pitch.
- Profile: They are typically conical.
- Common Uses: Thin-gauge metal sheets, wood, or plastic.
Fine Thread Design Features
- Pitch: Fine threads have a smaller pitch.
- Profile: They can be round, conical, or trapezoidal, depending on relevant standards.
- Common Uses: Precision fastening applications such as the aerospace industry.
Aspect | Coarse Threads | Fine Threads |
---|---|---|
Bolt Pitch | Larger | Smaller |
Shear Strength | Higher | Lower |
Tensile Strength | Lower | Higher |
Resistance to Loosening | More resistant to vibration | Prone to loosening over time |
Installation Speed | Faster | Slower |
Material Suitability | Soft materials (wood, plastic) | Hard materials (metal) |
Holding Power | Less metal engagement | Stronger grip on metal |
Common Applications | Construction, etc. | Automotive, aerospace, etc. |
How to Design Threads?
Screw manufacturers adhere to international standards such as ISO, UNC, ASME, and BSW to produce standardized screws and bolts. There are also other factors to consider:
Determine Load Requirements
The selected screw diameter should meet the strength requirements of relevant standards.
Choose the Right Thread Standard
Standardization ensures easy replacement of screws and bolts. Universally accepted standards should be used.
How to Select Materials
When choosing materials for screws and bolts, corrosion resistance and ultimate tensile strength requirements must be considered.
Select Processing Technology
Manufacturers should consider capital investment, tolerances, and production volume requirements to select appropriate processing techniques.
Coarse Threads vs. Fine Threads: 4 Key Differences
1. Pitch: Larger vs. Smaller
Coarse threads have fewer threads per unit length, so their pitch is larger. Fine threads are the opposite.
2. Strength: Better Load-Bearing vs. Better Tensile Capacity
Coarse threads have good adhesion or clamping properties and higher shear strength. Fine threads, with their relatively larger outer diameter and shallower thread depth, offer better tensile strength.
3. Vibration Resistance: Better Resistance, Less Likely to Loosen
Coarse threads tend to grip the base material tightly, while fine threads gradually loosen. For example, coarse-thread EPDM screws are often used to fasten roof panels in pre-engineered buildings (PEB). They keep roof panels securely attached to the frame for years.
4. Manufacturing: Easier to Produce vs. Higher Precision Required
Coarse-thread screws generally do not require high precision due to their larger pitch and versatility. In contrast, fine-thread screws and bolts are used in high-precision applications such as automotive and aerospace. They are considered more difficult to manufacture and require rigorous quality assurance/quality control.
How Does Pitch Affect Thread Engagement and Strength?
The optimal pitch is essential for optimal fastening. It depends entirely on the intended use. Some situations require precise assembly, while others need a tight fit. The bolt or screw design should accommodate this.
Coarse Thread Pitch and Load Distribution
A coarse pitch is used in applications requiring greater clamping force. In applications like wooden components, coarse threads clamp more tightly and can also withstand higher shear stress.
Fine Pitch and Precision Engagement
A fine pitch ensures high-precision mechanical fastening. Fine-thread bolts tighten only in the correct position, and low tolerances ensure minimal clearance between components.
Optimizing Pitch for Specific Load and Stress Requirements
Although research and development are always essential for product optimization, certain standardized designs exist. Standards should be checked to find the right pitch for a specific application.
Coarse vs. Fine Threads: Choosing for Your Custom Parts
For custom components, the choice between coarse and fine thread designs is critical. Mechanical fastener design often receives little attention but should be regarded as a vital aspect of component assembly. Proper research and development are essential to finding the right thread design for a specific application.
For Heavy-Duty and High-Torque Applications
Coarse-thread screws are usually preferred for heavy-duty applications such as structural assembly and construction due to their high shear strength, faster assembly speed, and high resistance to chipping and wear. For example, coarse-thread EPDM screws are used to fasten roof panels in pre-engineered buildings (PEB), keeping them securely attached to the frame for years.
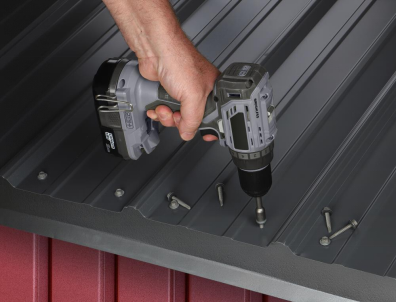
For Finely Tuned Components
Fine-thread screws and bolts are preferred for precision parts (e.g., aerospace components) due to their higher accuracy and better performance under tensile loads. For example, fine-thread rivets tightened along aircraft fuselages ensure secure and precise fastening.
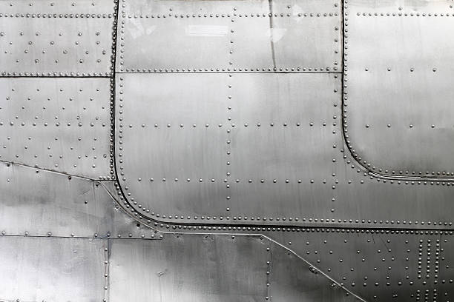
Examples: Coarse vs. Fine Thread Bolts
EPDM coarse-thread bolts are suitable for tough jobs like construction, while M10 x 1.0 fine-thread bolts may be used in higher-precision engineering applications. In practice, the choice between fine and coarse threads depends on the application.
- What Are the Uses of Coarse and Fine Thread Bolts?
Coarse threads are preferred for high shear stress environments, while fine threads are ideal for high-precision and high axial load environments. - Which Type of Bolt Should Be Used in High-Stress Situations?
Fine-thread bolts should be used in high-stress situations as they can withstand higher tensile loads.
Manufacturing Processes for Coarse and Fine Threads: From Design to Final Product
Bolt manufacturing starts with a rod-shaped base material, which may undergo multiple steps such as rolling, heat treatment, and milling to achieve the required precision and strength. Design, dimensions, tolerances, and material properties are all regulated by relevant standards.
CNC Machining of Coarse and Fine Threads
Lathes and CNC thread milling machines are used to machine threads on ordinary rods. CNC machines follow a set of predefined instructions from CAD and CAM to process the rod. Coarse threads are machined faster than fine threads.
Thread Cutting and Rolling Techniques for Parts
- Thread Cutting: Uses lathes, taps, or dies for small-batch or custom threads.
- Thread Rolling: Cold-forming threads for higher strength and mass production.
Materials for Coarse vs. Fine Thread Manufacturing Processes
Material selection depends on factors such as machinability, cost, durability, corrosion resistance, and dimensional stability.
Coarse Threads: Lower Precision Requirements
- Mild Steel (A36, SAE 1018): The most common base material, cost-effective, strong, heat-treatable, and readily available. Used in mechanical fittings and shipbuilding.
- Aluminum (6061, 7075): Offers a good strength-to-weight ratio, suitable for lightweight applications like aircraft fasteners.
- Brass (C36000): Has good machinability, excellent aesthetics, and is non-magnetic with high corrosion resistance. Used in electrical systems, marine applications, woodworking, plumbing, HVAC, musical instruments, decorative fittings, and automotive restoration.
Fine Threads: Higher Precision Requirements
- Stainless Steel (304, 316, 17-4 PH): Relatively affordable yet highly corrosion-resistant, suitable for high-strength applications, from children’s toys to nuclear reactors.
- Titanium (Grade 5 – Ti-6Al-4V): Boasts an excellent strength-to-weight ratio, ideal for aerospace and biomedical applications.
- Alloy Steels (4140, 4340, 8620): Used in various critical conditions requiring resistance to fatigue and high temperatures, such as wind turbines and furnaces.
Manufacturing Challenges for Coarse and Fine Threads
Maintaining thread machining quality is a tedious task. Common quality issues in thread processing include insufficient precision, burr formation, thread wear, uneven performance, and excessive friction. Addressing these issues will improve the quality of coarse and fine thread bolts.
Common Thread Production Problems and Solutions
Challenge | Impact | Remedies |
---|---|---|
Thread Precision | Poor fit, loose fastening | Precision CNC machining, tool calibration |
Material Hardness | Tool wear, high costs | Carbide tools, use of coolants |
Burr Formation | Impaired assembly | Deburring tools and thread rolling dies |
Tool Wear and Breakage | Reduced quality, increased downtime | Use of coated tools |
Thread Wear | Seizing and thread damage | Lubrication, coatings |
Surface Finish Issues | Poor fit, high friction | Proper feed rates, finishing passes |
Heat Generation | Altered material properties, shortened tool life | Use of coolants, optimized speed |
Thread Rolling Defects | Weak threads, failure | Control of rolling pressure |
Impact of Thread Precision on Manufacturing Costs
Manufacturing costs increase with the required level of precision. High precision demands strict quality control, leading to higher scrap rates and waste. Additionally, extra steps such as deburring, surface improvement, lubrication, and heat treatment may be required. High-precision equipment results in higher capital expenditure.
Quality Control and Tolerance Management for Threaded Parts
For threaded components like bolts and screws, quality control procedures should be clearly defined according to relevant standards. Manufacturers should establish standard operating procedures (SOPs) for quality control. Any components failing to meet quality specifications should be rejected, and feedback should be provided to the manufacturing team to prevent future errors.
Advantages of Coarse and Fine Threads in Specific Applications
The choice between fine and coarse threads depends on the specific application. Fine threads cannot fully replace coarse threads, and vice versa. Engineers and designers carefully consider thread design criteria and other bolt properties based on the bolt’s intended use.
Coarse Threads in Automotive Engine Components
Coarse thread designs overcome vibration loads in automobiles and are less likely to loosen. They better withstand multi-axial loads.
Fine Threads in Aerospace Fasteners
Fine thread designs offer high precision, essential for critical applications like aerospace. Their smooth, fine-thread design takes up less space and provides better load distribution from an aerodynamic perspective.
Coarse Threads in Heavy Equipment and Machinery
Coarse thread designs speed up assembly and disassembly of heavy equipment and machinery. They are less susceptible to damage and deformation from dirt and are easy to replace.
Fine Threads in Precision Medical Devices
Medical equipment requires extreme care to achieve high precision. These devices are designed so that loads are distributed more effectively through fine thread designs.
Disadvantages of Coarse and Fine Threads in Specific Applications
Using incorrect specifications can have fatal consequences. For example, even a small component failure like a screw can severely harm people’s health and safety on an aircraft, resulting in huge economic losses. Widely accepted standards should be referenced when selecting mechanical fasteners.
Coarse Threads in Aerospace Structural Components
Coarse thread designs lack the precision required for critical applications like aerospace and have poor pressure management capabilities. For instance, under increased pressure, coarse-thread bolts of similar size fail earlier than fine-thread bolts. Larger coarse-thread bolts might withstand such loads but may not fit other design requirements.
Fine Threads in High-Torque Automotive Applications
Fine thread designs are generally not considered suitable for high-torque and multi-axial load environments and are prone to loosening under vibration loads.
Conclusion
Both coarse and fine threads are suitable for a unique set of applications. From a design perspective, a clear choice must be made between them. Using the wrong thread design can lead to economic losses and personal injury. Coarse threads are valued for their clamping force, ease of assembly, low cost, and high shear load-bearing capacity. Fine threads, on the other hand, offer high precision, high tensile strength, and relatively light weight.
For more information, please contact Debaolong Seiko. You are also welcome to upload your designs to Debaolong Seiko for a quotation.