17-4 PH stainless steel is a metallic material with various properties that make it a preferred choice for high-temperature applications. Key characteristics of this alloy include excellent formability, weldability, and corrosion resistance. Additionally, its properties can be modified through different heat treatment processes. This article focuses on eight distinct heat treatment methods for 17-4 PH stainless steel, which can alter its properties to meet specific application requirements.
Understanding 17-4 PH Stainless Steel
Before delving into heat treatment processes, it is crucial to understand the material’s properties, which are discussed below:
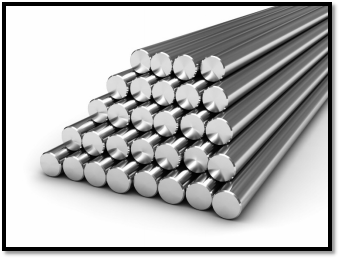
Precipitation Hardening Mechanism
The goal of this process is to enhance the mechanical properties of 17-4 PH SS, particularly strength and hardness. To achieve this, the material undergoes two main steps:
- Solution Treatment: The alloy is heated to approximately 1025°C, held for one hour, and then rapidly water-quenched or air-cooled to ensure uniform distribution of elements within the material.
- Aging: The alloy is reheated to a temperature between 480–620°C for a specified soaking time, forming copper-rich precipitates that impede dislocations, thereby enhancing the material’s mechanical properties.
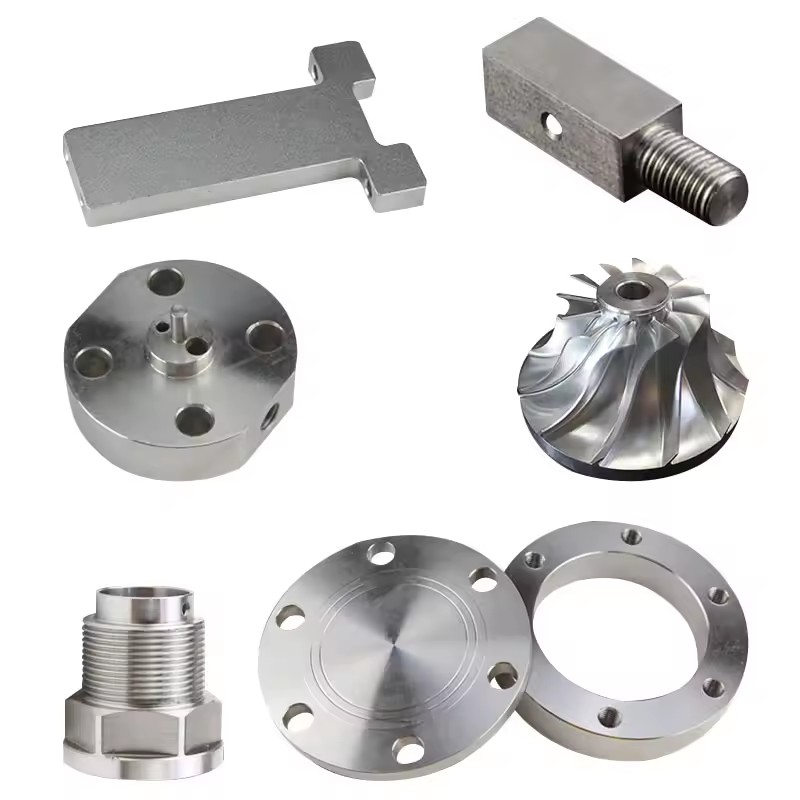
Chemical Composition
Element | Composition (%) |
---|---|
C | 0.07 |
Si | 1.00 |
Mn | 1.00 |
P | 0.040 |
S | 0.030 |
Cr | 15.00–17.50 |
Ni | 3.00–5.00 |
Cu | 3.00–5.00 |
Nb | 0.15–0.45 |
Is 17-7 PH Stainless Steel Magnetic?
17-7 PH stainless steel is magnetic. This property is acquired when the material undergoes heat treatment that promotes the formation of a martensitic structure, making it suitable for applications requiring magnetism.
Density
The approximate density of 17-4 PH SS is 7.75 g/cm³, making it suitable for applications demanding durability and high strength.
17-4 PH Hardness
Hardness strictly depends on the specific heat treatment the material undergoes, ranging from 28–44 HRC.
Yield Strength
The alloy has a yield strength of 1030 MPa in the solution-treated condition, but this changes significantly after precipitation hardening.
Mechanical Properties of 17-4 PH Stainless Steel
Condition | Ultimate Tensile Strength (PSI) | 0.2% Yield Strength (PSI) | Elongation (2 in, %) | Reduction of Area (%) | Brinell Hardness | Rockwell Hardness |
---|---|---|---|---|---|---|
A | <185,000 | <160,000 | 5 | 30 | <353 | <C38 |
H900 | 190,000 | 170,000 | 10 | 40 | 388 | C40–48 |
H925 | 170,000 | 155,000 | 10 | 40 | 390 | C38–46 |
H1025 | 155,000 | 145,000 | 12 | 45 | 331 | C35–43 |
H1075 | 145,000 | 125,000 | 13 | 45 | 311 | C32–40 |
H1150 | 135,000 | 105,000 | 16 | 50 | 277 | C28–38 |
H1150-M | 115,000 | 75,000 | 18 | 55 | 255 | C24–32 |
H1150-D | 125,000 | 105,000 | 16 | 50 | 275 | C24–33 |
Machinability of 17-4 Stainless Steel
The alloy has good machinability in the solution-treated condition, but this typically decreases after precipitation hardening. However, advanced machining techniques can maintain processability.
17-4 PH Stainless Steel Equivalents
Due to its properties (hardness, strength, corrosion resistance), the alloy is ideal for demanding applications. Its equivalents under certain conditions include:
- AMS 5643
- DIN 1.4542
- AISI 630
- EN 1.4542 / X5CrNiCuNb16-4
- ASTM A564
- JIS SUS630
17-4 Heat Treatment Chart
Condition | Hardening Temperature (°C) | Time (Hours) | Cooling Process |
---|---|---|---|
Condition A | 1038±12 | 0.5 | Oil, water, air |
H900 | 482 | 1 | Air |
H925 | 496 | 4 | Air |
H1025 | 552 | 4 | Air |
H1075 | 579 | 4 | Air |
H1100 | 593 | 4 | Air |
H1150 | 621 | 4 | Air |
Type 1150-D | 621 | 4 | Air |
H1150-M | 760 | 2 | Air |
How to Heat Treat 17-4 PH Stainless Steel
Process | Details |
---|---|
Solution Treatment | – Heat the alloy to 1025°C (1875°F), hold for one hour, then cool rapidly. |
Aging | – Reheat to a lower temperature, typically 480°C (900°F) to 620°C (1150°F). |
– Hold for a specified time (usually ~4 hours), then air-cool. | |
Precipitation Hardening | – Heat to varying temperatures and hold for specific times to form copper-rich precipitates, enhancing properties. |
Advantages and Disadvantages of 17-4 PH Stainless Steel
Advantages | Disadvantages |
---|---|
High strength and hardness | Susceptibility to stress corrosion cracking |
Versatile heat treatment | Sensitivity to heat treatment |
Good machinability | Work hardening |
Weldability | Cost |
High impact toughness | Limited high-temperature performance |
Dimensional stability issues |
Condition A (Annealing): The Foundation for Further Heat Treatment
Purpose of Annealing
This is the first step in heat treatment and processing of material components. It is critical as it eliminates internal stresses, softens the alloy for easier machining and handling, and forms a fine-grained microstructure, ensuring uniform material properties for high-precision machining and forming.
Process Steps
- Heat the alloy to 1040–1065°C to dissolve alloying elements into a solid solution, ensuring a uniform microstructure.
- Soak for 30–60 minutes to ensure element uniformity.
- Cool slowly in the furnace or at room temperature.
Resulting Properties
- Improved ductility
- Enhanced machinability
- Lower strength and hardness
- Uniform microstructure
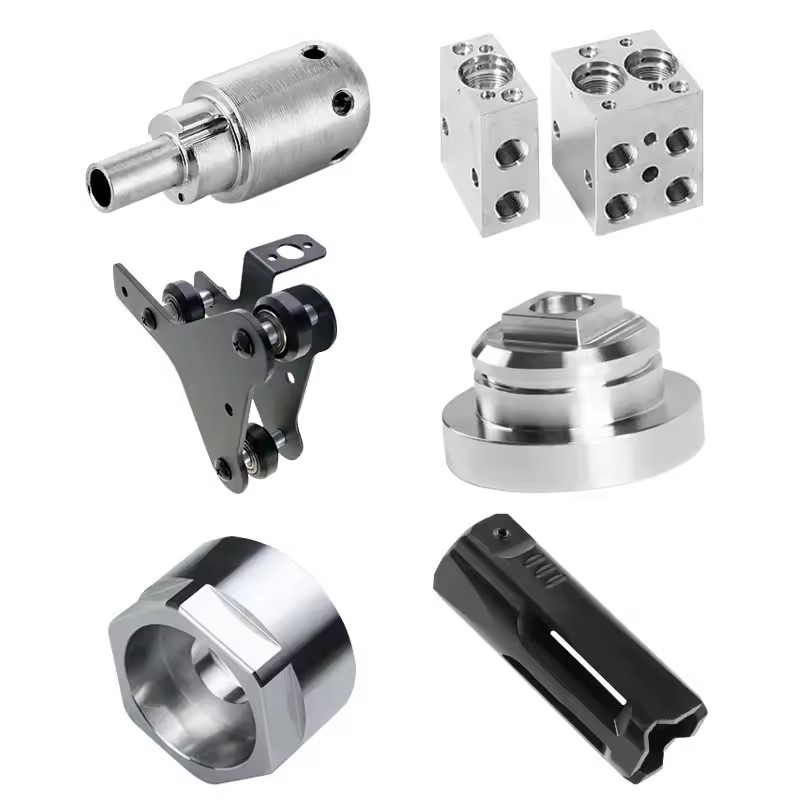
Condition H900: Maximizing Strength and Hardness
Purpose of H900 Treatment
This treatment forms copper-rich precipitates in the microstructure, impeding dislocation movement. It maximizes the mechanical properties of 17-4 PH stainless steel in terms of strength and hardness, making it suitable for applications requiring high tensile and yield performance.
Process Steps
- Heat the alloy to 482°C to form copper-rich precipitates without damaging the alloy structure.
- Soak for 4 hours to ensure uniform precipitate distribution.
- Control air cooling to retain precipitates and stabilize properties.
Resulting Properties
- Tensile strength increased to 1450 MPa
- Yield strength increased to 1400 MPa
- Higher hardness
- Slightly reduced ductility
Condition H1150: Balancing Strength and Toughness
Purpose of H1150 Treatment
Alloys treated with H1150 achieve a balance between strength and toughness, suitable for applications requiring enhanced properties and high impact resistance. They can withstand impact and cyclic loads while maintaining mechanical integrity.
Process Steps
- Heat the alloy to 621°C to promote precipitate formation.
- Soak for 4 hours to optimize precipitate formation.
- Air-cool at room temperature to stabilize precipitates and retain mechanical properties.
Resulting Properties
- High tensile strength (1210 MPa) – slightly lower than H900
- Improved yield strength (1070 MPa)
- Enhanced toughness
- Balanced performance
Condition H1025: Optimizing Corrosion Resistance
Purpose of H1025 Treatment
This treatment enhances the corrosion resistance of 17-4 PH SS alongside other strengthened properties, making alloy components suitable for high-corrosion environments such as marine, chemical, and aerospace applications.
Process Steps
- Heat the alloy to 552°C to form copper-rich precipitates.
- Soak at 552°C for 4 hours to optimize precipitate formation.
- Air-cool at room temperature to stabilize precipitates and retain mechanical properties.
Resulting Properties
- High tensile and yield strength
- Improved corrosion resistance
Condition H1075: Enhancing Toughness and Ductility
Purpose of H1075 Treatment
This heat treatment modifies the toughness and ductility of 17-4 PH stainless steel components, customizing them for applications requiring high impact resistance and formability. Treated components can withstand dynamic forces and deformation.
Process Steps
- Heat the alloy to 579°C to balance toughness and strengthened properties.
- Hold at 579°C for 4 hours to form optimal precipitates.
- Air-cool at room temperature to stabilize properties.
Resulting Properties
- Increased toughness
- Enhanced ductility
- Good strength
- Balanced properties
Condition H1100: Achieving High Strength and Moderate Toughness
Purpose of H1100 Treatment
H1100 treatment provides 17-4 PH stainless steel alloy components with high strength and moderate toughness, enabling them to withstand significant loads and deformation. It is suitable for applications requiring high mechanical performance without severe impact exposure.
Process Steps
- Heat the alloy to 593°C (higher temperature).
- Hold at 593°C for 4 hours to induce necessary changes for desired properties.
- Air-cool at room temperature to retain properties.
Resulting Properties
- High tensile strength
- Moderate yield strength
- Good toughness
- Versatile performance
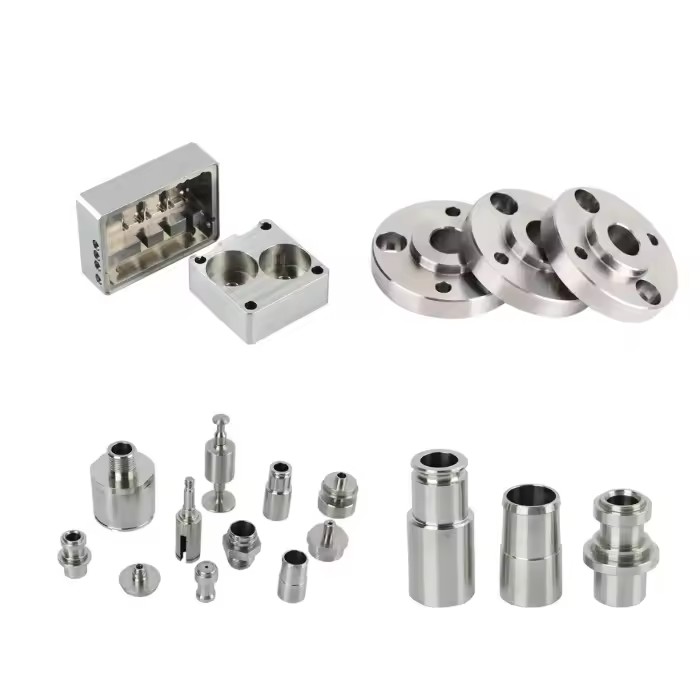
Conditions H1125 and H925: Maximizing Toughness and Custom Properties
Purpose of H1125 and H925 Treatments
- H1125: Maximizes toughness to withstand impact forces and high stress, resisting cracking in harsh conditions.
- H925: Balances properties such as hardness, strength, and toughness, enabling components to suit a wide range of engineering applications.
Process Steps
H1125 Steps | H925 Steps |
---|---|
Heat material to 607°C to optimize precipitates. | Heat material to 496°C. |
Hold for 4 hours to form and distribute precipitates. | Hold for 4 hours to form a microstructure with intermediate properties. |
Air-cool to room temperature. | Air-cool to achieve balanced properties. |
Resulting Properties
- H1125:
- Excellent toughness
- Improved ductility
- Good strength
- H925:
- Balanced strength and hardness
- Moderate toughness
- Versatility
Risks of Improper Heat Treatment for 17-4 PH
Improper heat treatment can cause significant microstructural changes, leading to undesirable properties. Potential risks include:
- Under-aging
- Over-aging
- Distortion
- Cracking
Best Methods to Prevent 17-4 PH Stainless Steel from Rusting
- Proper heat treatment
- Surface protection
- Passivation
- Environmental control
- Regular inspection and maintenance
- Proper design and manufacturing
- Using high-quality stainless steel
Choosing the Right Heat Treatment: Matching Properties to Applications
The table below analyzes properties achieved through specific heat treatments, helping you select the most suitable 17-4 PH SS treatment for your application:
HT Condition | Tensile Strength (MPa) | Yield Strength (MPa) | Elongation | Rockwell C Hardness |
---|---|---|---|---|
Condition A | 1172 | 1034 | 5 | 30 |
H900 | 1379 | 1241 | 10 | 36 |
H925 | 1310 | 1172 | 10 | 36 |
H1025 | 1180 | 1034 | 12 | 34 |
H1075 | 1103 | 896 | 14 | 32 |
H1100 | 1000 | 827 | 16 | 30 |
H1150 | 862 | 724 | 18 | 28 |
H1150-M | 862 | 724 | 18 | 28 |
Frequently Asked Questions
17-7 PH Stainless Steel vs. 304
17-7 PH contains 17% chromium and 7% nickel, offering good corrosion resistance and excellent fatigue life. In contrast, 304 contains 18% chromium and 8% nickel, providing better ductility and weldability.
17-7 PH Stainless Steel vs. 316
17-7 PH (17% Cr, 7% Ni) offers good corrosion resistance and significant fatigue life, while 316 (16% Cr, 10% Ni, 2% Mo) is suitable for chloride-rich environments.
13-8 PH, 15-5 PH, and 17-4 PH Stainless Steel
- 13-8 PH (13% Cr, 8% Ni): Good strength and toughness.
- 15-5 PH (15% Cr, 5% Ni): Balances strength and toughness.
- 17-4 PH SS (17% Cr, 4% Ni): Combines high strength and good corrosion resistance.
For more information, please contact Debaolong Seiko. You are also welcome to upload your designs to Debaolong Seiko for a quotation.