Less than a year ago, retail giant Walmart announced the commissioning of one of the largest freestanding 3D-printed commercial buildings in the United States. The Tennessee-based structure, an 8,000-square-foot expansion of an existing store, is now operational as an online pickup center. Now, clearly satisfied with this first major foray into 3D-printed construction, Walmart is set to open a second 3D-printed expansion project in Huntsville, Alabama.
The new building is scheduled to open this Friday (May 9th) at Walmart Supercenter #5197, covering 5,000 square feet and serving as an online grocery pickup and delivery hub. Similar to Walmart’s first 3D-printed construction project, this development is led by Colorado-based 3D construction printing company Alquist 3D LLC, in collaboration with FMGI, a commercial real estate specialist general contractor.
Notably, the 3D-printed walls of the new expansion were completed in 75 hours over 7 days, representing a significant compression compared to the three-plus weeks required by traditional cement masonry techniques. Additionally, the construction process required far fewer workers than traditional methods: the Alquist and FMGI Huntsville teams deployed a five-person crew, using two construction 3D printing robots to build 16-foot-tall walls layer by layer with a special concrete mixture developed by Sika USA.
“In the commercial construction sector, where project timelines and costs are highly valued, our partnership with Walmart demonstrates that 3D printing is not just an innovative technology—it’s a mature solution scalable for industries like retail,” said Patrick Callahan, CEO of Alquist 3D. “This second project clearly shows how retail expansions can be faster, more cost-effective, and less wasteful, paving the way for broader adoption of the technology in large-scale commercial buildings.”
Another key advantage of 3D construction printing is its ability to continue operations in weather conditions that might hinder traditional construction. In fact, this feature allowed the team to complete the wall construction ahead of schedule. Callahan added, “The adaptability of the technology and materials proves that 3D construction printing (3DCP) is a preferred commercial building solution for variable climate conditions.”
Efficiency gains are also evident in other aspects, particularly material consumption. According to Alquist 3D, 3D printing technology enabled the team to reduce material waste by 55%, using only 75% of the materials supplied by Sika. Furthermore, the robotic construction site eliminated the need for high-risk facilities like scaffolding, providing a safer environment for workers.
LB Johnson, Walmart’s Vice President of Construction, spoke about the second project: “These 3DCP tests aim to evaluate alternatives to traditional construction methods while maximizing sustainability. Our innovation strategy focuses on optimizing processes and simplifying on-site operations—to reduce project costs and timelines. This will accelerate our market response to serve customers and drive the evolution of the construction industry.”
Walmart is emerging as a leader among the few mainstream brands embracing 3D construction printing. Coffee giant Starbucks also plans to open its first 3D-printed store in Brownsville, Texas. As the technology’s maturity and cost-effectiveness continue to be validated, 3D construction printing is reshaping the paradigm of commercial space construction, ushering in a new era of efficient and environmentally friendly building.
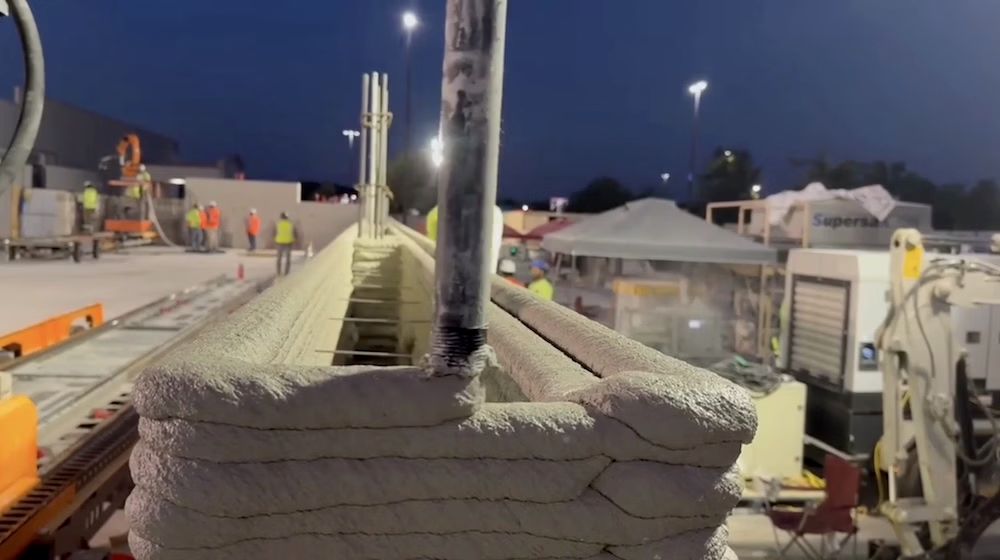
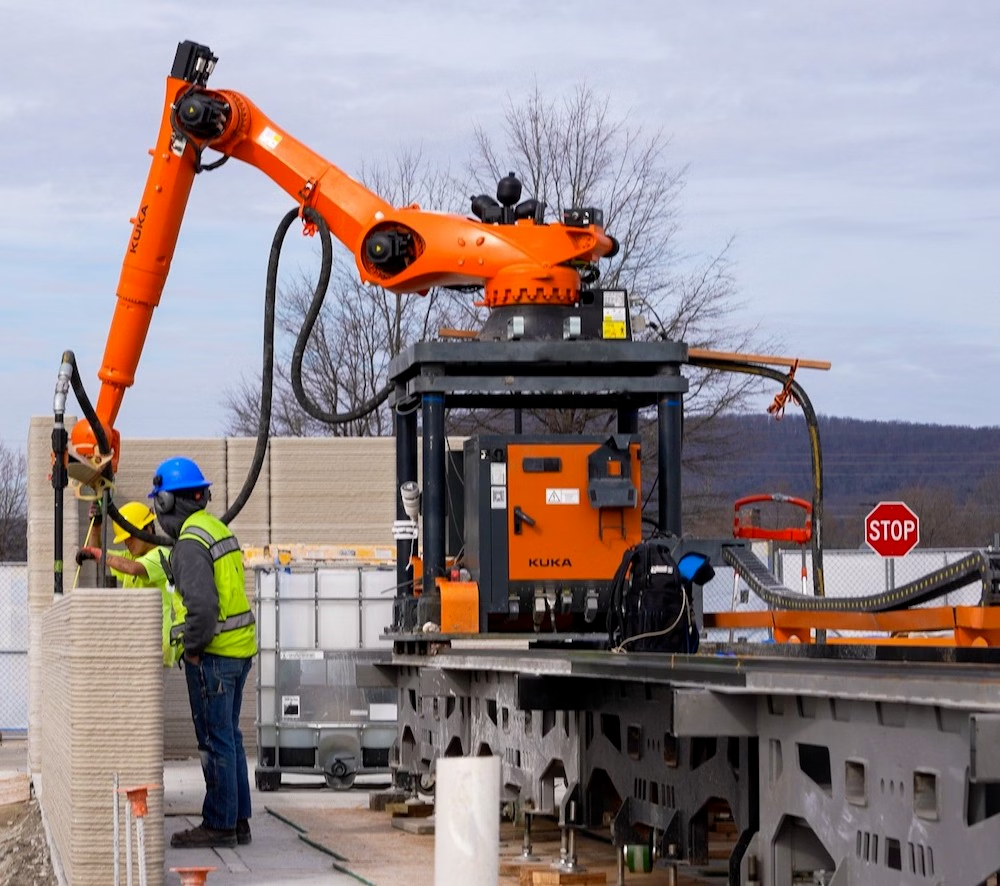
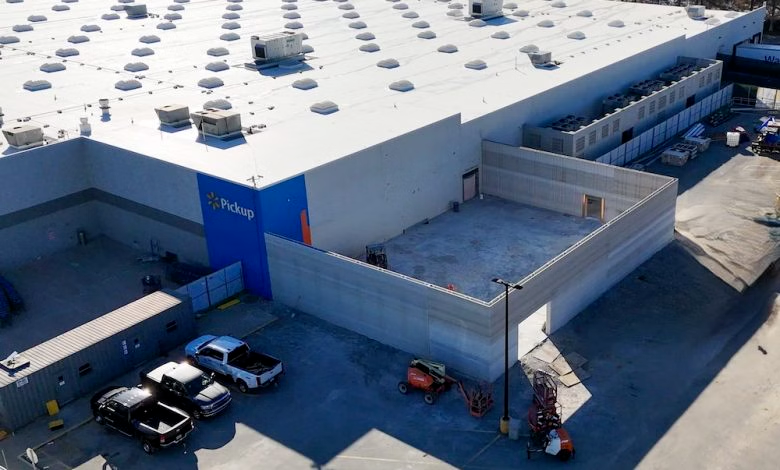
For more information, please contact Debaolong Seiko. You are also welcome to upload your designs to Debaolong Seiko for a quote.