01 ViliaSprint²
PERI 3D, a construction 3D printing contractor, and Holcim, a concrete materials company, have launched France’s first on-site 3D-printed multi-family building, which is the largest of its kind in Europe. The new ViliaSprint² project is currently underway in Bezannes. As part of a social housing initiative, this building represents a major trend in construction additive manufacturing.
Built using COBOD’s BOD2 construction 3D printer, ViliaSprint² demonstrates that 3D concrete printing is no longer a speculative experiment but a tangible architectural reality. Together with Plurial Novilia, the project introduces an epoch-making transformation in public housing manufacturing.
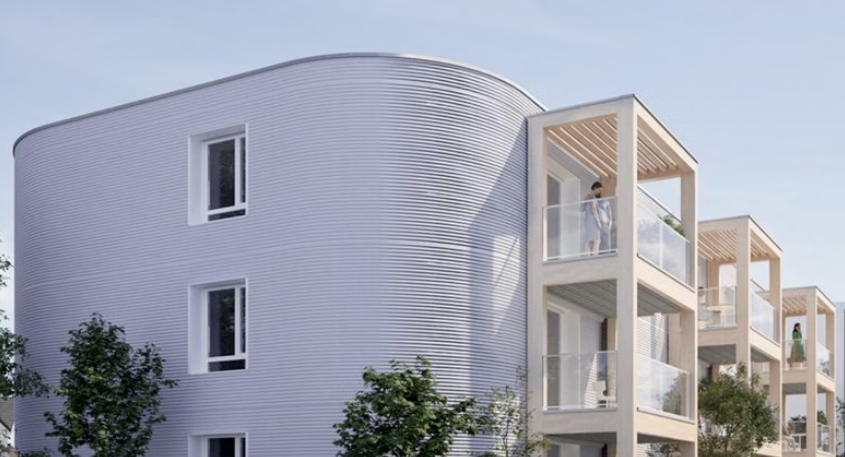
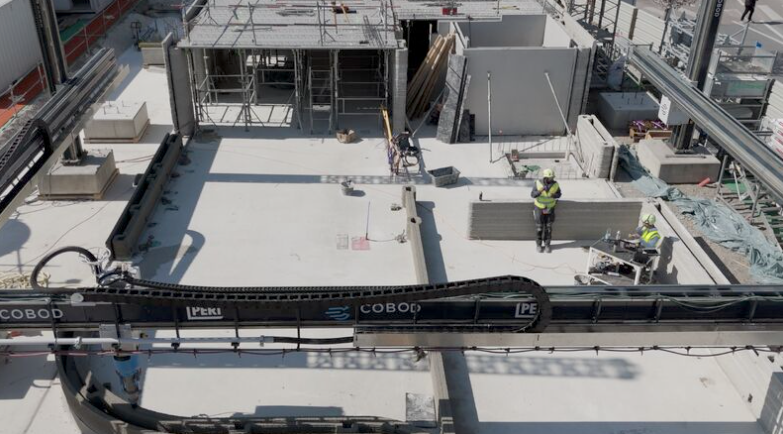
02 Next Starbucks
Starbucks will open its first 3D-printed store in the United States, a project collaborated on by Starbucks, PERI 3D Construction, and COBOD International. Germany-based PERI, known for its work in 3D-printed construction, utilized COBOD’s BOD2 gantry printer. COBOD, headquartered in Denmark, is a leader in the field of construction 3D printing with a significant share of the global market. The three partners have joined forces to apply faster and more sustainable construction methods.
The textured concrete walls with a layered appearance give the building a unique 3D-printed feel. The layout includes a shaded drive-thru lane and an elevator-free window, designed for customers seeking speed and convenience. The restaurant has no indoor seating, reflecting the growing trend of dining outside restaurants and quick pickups.
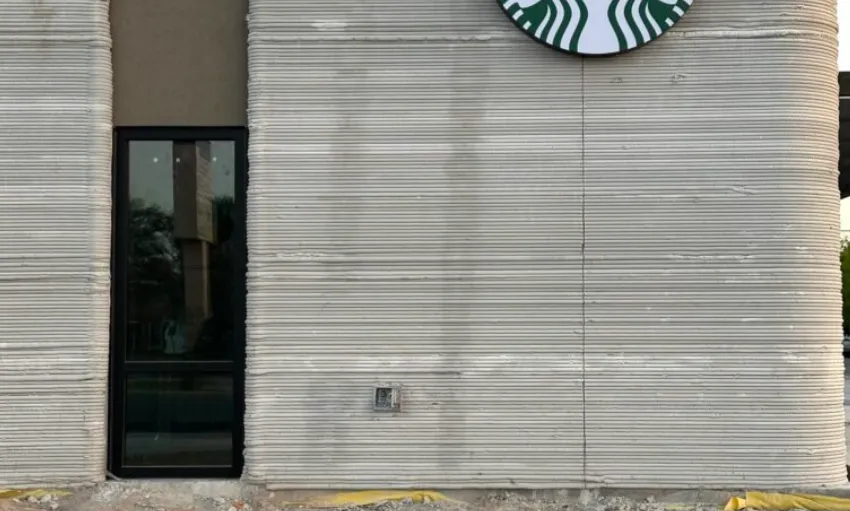
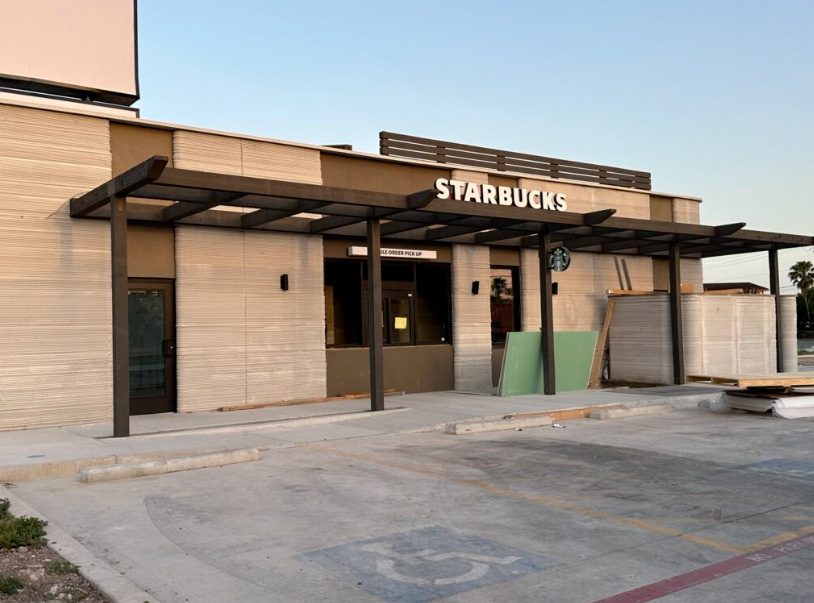
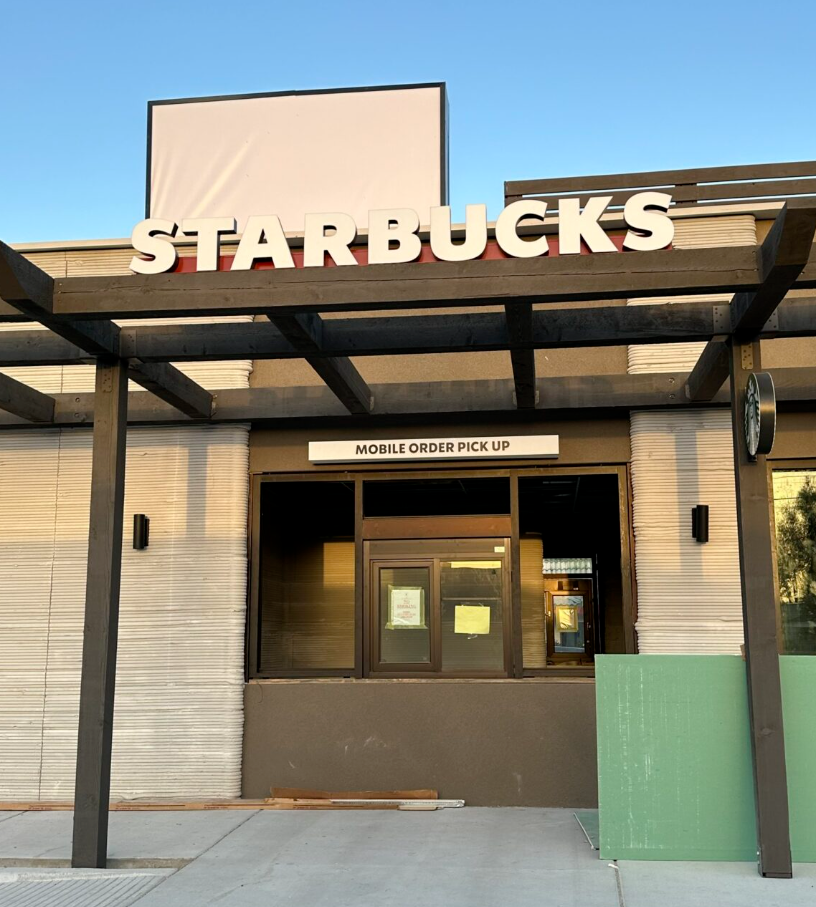
03 WASP
WASP, in collaboration with Aki Hamada Architects, designed a series of 3D-printed structures for the 2025 World Expo in Osaka, Japan. Using the Crane WASP, 20 toilet facilities, as well as walls, flower pots, structures around the toilets, and small stages, were 3D-printed. This is a continuation of WASP’s series of Expo-related buildings and residences, including self-sufficient homes, another eco-friendly house (part of the Milan Triennale), and structures in Colombia. While there are many construction 3D printing companies, WASP’s core mission is to save the world. The team invests heavily in geopolymers and materials beyond concrete or polymers. This focus on sustainability gives it an advantage with non-governmental organizations, eco-friendly brands, architects, and governments.
Components were manufactured centrally rather than printed on-site. 56 panels, 4 flower pots, 45 bricks, and handwash basin bases combined with ceramic units were 3D-printed. The panels, with dimensions of 93cm x 30cm and 120cm in height, are connected to wooden walls. Each flower pot, an impressive structure with a circumference of 6.2 meters and a height of 1.7 meters, serves as part of the seating area and a flower container. For the blocks, bamboo poles are used as green reinforcement to strengthen the structure.
Soil is mixed with seaweed as a binder, along with straw and clay. The structure is biodegradable, and the printed objects themselves are hardened with magnesium oxide. The entire structure was 3D-printed indoors and then installed on-site.
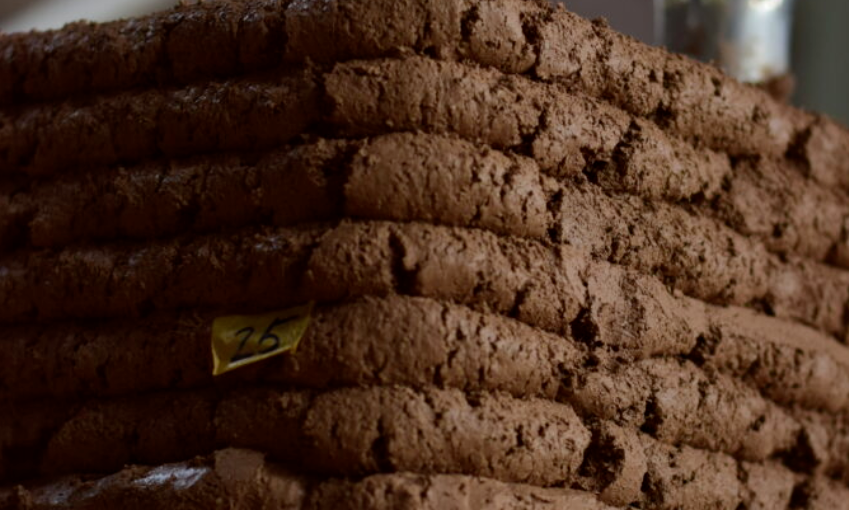
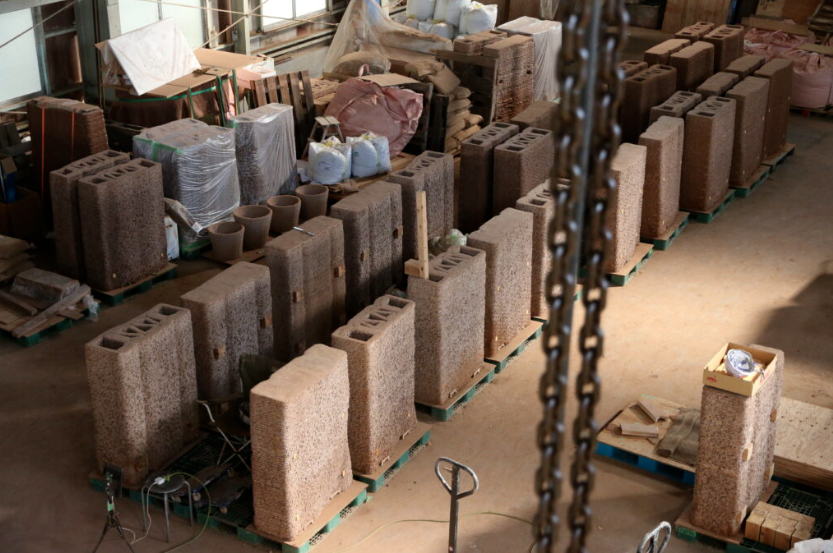
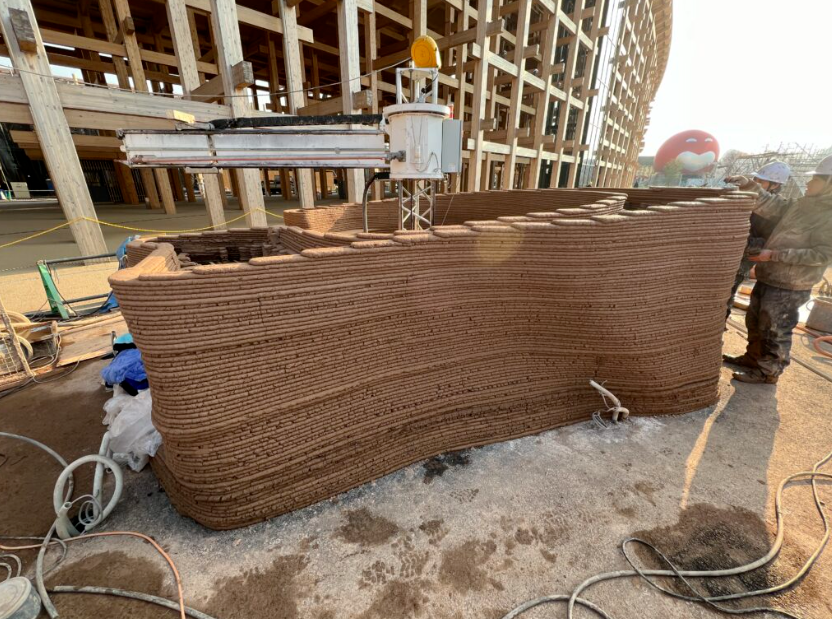
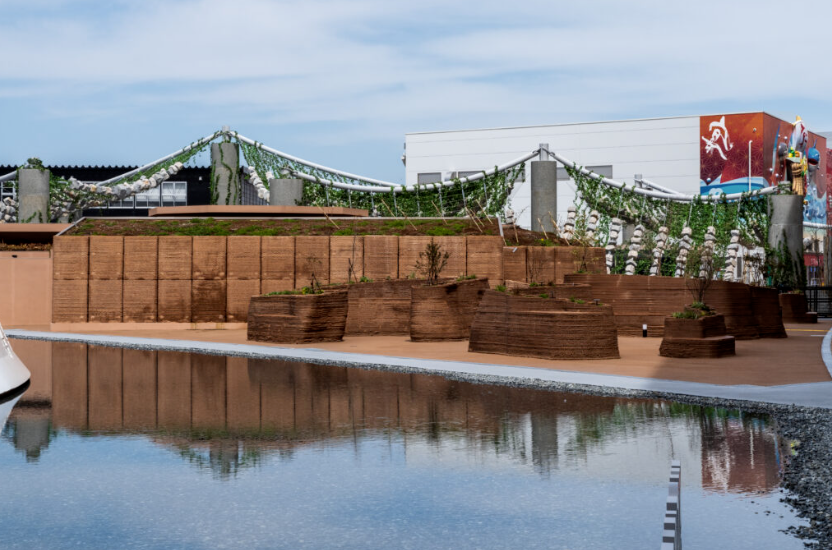
04 Canyon Club
A planned luxury residential resort community, covering 60 acres, is located on the waterfront of Lake Travis in the Texas Hill Country. The development will include 25 residences, 20 of which will be traditionally constructed, and 5 will be 3D-printed vacation buildings.
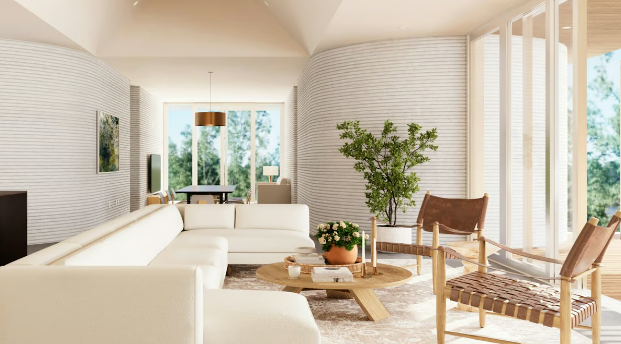
05 Aevum
At the 2025 international “Crei-action” exhibition held at the University of Milan, London-based architectural firm Zaha Hadid Architects (ZHA) and Dutch 3D concrete printing expert Vertico showcased Aevum, a collaborative installation exploring the intersection of historical stone carving and robotic concrete 3D printing.
“Aevum”, meaning “eternity” in Latin, consists of two 6-meter by 6-meter offset arches. One arch is carved from solid marble; the other is created using Vertico’s large-scale 3D concrete printing system. The 3D-printed arch is composed of 21 unique elements, standing 5.6 meters tall and weighing 5.5 tons, with a printing time exceeding 6 days. The installation was completed within 7 days, with structural and manufacturing support from Carpenterie Pezzetti and Eckersley O’Callaghan.
The printed structure was manufactured using Vertico’s accelerator print head mounted on a robotic rail platform. A custom Sika cement mixture enabled the production of the non-planar geometries and large cantilevers required by ZHA’s design. The printing process prioritized design accuracy within a compressed timeframe.
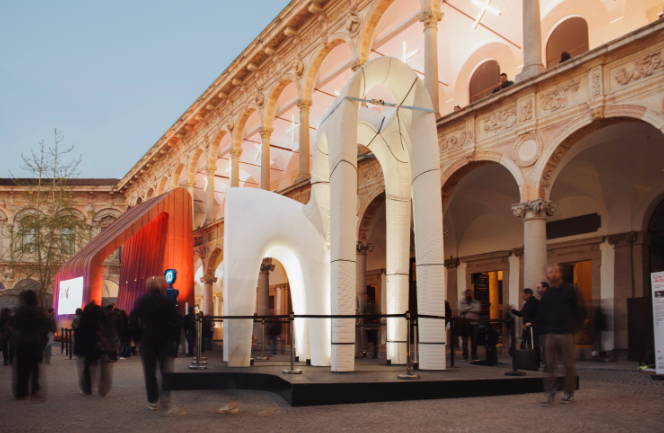
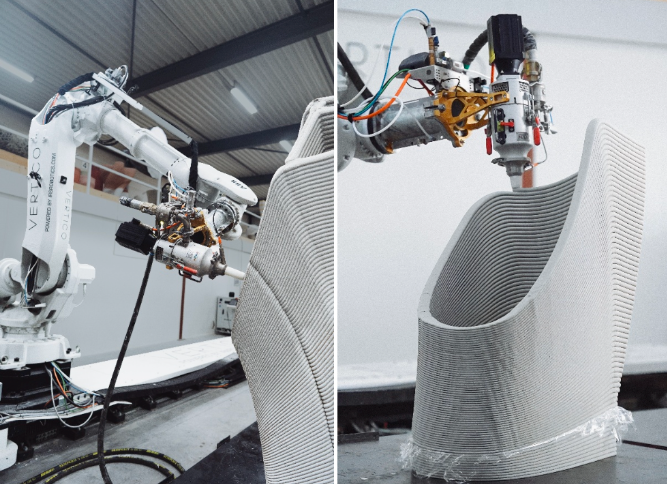
For more information, please contact Debaolong Seiko. You are also welcome to upload your designs to Debaolong Seiko for a quote.